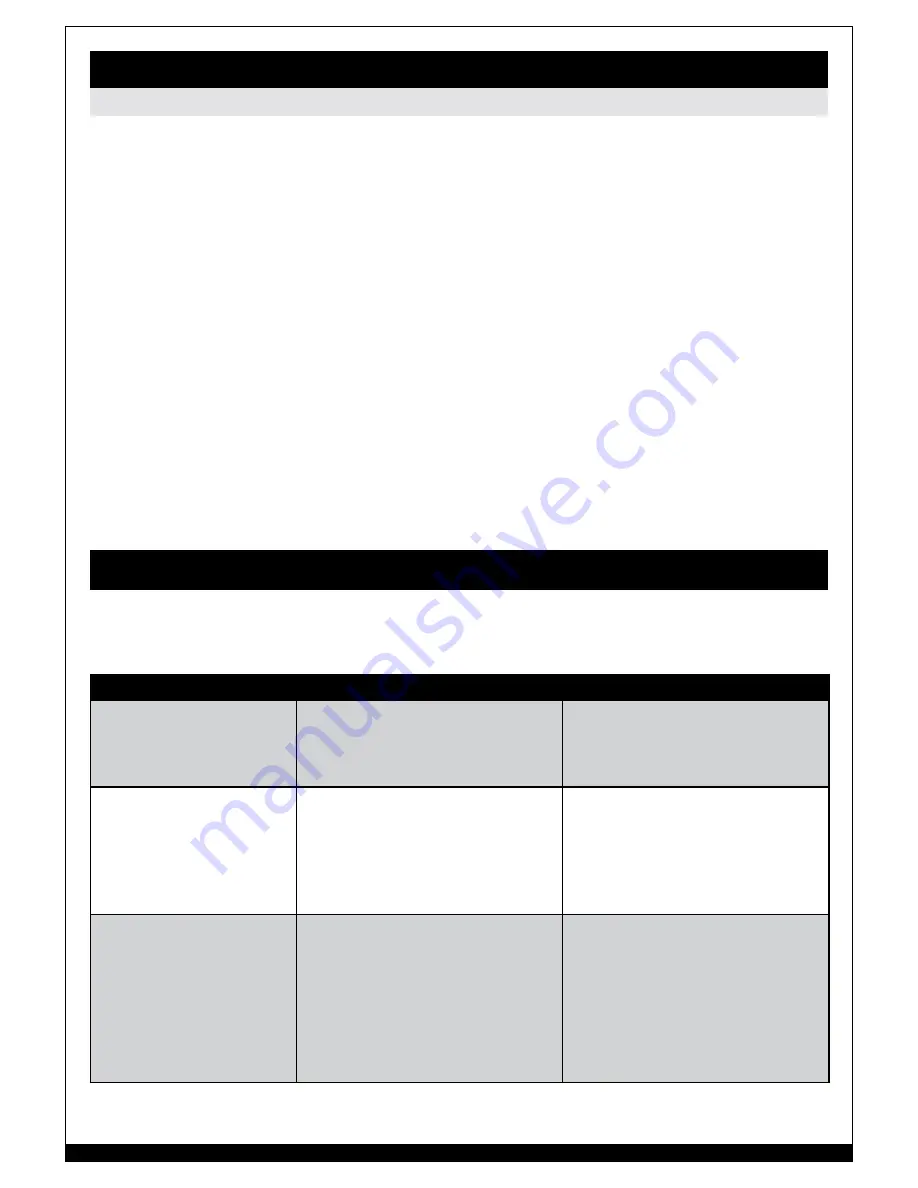
21
WWW.FORNEYIND.COM
• Always weld clean, dry and well-prepared material.
• Hold gun at a 45° angle to the workpiece with nozzle about 1/2” from the surface.
• Move the gun smoothly and steadily as you weld.
• Avoid welding in very drafty areas. A weak, pitted and porous weld will result due to air
blowing away the protective welding gas.
• Keep wire and wire liner clean. Do not use rusty wire.
• Sharp bends or kinks in the welding cable should be avoided.
• Always try to avoid getting particles of metal inside the machine since they could cause short
circuits or other damage.
• If available, use compressed air to periodically clean the hose liner, especially when
changing wire spools.
NOTE:
Disconnect from power source when carrying out this
operation.
• Using low pressure air (3/5 Bar=20-30 PSI), occasionally blow the dust from the inside of
the welder. This keeps the machine running cooler.
NOTE:
Do not blow air over the printed
circuit board and electronic components.
• The wire feed roller will eventually wear during normal use. With the correct tension the
pressure roller must feed the wire without slipping. If the pressure roller and the wire feed
roller make contact when the wire is in place between them, the wire feed roller must be
replaced.
• Check all cables periodically. They must be in good condition and not cracked.
This chart will assist you in resolving common problems you may encounter. These are not all the
possible solutions.
PROBLEM
POSSIBLE CAUSE
POSSIBLE SOLUTION
No “power” from welder.
Input cable or plug malfunction.
Wrong size fuse.
Check for proper input cable
connection.
Check fuse and replace as
necessary.
Fan operates normally, but
when gun trigger pulled,
there is no wire feed, weld
output or gas flow.
Faulty trigger gun.
Thermostat intervention.
Replace torch trigger.
Allow welder to cool. When the
pilot lamp/switch on the front panel
goes dark indicates the thermostat
has closed.
Feed motor operates but
wire will not feed.
Faulty wire feeding motor (rare).
Insufficient feed roller pressure.
Burr on end of wire.
Liner blocked or damaged.
Replace wire feeding motor.
Increase roller pressure.
Re-cut wire square with no burr.
Clear with compressed air or
replace liner.
Maintenance & Servicing
General Maintenance
Troubleshooting
Summary of Contents for MAXFire 140
Page 2: ......
Page 24: ...24 WWW FORNEYIND COM Wiring Diagram...
Page 26: ...26 WWW FORNEYIND COM Parts Diagram...
Page 27: ...27 WWW FORNEYIND COM Parts Diagram...
Page 30: ...30 WWW FORNEYIND COM...
Page 57: ...57 WWW FORNEYIND COM Sch ma des pi ces...
Page 58: ...58 WWW FORNEYIND COM Sch ma des pi ces...
Page 87: ...87 WWW FORNEYIND COM Diagrama de piezas...
Page 88: ...88 WWW FORNEYIND COM Diagrama de piezas...
Page 91: ......
Page 92: ...Forney Industries Inc 2057 Vermont Drive Fort Collins CO 80525 800 521 6038 www forneyind com...