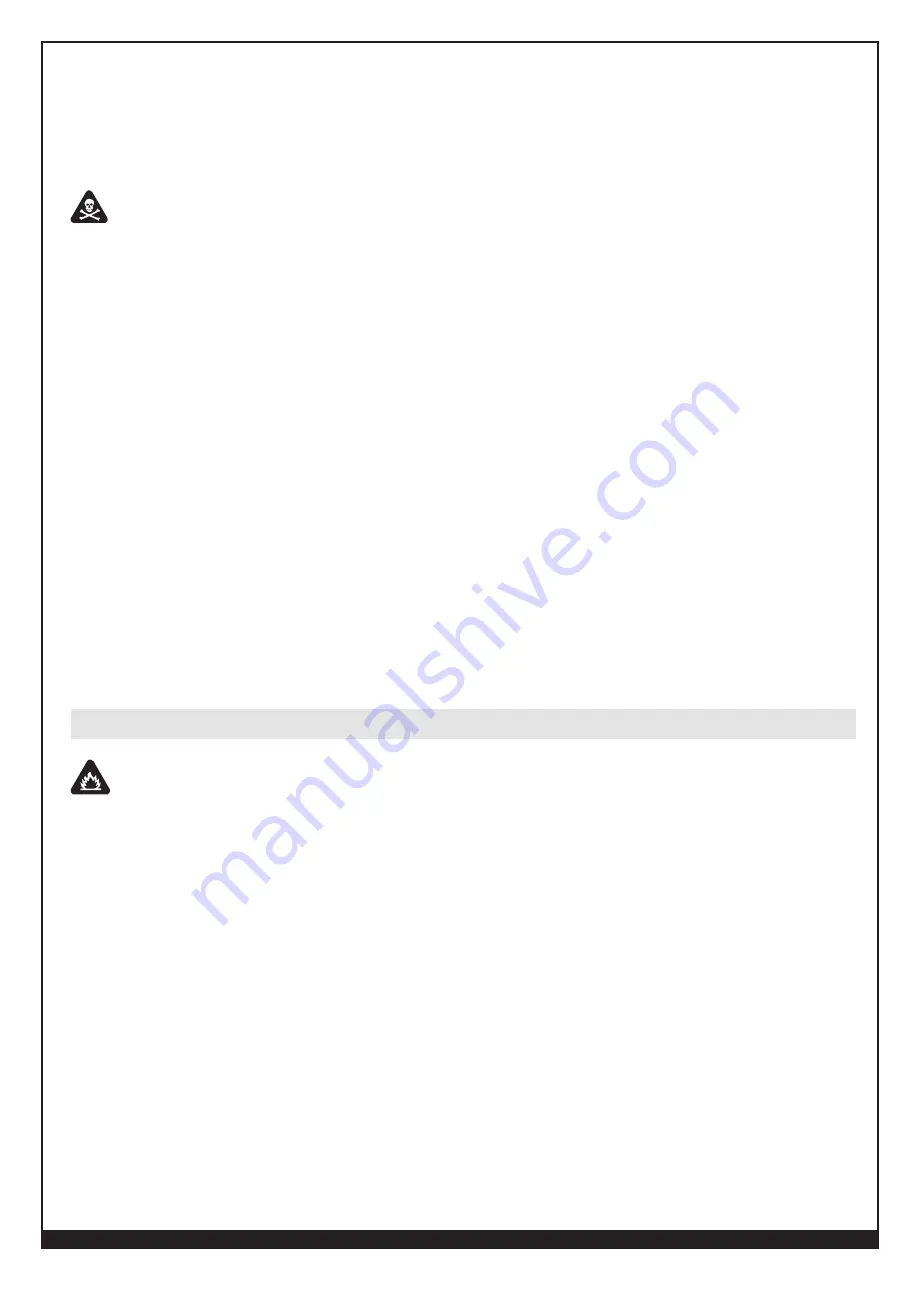
7
WWW.FORNEYIND.COM
•
background exists in your welding area, either remove it or cover it with something non-flammable and non-
reflective. Reflective arc rays can also cause skin burn in addition to eye injury.
•
Flying sparks can injure. Wear proper safety equipment to protect eyes and face. Shape tungsten electrode on
grinder wearing proper protection and in a safe location. Keep flammables away and prevent fire from flying
sparks.
FUMES, GASSES, AND VAPORS CAN CAUSE DISCOMFORT, ILLNESS, AND DEATH!
To reduce the risk, read, understand, and follow the safety instructions. In addition, make certain that anyone else that
uses this welding equipment or is a bystander in the welding area, understands and follows these safety instructions as
well.
•
Read and understand manufacturers Safety Data Sheets (SDS) and Material Safety Data Sheets (MSDS).
•
Do not weld in an area until it is checked for adequate ventilation as described in ANSI standard Z49.1. If
ventilation is not adequate to exchange all fumes and gasses generated during the welding process with fresh air, do
not weld unless you (the welder) and all bystanders are wearing air-supplied respirators.
•
Do not heat metals coated with, or that contain, materials that produce toxic fumes (such as galvanized steel), unless
the coating is removed. Make certain the area is well ventilated, and the operator and all bystanders are wearing
air-supplied respirators.
•
Do not weld, cut or heat lead, zinc, cadmium, mercury, beryllium, antimony, cobalt, manganese, selenium, arsenic,
copper, silver, barium, chromium, vanadium, nickel, or similar metals without seeking professional advice and
inspection of the ventilation of the welding area. These metals produce extremely toxic fumes which can cause
discomfort, illness and death.
•
Do not weld or cut in areas that are near chlorinated solvents. Vapors from chlorinated hydrocarbons, such as
trichloroethylene and perchloroethylene, can be decomposed by the heat of an electric arc or its ultraviolet radiation.
These actions can cause phosgene, a highly toxic gas to form, along with other lung and eye- irritating gasses. Do
not weld or cut where these solvent vapors can be drawn into the work area or where the ultraviolet radiation can
penetrate to areas containing even very small amounts of these vapors.
•
Do not weld in a confined area unless it is being ventilated or the operator (and anyone else in the area) is wearing
an air-supplied respirator.
•
Stop welding if you develop momentary eye, nose, or throat irritation as this indicates inadequate ventilation.
Stop work and take necessary steps to improve ventilation in the welding area. Do not resume welding if physical
discomfort persists.
Fire Prevention
FIRE OR EXPLOSION CAN CAUSE DEATH, INJURY, AND PROPERTY DAMAGE!
To reduce these
risks, read, understand and follow the safety instructions. In addition, make certain that anyone else that uses this welding
equipment, or is a bystander in the welding area, understands and follows these safety instructions as well. Remember:
arc welding by nature produces sparks, hot spatter, molten metal drops, hot slag and hot metal parts that can start fires,
burn skin and damage eyes.
• Do not wear gloves or other clothing that contains oil, grease, or other flammable substances.
• Do not wear flammable hair preparations.
• Do not touch the hot weld bead or weld puddle until fully cooled.
• Do not weld in an area until it is checked and cleared of combustible and/or flammable materials. Be aware that
sparks and slag can fly 35 feet and can pass through small cracks and openings. If work and combustibles cannot be
separated by a minimum of 35 feet, protect against ignition with suitable, snug-fitting, fire resistant, covers or shields.
• Do not weld on walls until checking for and removing combustibles touching the other side of the walls.
• Connect the ground cable to the workpiece as close as possible to the welding area. Do not connect ground cables
to building framing or other locations away from the welding area. This increases the possibility of welding current
passing through alternate circuits, creating fire hazards and other safety hazards.
• Do not weld, cut, or perform other such work on used barrels, drums, tanks, or other containers that had a flammable
or toxic substance. The techniques for removing flammable substance and vapors, to make a used container safe for
welding or cutting, are quite complex and require special education and training.
• Do not strike an arc on a compressed gas or air cylinder, and never allow any electrically “hot” parts to touch a
cylinder. Doing so will create a brittle area that can result in a violent rupture immediately or at a later time as a result
of rough handling.
• Ensure any compressed gas cylinders in the work area have properly operating regulators rated for the gas and