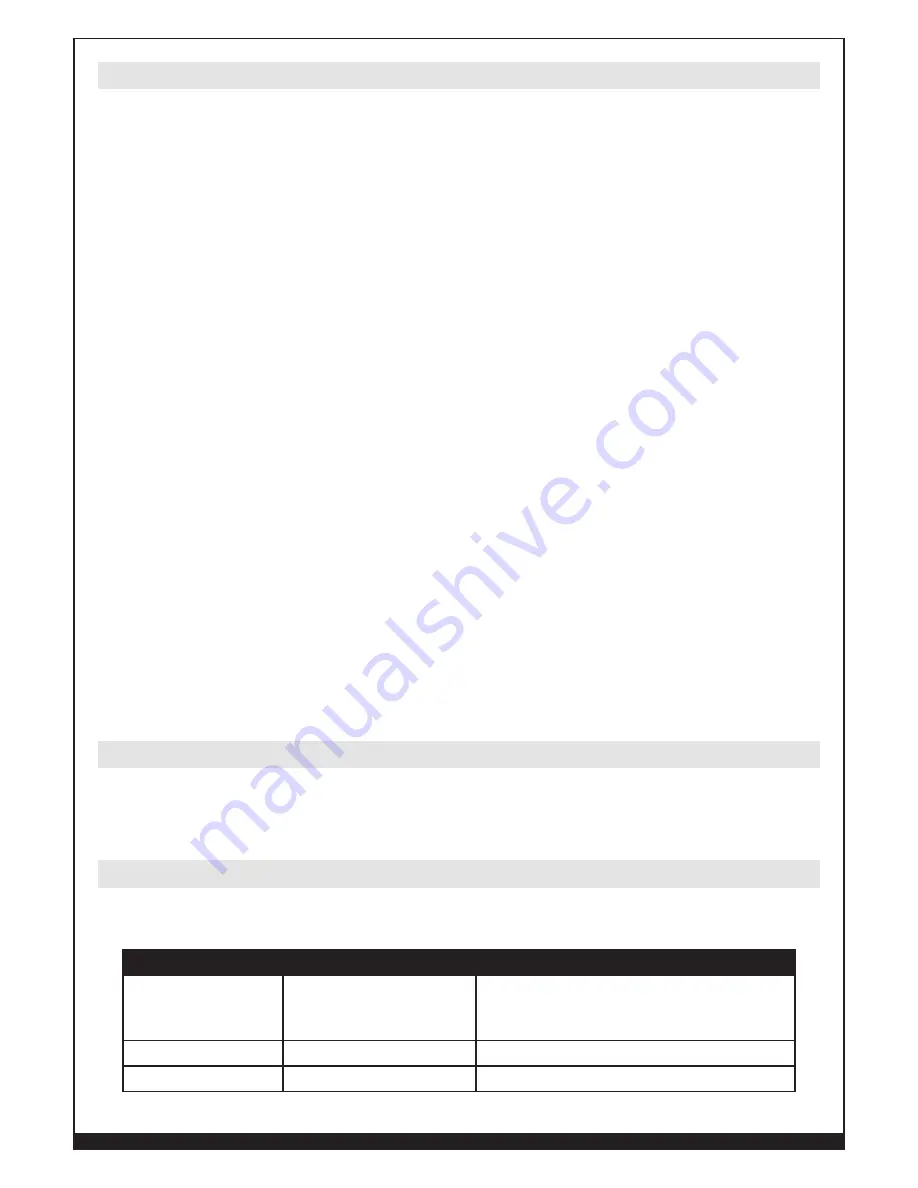
22
WWW.FORNEYIND.COM
Some experience is required to adjust and use a MIG welder. In MIG welding two parameters are
fundamental: the welding voltage and the wire speed. The resulting welding current is a result of these
two settings.
• Set the voltage and wire feed controls to positions suitable for the thickness of the material
to be welded. Welding current varies in relationship to wire feed speed. For low welding
current output, the wire feed speed potentiometer should be set at the low end of the wire
feed speed scale. Turning the wire feed speed control potentiometer clockwise will result
in increased wire feed speed and welding current. Welding voltage is adjusted to match
the wire feed speed (welding current). Progressively select higher voltage positions while
increasing wire speed.
Increasing welding voltage leads to a longer arc (without substantially affecting the current).
Conversely, a decreased welding voltage results in a shorter arc (the current again is not substancially
changed). A change in wire diameter results in changed parameters. A smaller diameter wire
requires an increase in wire feed speed to reach the same current. If certain limits are exceeded, a
satisfactory weld cannot be obtained. These are:
A) Feeding wire too fast (too high with regard to the welding voltage) results in pulsing within
the torch. This is because the wire electrode dips into the puddle and cannot be melted off fast
enough.
B) Setting welding voltage to high (too high with regard to the wire feed speed), will result in
excessive and unstable arc. Increase the voltage even higher and the contact tip will burn.
C) Excessive wire speed can be corrected through the arc voltage increase. The limit of this
adjustment depends on the thickness of the material to be welded (a certain limit exceeded
will result in burn through).
Place the torch on the joint you want to weld: the angle between the torch and the nozzle should be
around 45°. The distance between the torch and the work piece should be 5-1/2”. Lower the face
shield and press the torch trigger to start the arc. When the arc has struck, move the nozzle slowly
from left to right along the joint. Adjust the wire feed speed until the arc makes a “crisp” sound
(experience will help you to recognize the right sound).
This welder can work with Aluminum wire .030” (0.8mm) diameter, solid steel wire .023”- .035”
(0.6-0.9mm) diameter and stainless steel wire .030”-.035” (0.8-0.9mm) diameter (MIG Welding,
“GMAW”) and with flux core wires 0.9mm diameter (.035”) (FLUXCORE WIRE Welding, “FCAW”).
According to the material to be welded and to the wire you are going to use, select the shielding gas.
The table below can give you some useful indications:
MATERIAL TO WELD
GAS CYLINDER
WIRE
Mild Steel
Argon + CO2
Cylinder or CO2 Cylinder
Copper coated mild steel wire spool. For
FLUXCORE WIRE Welding, “FCAW” use
flux-cored wire spool
Stainless Steel
Argon Cylinder
Stainless Steel wire spool
Aluminum
Argon Cylinder
Aluminum wire spool
Factors to Consider for Best Welding Results
Welding Wire Selection
Gas Selection