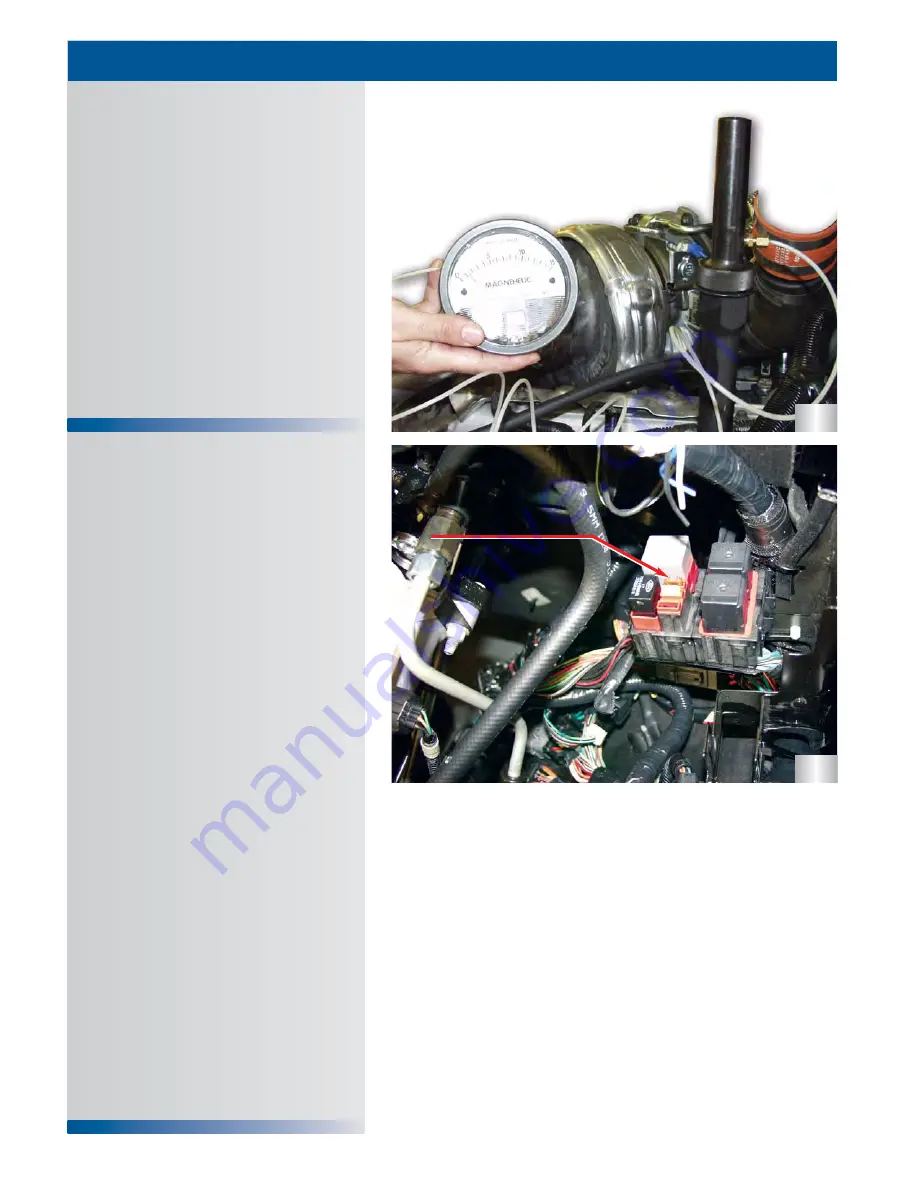
168
169
• Every time the key is cycled to the on
position, the injectors should buzz.
• If no buzz is heard one of the following
conditions may be present:
a) No power or ground to the FICM or
PCM.
b) No CAN communication between the
FICM and the PCM.
c) V-ref shorted to ground.
d) Bad PCM or FICM.
e) All injectors bad or wiring to all
injectors bad (not likely).
• If the injectors do buzz and all conditions are
met for the engine to run but the injectors do
not fire during crank, check the FICM logic
power feed to the FICM.
• To check powers and grounds to the FICM
you can bring up the following pids on the
WDS:
FICMVPWR (FICM Vehicle Power battery
voltage)
FICMMPWR (FICM Main Power or output
voltage approximately 48 volts)
FICMLPWR (FICM Logic Power battery
voltage)
• A new crankcase pressure orifice tool has
been developed for the 6.0L
Power Stroke.
•
The new tool has a smaller orifice in the top
so that more accurate readings could be
taken with the 0-60” gauge on the gauge
bar.
• When using the new tool on the 6.0L
Power
Stroke
the maximum reading for a good
engine is 8” of water.
Crankcase Pressure Test
G E N E R A L D I A G N O S T I C S
82
Injector Buzz/No Buzz
FICM LOGIC FUSE
FICM LOGIC FUSE
Summary of Contents for 6.0L POWER STROKE
Page 1: ... F Series Super Duty ...
Page 3: ...This page intentionally left blank ...
Page 5: ...This page intentionally left blank ...
Page 6: ...1 Direct Injection Turbocharged Diesel Engine 6 0L Power Stroke ...
Page 17: ...16 This page intentionally left blank ...
Page 49: ...48 This page intentionally left blank ...
Page 91: ...W I R I N G D I A G R A M S I N G L E A LT 90 ...
Page 92: ...W I R I N G D I A G R A M S I N G L E A LT 91 ...
Page 93: ...W I R I N G D I A G R A M D U A L A LT 92 ...
Page 94: ...W I R I N G D I A G R A M D U A L A LT 93 ...
Page 104: ...N O T E S 103 ...
Page 105: ...N O T E S 104 ...
Page 106: ...2002 International Truck and Engine Corporation Printed in the U S A ...