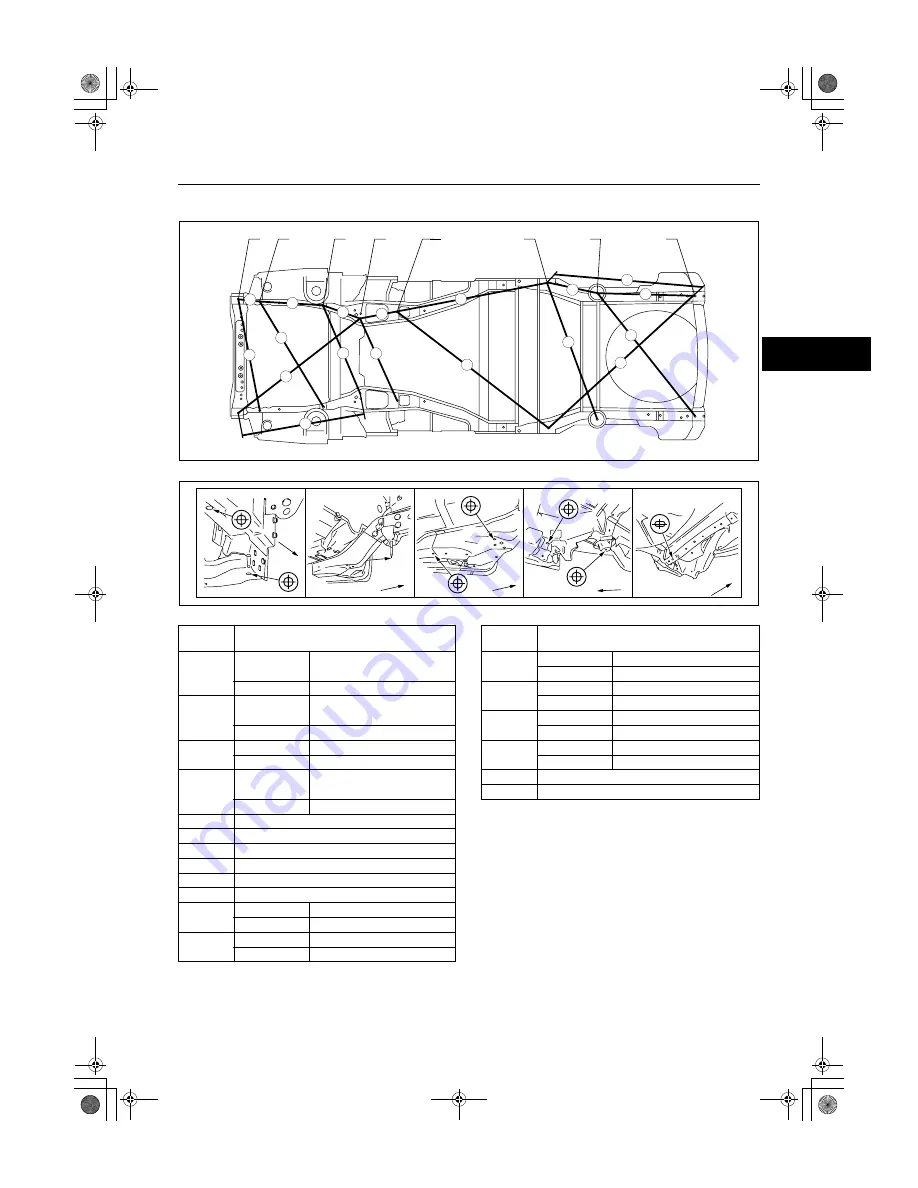
BODY STRUCTURE [DIMENSIONS]
09-80D–5
80D
UNDERBODY STRAIGHT-LINE DIMENSIONS[DIMENSIONS]
id098010740500
.
End Of Sie
BM: FRONT BODY
A
B
D
E
F
G
I
J
9
8
7
5
4
3
1
2
6
18
17
15
16
14
13
11
12
10
BUE0980B043
G,I
G
E
A
B
F
I
A,B
D
E,F
J
Fr
Fr
Fr
Fr
Fr
BUE0980B044
Measured
location
Dimensions mm {in}
1
R.H.D. models
RH:214 {8.42},
LH:215 {8.46}
L.H.D. models
156 {6.14}
2
R.H.D. models
RH:1,023 {40.27},
LH:1,032 {40.62}
L.H.D. models
1,037 {40.83}
3
R.H.D. models
558 {21.96}
L.H.D. models
628 {24.72}
4
R.H.D. models
RH:1,105 {43.50},
LH:1,096 {43.14}
L.H.D. models
1,154 {45.43}
5
1,357 {53.42}
6
1,063 {41.85}
7
345 {13.58}
8
867 {34.15}
9
430 {16.94}
10
859 {33.82}
11
R.H.D. models
1,262 {49.68}
L.H.D. models
1,264 {49.77}
12
R.H.D. models
1,602 {63.07}
L.H.D. models
1,612 {63.46}
13
R.H.D. models
425 {16.73}
L.H.D. models
428 {16.85}
14
R.H.D. models
1,229 {48.38}
L.H.D. models
1,243 {48.94}
15
R.H.D. models
1,144 {45.03}
L.H.D. models
1,145 {45.08}
16
R.H.D. models
1,613 {63.50}
L.H.D. models
1,623 {63.91}
17
721 {28.39}
18
1,294 {50.94}
Measured
location
Dimensions mm {in}
Summary of Contents for 2006 Escape J87R
Page 1: ......
Page 4: ......
Page 26: ......
Page 61: ...BODY STRUCTURE WATER PROOF AND RUST PREVENTIVE 09 80C 3 80C BUE0980B037...
Page 62: ...09 80C 4 BODY STRUCTURE WATER PROOF AND RUST PREVENTIVE BONNET DOOR LIFTGATE BUE0980B038...
Page 63: ...BODY STRUCTURE WATER PROOF AND RUST PREVENTIVE 09 80C 5 80C L H D models BUE0980B071...
Page 64: ...09 80C 6 BODY STRUCTURE WATER PROOF AND RUST PREVENTIVE End Of Sie BUE0980B072...
Page 66: ...09 80C 8 BODY STRUCTURE WATER PROOF AND RUST PREVENTIVE L H D models End Of Sie BUE0980B073...
Page 68: ......
Page 90: ......