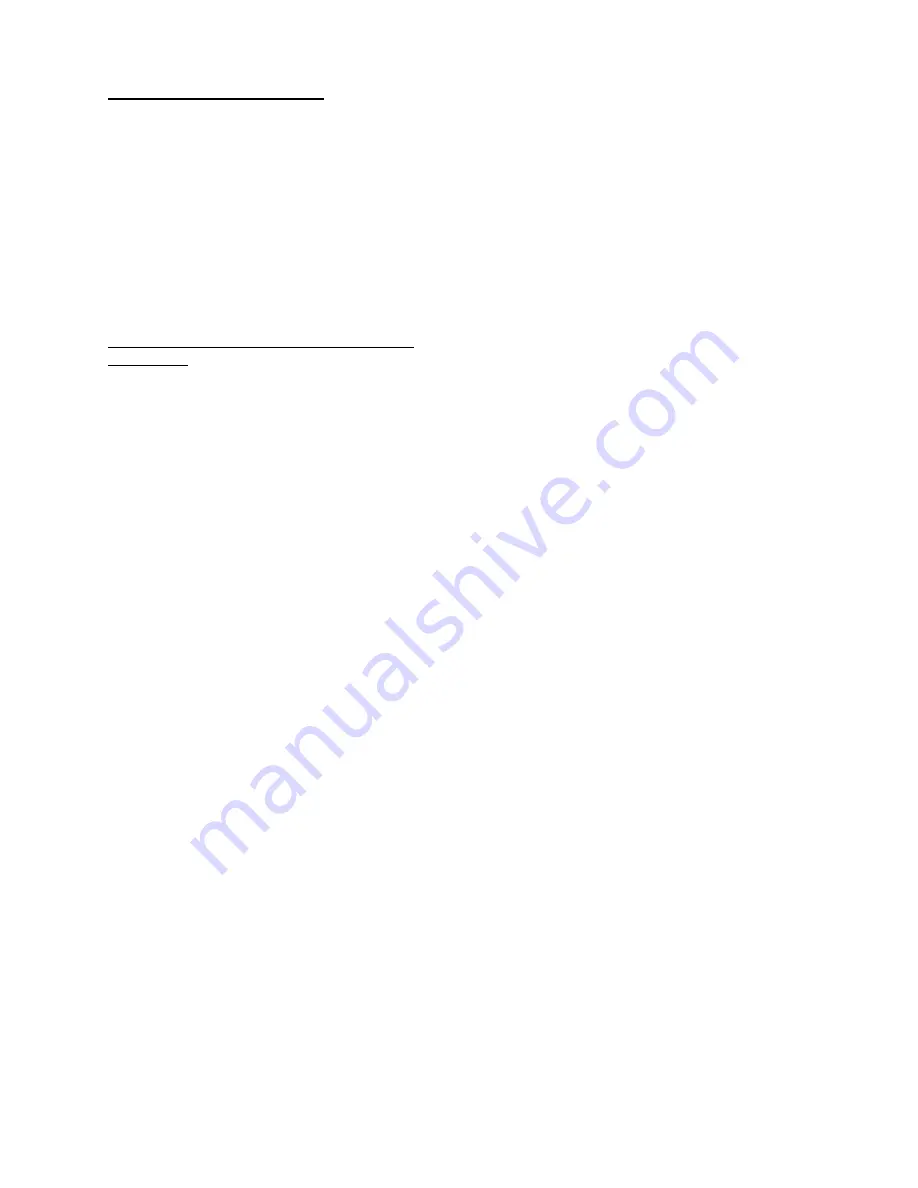
41
x: System Start-Up
(continued)
D.
ADJUST CONTROL SETTINGS
with burner
service switch turned “ON”.
1. SET ROOM THERMOSTAT about 10°F below
room temperature.
2. PRESS RED RESET BUTTON on burner primary
control, hold for ten (10) seconds and release to
reset the control.
3. CHECKOUT
Put the system into operation and observe at least
one complete cycle to make sure that the controller
operates properly. See Troubleshooting Section to
use LED to assist in determining system operation.
E.
CHECK / ADJUST OIL BURNER BEFORE
STARTING.
Natural Vent Applications:
1.
Beckett AFG Burners
a. Verify nozzle size, head size, gun setting, and
positioning of electrodes. This information is
shown in Figure 33, and Beckett AFg Burner
Specifications, Table 9.
b. Inspect Beckett head setting on left side of
burner housing by insuring the blue line MD(V1)
or the line on the label MB(L1) are aligned,
readjust if necessary. Refer to Figure 33 and
Table 9 at the end of this manual.
c. Check burner air band and air shutter settings.
Readjust if necessary, see Beckett AFg Burner
Specifications, Table 9 at the end of this manual.
d. OPEN ALL SHUT-OFF VALVES in the oil
supply line to the burner.
e. ATTACH A PLASTIC HOSE TO FUEL PUMP
VENT/BLEED FITTINg and place the other
hose end into an empty container to catch the oil.
f. SLIgHTLY OPEN FLAME OBSERVATION
PORT COVER on burner swing door, enough to
insert draft gauge probe later.
Direct Vent Applications:
2.
Beckett NX Burners
a. Verify nozzle size, gun setting and positioning of
electrodes. See Figures 34 and 36 and Beckett
NX Burner Specifications, Table 10 at the end of
this manual.
b. Remove burner cover by loosening the four
thumb screws and set aside.
c. Disconnect the copper oil connector tube from
nozzle line.
d. Loosen the two screws securing igniter-retaining
clips and rotate both clips to release the igniter
baseplate. The igniter should pop-up and would
be supported by the prop spring.
e. Loosen the two screws securing the rear door,
then swing to the right and down.
f. Loosen splined nut.
g. Lift up the igniter baseplate and simultaneously
remove nozzle line assembly from burner
by drawing it straight back out the rear door
opening. Be careful not to damage the electrodes
or insulators while handling.
h. Check electrodes to comply with dimensions
shown in Figure 34. For adjustment, loosen the
electrode clamp screw and slide/rotate electrodes
as needed. Securely re-tighten the clamp screw
when finished.
i. Check retention head alignment. Cad cell
sighting holes in the throttle cup and retention
head must line up, so the cad cell can see the
flame. Make sure that, the “stamped key” in the
retention head collar lines up with the “keyway”
in the nozzle adapter, when mounting the
retention head. See Figure 35.
j. To re-install the nozzle line assembly, reverse
procedure outlined in steps f thru b.
k. Upon reinstallation of the nozzle line assembly,
check that head/air plate setting number
pointer lines up with a number on the scale,
which matches a value shown in Table 10 for a
particular boiler/burner model.
The zero calibration has been factory set; the
upper left acorn nut locks retention head at
“0” position. If the zero calibration has to be
reset, follow the adjustment procedure, outlined
at “Prepare Burner & Site” section of Beckett
Model NX Oil Burner Instruction Manual, Form
Number 610BNX. Make sure the retention head
is securely against the stops in the retention ring,
when the adjustment plate pointer is at “0”.
l. The rear door must be kept tightly closed upon
reinstallation of the nozzle line assembly.
m. Loosening the splined nut and lower acorn nut,
and, turning the adjustment screw, either forward
or, rearwards, will adjust the head/air plate. DO
NOT LOOSEN UPPER LEFT ACORN NUT,
which locks zero head/air setting. See Figure 36.
n. OPEN ALL SHUT-OFF VALVES in the oil
supply line to the burner.
o. ATTACH A PLASTIC HOSE TO FUEL PUMP
VENT/BLEED FITTINg and place the other
hose end into an empty container to catch the oil.
p. SLIgHTLY OPEN FLAME OBSERVATION
PORT COVER on burner swing door, enough to
insert draft gauge probe later.
Summary of Contents for FORCEOL Series
Page 58: ...58 Jacket Assembly XV Repair Parts continued...
Page 60: ...60 Water Boilers Trim and Controls XV Repair Parts continued...
Page 62: ...62 Beckett AFG Burner XV Repair Parts continued...
Page 64: ...64 Beckett NX Burner XV Repair Parts continued...
Page 70: ...70...
Page 71: ...71...
Page 72: ...72...