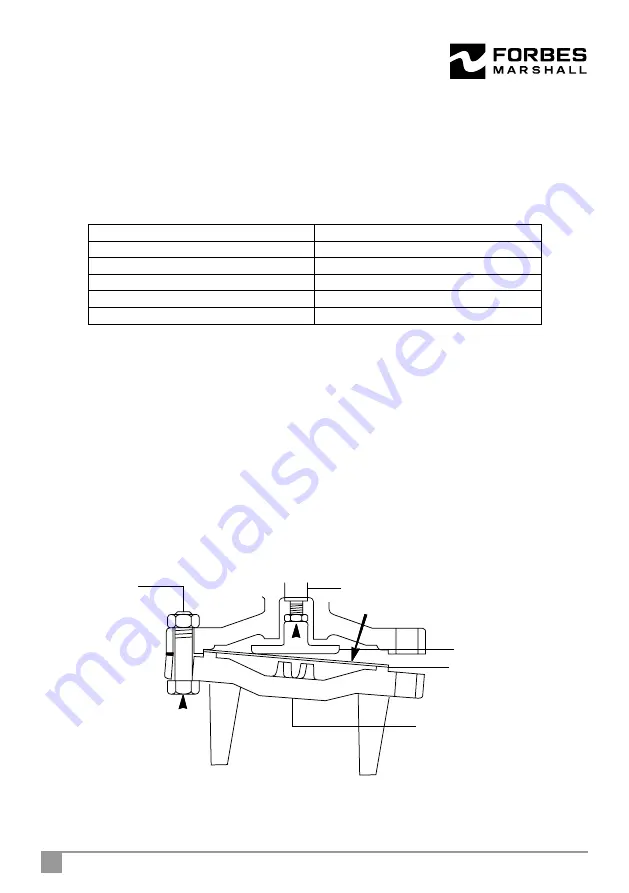
26
Forbes Marshall Pilot Operated Pressure Reducing Valve
4.
Refit the pushrod assembly.
5.
Refit the main valve head, make sure valve locates on seat.
6.
Check the valve lift shown in Table 3 using a depth gauge and adjust if necessary
byscrewing the pushrod in or out of the diaphragm plate.
Table 3 : VALVE LIFT FMPRV41 STEAM/AIR
For this section refer to figure 21
7.
Thoroughly clean the lower diaphragm chamber
(4)
making sure contact faces are
clean.
8.
Replace the diaphragm plate
(2)
and pushrod assembly
(1)
and loosely fit the lower
diaphragm chamber on two bolts
(5)
either side of the union connection to locate the
spigot in the recess.
9.
Refit the diaphragms
(3)
in exactly the same way as when they were dismantled.
10. Push the lower diaphragm chamber
(4)
home to locate in the recess and refit the M12
nuts and bolts. Progressively and evenly tighten to a torque of 80 - 100 N m.
11. Retighten the long union nut to ensure a steam tight seal.
Figure 21: Resetting the main valve pushrod
Size of Valve
Valve Lift
DN15
1.8
DN20
2.3
DN25
2.8
DN40
4.3
DN50
4.8
M12 bolts (5)
Push rod
assembly (1)
Diaphragm plate (2)
Main Diaphragms (3)
Lower diaphragm
chamber (4)