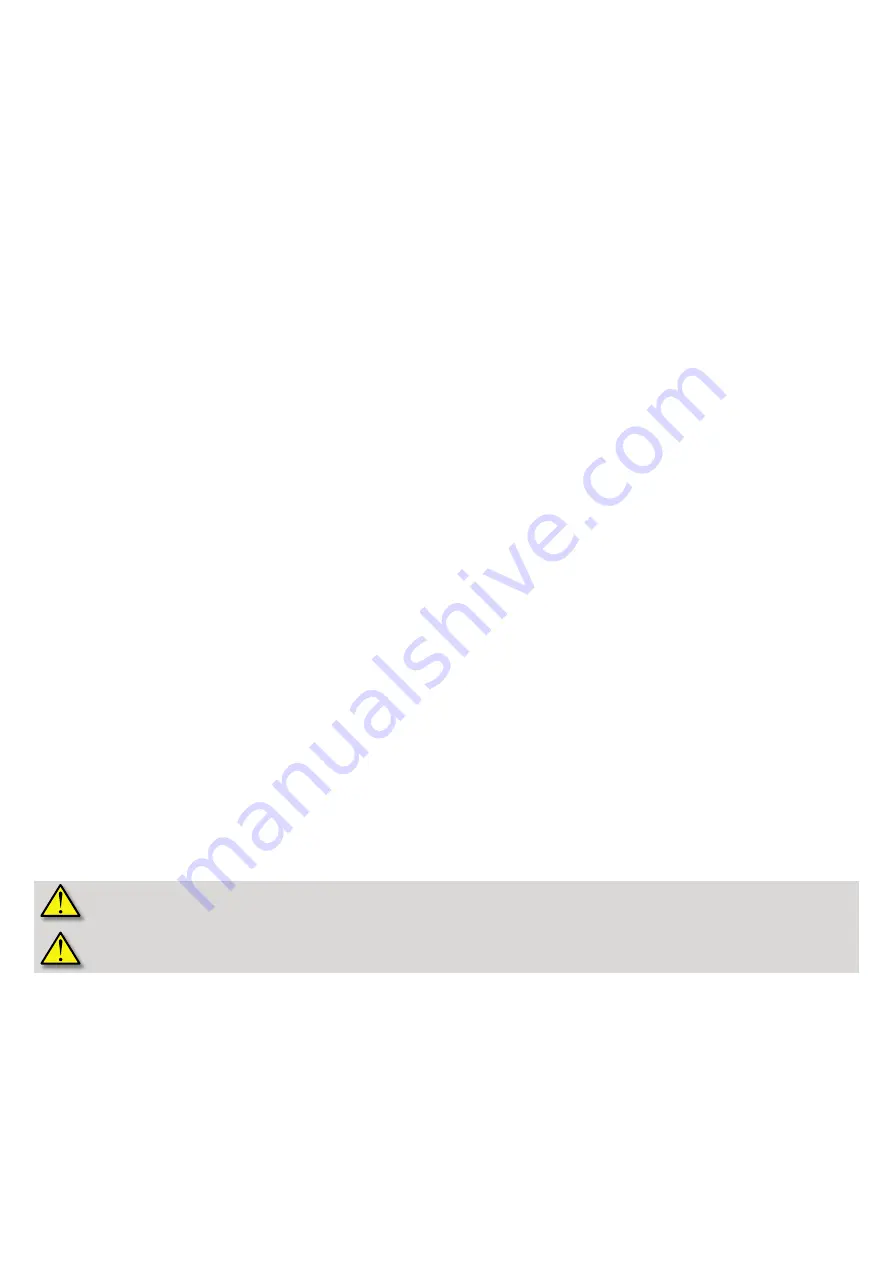
3
General information for fitters, maintenance technicians and users
This INSTRUCTION MANUAL, which is an integral and indispensable part of the product, must be handed over to the user by the in-
staller and must be kept in a safe place for future reference. The manual must accompany the boiler should it be sold or its possession
transferred. Following to the boiler installation, the fitter is to advise the user about boiler operation and its safety devices.
This boiler must be used for the purposes for which it has been intended.
Any other use shall be considered incorrect and therefore dangerous.
The boiler must be installed by qualified personnel, in compliance with applicable laws and standards and according to the manufac-
turer’s instructions given in this manual. Incorrect installation may cause injury to persons and/or animals and damage to property. The
manufacturer shall not be held liable for any such injury and/or damage.
Damage and/or injury caused by incorrect installation or use and/or damage and/or injury due to non-observance of the manufacturer’s
instructions shall relieve the manufacturer from any and all contractual and extra-contractual liability.
Before installing the boiler, check that the technical data correspond to the requirements for its correct use in the system.
Check that the boiler is intact and it has not been damaged during transport and handling: do not install equipment which is damaged
and/or faulty.
Do not obstruct the air suction openings.
Only manufacturer approved and supplied accessories or optional kits (including electric ones) are to be installed.
Properly dispose of the packaging as all the materials can be recycled. The packaging must therefore be sent to specific waste manage-
ment sites.
Keep the packaging out of the reach of children as it may represent a source hazard.
In the event of failure and/or faulty functioning, switch off the boiler. Do not attempt to make repairs: contact qualified technicians.
Manufacturer approved and supplied parts must be used for all repairs to the boiler.
Non-observance of the above requirements may affect the safety of the boilers and endanger people, animals and property.
The manufacturer, in order to guarantee efficient and correct functioning of the equipment, recommends the boiler to be serviced and
repaired by an authorized Service Centre which is best trained for the purpose.
Routine boiler maintenance is to be performed according to the schedule indicated in the relevant section of this manual.
Appropriate boiler maintenance ensures efficient operation, environment preservation, and safety for people, animals and
objects.
In the event of long periods of inactivity of the boiler, disconnect it from power mains and close the gas tap.
Warning! When power mains are disconnected, boiler electronic anti-frost function will not be operative.
Should there be a risk of freezing, add anti-frost: it is not advisable to empty the system as this may result in damage; use specific anti-
frost products suitable for multi-metal heating systems.
IMPORTANT
Should you smell gas:
- do not turn on or off electric switches and do not turn on electric appliances;
- do not ignite flames and do not smoke;
- close the main gas tap;
- open doors and windows;
- contact a Service Centre, a qualified installer or the gas supply company.
Never use flames to detect gas leaks.
The boiler is designed for installation in the country indicated on the technical data plate: installation in any other
country may be source of danger for people, animals and objects.
Summary of Contents for TAHITI CONDENSING KC24
Page 1: ...IST 03 C 234 01 INSTALLATION USE AND MAINTENANCE TAHITI CONDENSING GB...
Page 38: ...38...
Page 39: ...39...