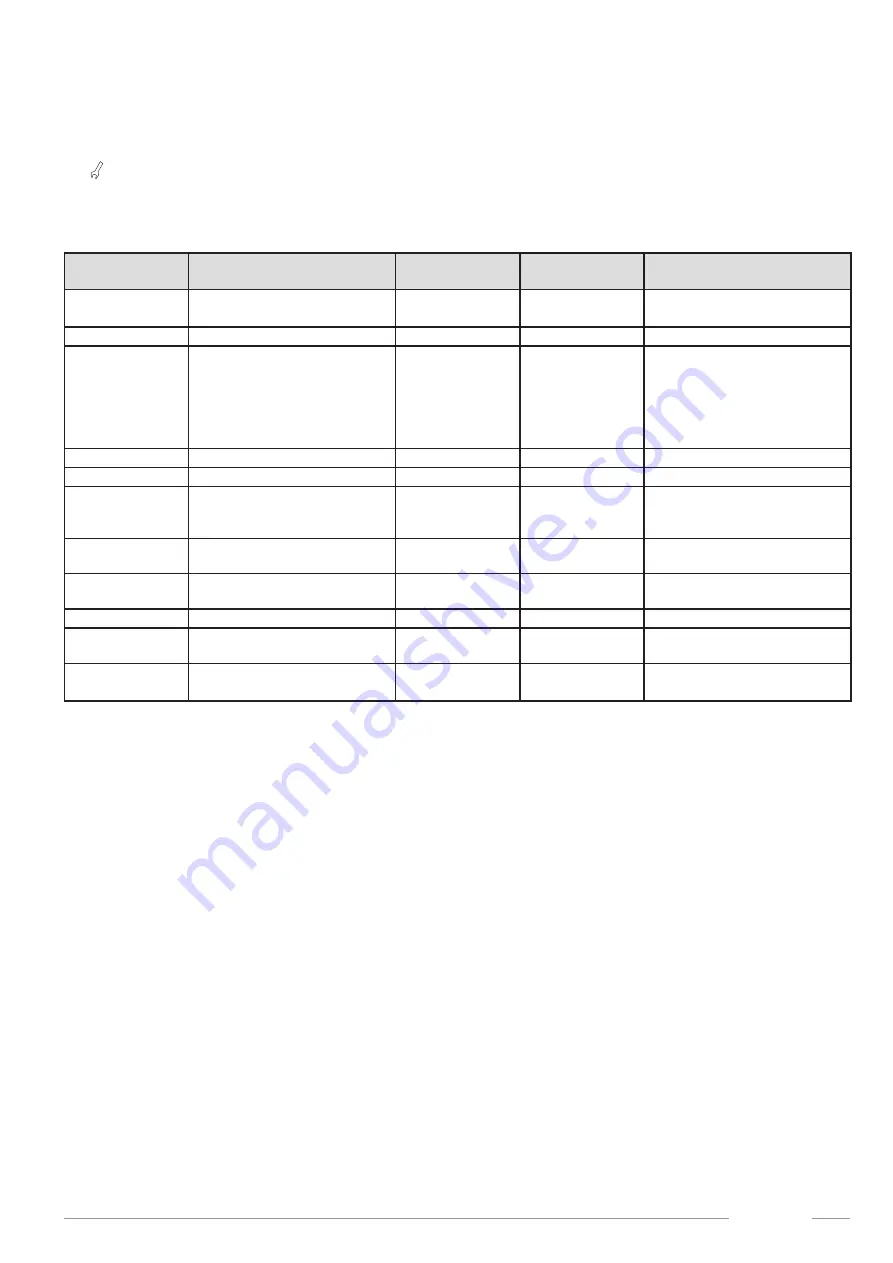
Instructions for the installer
39
3.13 TSP parameters
The boiler operation is controlled by several parameters.
To change parameters, press the
Reset
and
- HEATING
buttons together for 3 seconds.
Scroll through the parameters by pressing
CH +/-
buttons.
As soon as you reach the one to be modified, press
ok
.
The symbol turns on to indicate that you can edit the parameter value.
The parameter value can be changed with the
+/- HEATING
buttons.
To confirm modification press
Ok
.
To exit the parameter editing mode press button
Reset
.
Parameter
Description
Configurable
value range
Default values
Notes
P0 - TSP0
Fuel gas type
0 ÷ 1
According to the
model
0 = natural gas
1 = lpg
P1 - TSP1
CH maximum output
0 ÷ 100%
100%
n.a.
P2 - TSP2
Ignition power setting
0 ÷ 100%
0%
If P2=0, ignition ramping is
implemented.
If P2≠0, the boiler operates at
the power set (P2=1 minimum
power ÷ P2=100 maximum
power)
P3 - TSP3
Heating thermostat timing
0 ÷ 10 min.
4
n.a.
P4 - TSP4
CH power rising ramp timer
0 ÷ 10 min.
4
n.a.
P5 - TSP5
Timer for CH post-circulation,
freeze protection and flue clea-
ning function
0 ÷ 180 sec.
30
n.a.
P7 - TSP7
Water hammer protection delay,
configurable
0 ÷ 3 sec.
0
n.a.
P8 - TSP8
Ambient thermostat/remote con-
trol reading delay
0 ÷ 199 sec.
0
n.a.
P18 - TSP18
Heating timer reset temperature
35 ÷ 78 °C
40 °C
n.a.
P19 - TSP19
Maximum ΔT between flow and
return
0 ÷ 78 K
30 K
0 = function disabled
P20
Default parameter setting (with
the exception of P0)
0 ÷ 1
0
0 = user's parameters
1 = default parameters
Tab. 11 Limits to be set for TSP parameters and default values in relation to boiler type (TSP0) - I