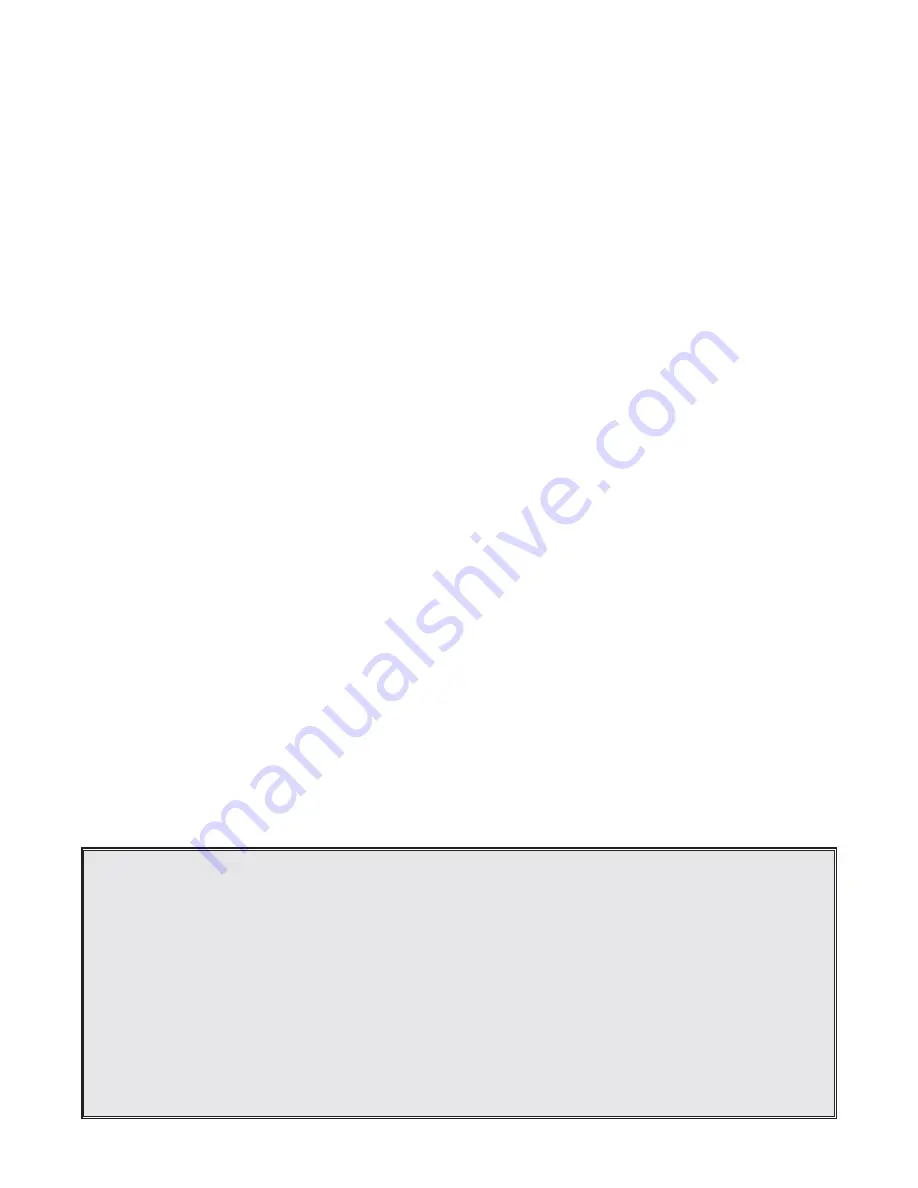
2
Follett Corporation
Equipment Return Policy
Follett equipment may be returned for credit under the following conditions:
1.
The equipment is new and unused.
2.
A return authorization number has been issued by customer service within 30 days after shipment.
3.
Follett receives the equipment at the factory in Easton, PA within 30 days after issuance of the return authorization number.
4.
The equipment must be returned in Follett packaging. If the packaging has been damaged or discarded, Follett will forward,
at the customer’s expense, new packaging.
Note:
Return freight charges are the responsibility of the customer. If equipment is returned and is damaged because of
improper packaging, Follett Corporation will not be held responsible.
Credit will be issued when:
The equipment has been inspected by Follett and deemed suitable to be returned to stock.
Note:
A 15% restocking charge will be deducted from the credit. If the cost to return the product to stock exceeds 15%, the
actual cost will be deducted.