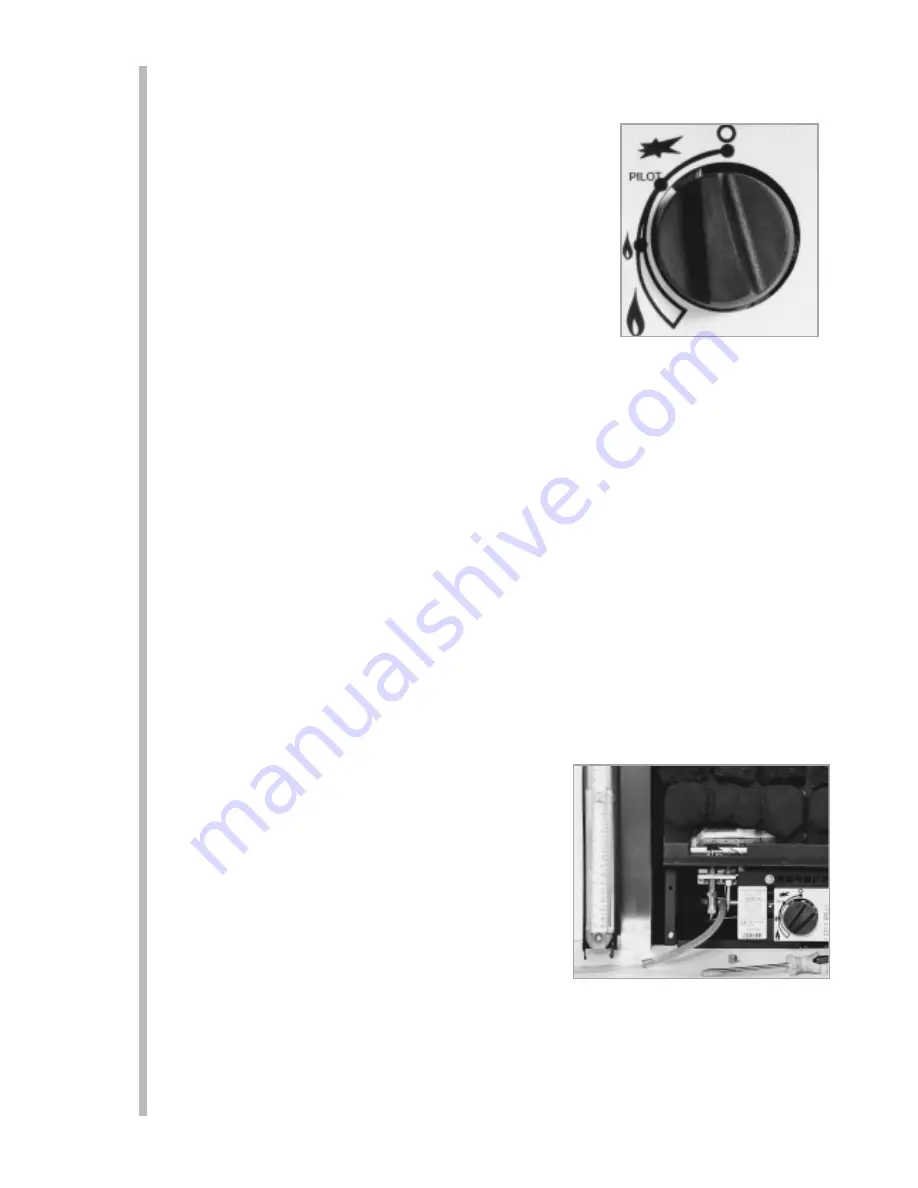
OPERATING THE FIRE
The pilot is visible through the underside of the left hand front coal strip.
Push in and turn the control knob to the SPARK position, and hold there for
a few seconds.
Continue turning anti-clockwise through the spark click to the PILOT light
position, ensuring the pilot has lit. If not, return the knob clockwise, and
repeat.
When the pilot lights after the spark, keep the knob depressed for
approximately ten seconds. Now release the knob and the pilot should stay
alight. If not, retry ignition. If the pilot is extinguished during use, wait three
minutes before repeating the ignition procedure.
To achieve the HIGH setting, push the control knob in slightly and continue turning anti-clockwise to the high
position. The main burner should light after a few seconds.
To decrease the setting to LOW, turn the control knob clockwise to the low setting.
To turn to the PILOT position from the HIGH or LOW positions, press the control knob in, and return to the pilot
position and release.
To turn the fire OFF, keep the knob pressed in, return to the off position and release.
SPARK FAILURE
The gap between the spark electrode and the pilot should be 3.5 - 4.5mm to produce a good spark. There should
be no need to adjust this. If under any circumstances the electric spark fails, the pilot may be lit manually by
proceeding with the ignition sequence as previously described, and after turning the control knob through the
spark position, the knob should be held in and the pilot lit with a taper.
FLAME CONTROL LEVER
On Natural Gas appliances there is a flame control lever behind the ashpan door that varies the flame colour from
blue to a decorative yellow. The customer should be instructed in it’s position and that it can be used to vary the
flame picture as required. To minimise any carbon deposition that may occur, it is recommended that the fire is
used on the COKE setting for the first and last periods (approximately 20 mins.) of each use.
SETTING PRESSURE
Remove the screw from the pressure test point, situated on the
main injector pipe by the pilot, and attach a U gauge. Light the fire
on the HIGH setting.
The setting pressure should be in accordance with the figures
stated on page 2 of these instructions. The fire is factory set to
achieve these pressures, and any significant variation could
indicate a supply problem.
If the pressure is too high, the gas supply meter may be set
incorrectly. This should be checked with the fire running and if
necessary reset by the gas supplier.
If the pressure is too low, then check the meter governor pressure with the appliance running. If this is incorrect
it will need to be reset by the gas supplier. If the setting pressure is too low, but the meter pressure is acceptable,
then a problem in the supply pipework is to be suspected. This will be dirt and debris, kinked or inadequate size
pipes, restriction in a fitting or solder flashing across a joint. (NOTE: you will not get an accurate reading of the
inlet pressure with a pressure gauge on the end of the supply pipe - this is the static pressure in the system. You
must use a T piece and measure the supply pressure with the fire on High - the dynamic pressure).
11
14.1
14.2
14.3
14.4