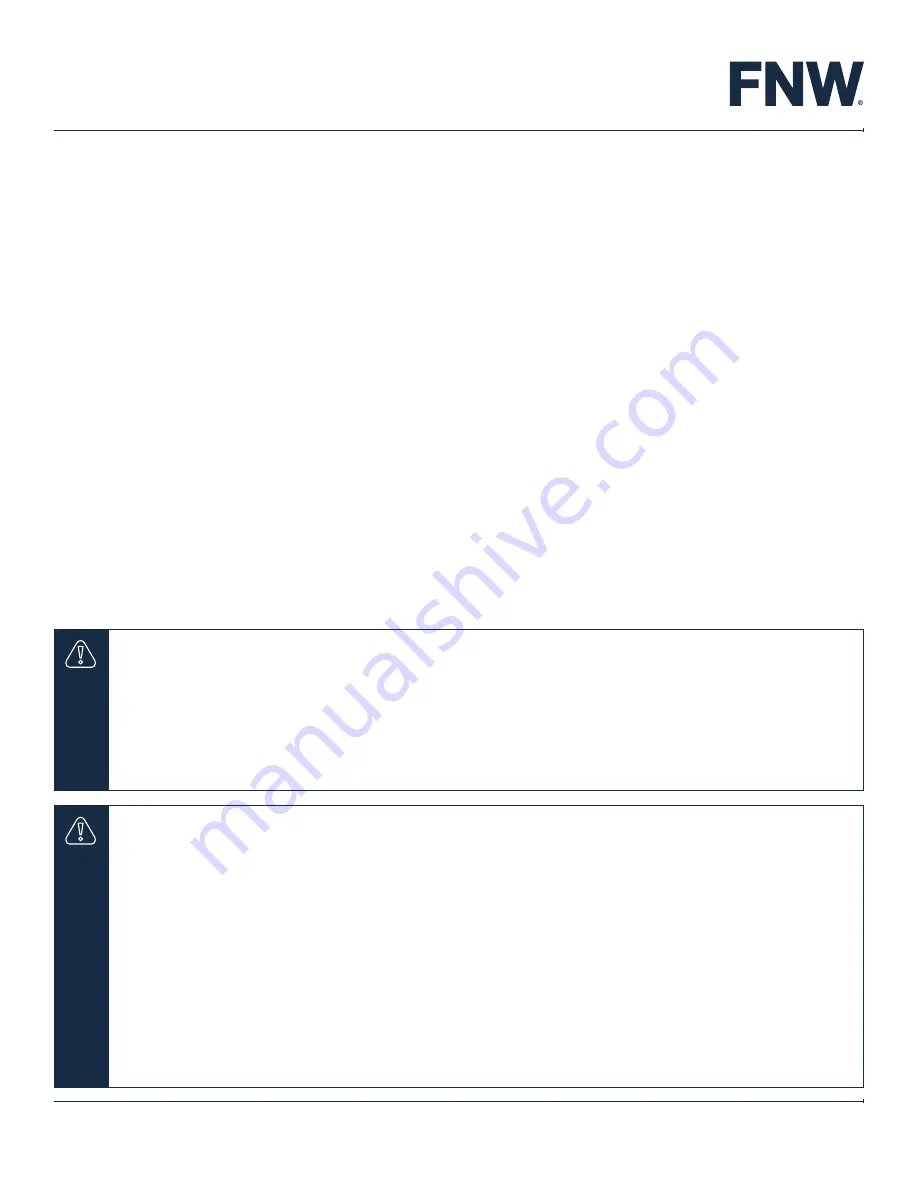
FNW.COM
©2021 Ferguson Enterprises, LLC 0721 2945816
We reserve the right to modify or improve the designs or
specifications of our products at any time without notice.
HIGH PERFORMANCE BUTTERFLY VALVE
FIGURE HPA
6
5. VALVE OPERATION
5.1 GENERAL
5.1.1 Operational life of the valve can be maximized
if the valve is used within the rated range, in
accordance with pressure, temperature and
corrosion data.
5.1.2 For arrangement of the internal construction, refer
to the Exploded View of the valve.
5.2 ACTUATION
General instructions given below, refer to separate
operator IOMs for further details.
5.2.1
Mechanism:
The stem of the valve is rotated
by using a wrench/handle/lever for small sized
valves and by a gear unit in case of larger valves.
Electric/hydraulic/pneumatic actuators can also be
used for actuation.
5.2.2
Wrench/handle/lever operated
valves shall be
opened or closed by turning the operator by a
quarter turn (90°).
•
Valve in open position – the operator is in
parallel (in-line) with the valve or pipeline.
•
Valve in closed position – the operator
is perpendicular (crossed) with the valve
or pipeline.
5.2.3
Gear units
are provided on valves for easier
operation. Usually, clockwise operation is for
closing and anti-clockwise is for opening of the
valve. The position of the valve can be noted by
the position indicator provided on top of the gear
unit. The number of turns will depend on the gear
unit used. Gear units are of the self-locking type
(i.e., the line fluid will not make the valve rotate)
and the gear units have factory-set mechanical
stopper screws for setting the exact opening and
closing positions.
Refer to section 8.4 for how to adjust the
mechanical stoppers, if required.
•
Worm gear operators are packed with grease.
Normally the grease is suitable for -20°C (-4°F) to
80°C (176°F). For other applications, consult the
nearest FNW or manufacturer representative.
CAUTION:
•
HPA series butterfly valves are quarter-turn valves (i.e., 90° rotation of the disc makes the valve either fully
opened or fully closed).
•
Butterfly valves employed for throttling duties shall be limited to a max pressure drop of 20% of the inlet.
Pressure at max open position.
•
Recommended controls angles are between 25°-70°. Preferred angles for control valve sizing is 60°-65° open.
•
Valve is to be operated for maximum 5 m/s velocity for liquids and 100 m/s for gaseous fluids.
CAUTION:
•
Keep hands, tools and other foreign objects out of the internals of valves. A remotely actuated valve might
close without warning causing physical damage and personal injury. Disconnect valve from supply sources
and make sure valve automation is in fail safe state before performing any maintenance work.
•
In cases when valves are supplied as bare stem as per customer requirements, please ensure that the
connecting devices for operator do not exert any axial or radial loads on the valve stem as it may lead
to bending of the stem and excessive loading on the ball. Ensure the end cover of actuator position is
interchanging to valve position when installing/mounting actuator to valve. Brackets, mounting hardware of
product, are designed to support the weight of the automation assembly. Do not apply additional weight as
this may result in leakage and performance failure of the valve assembly, causing possible seat damage and
increase operation torque.
•
Bare stem position indicator: When valve is closed, the position of the stem double-D or keyway is
perpendicular to pipeline; when valve is open, the position of the stem double-D or keyway is parallel
to pipeline.