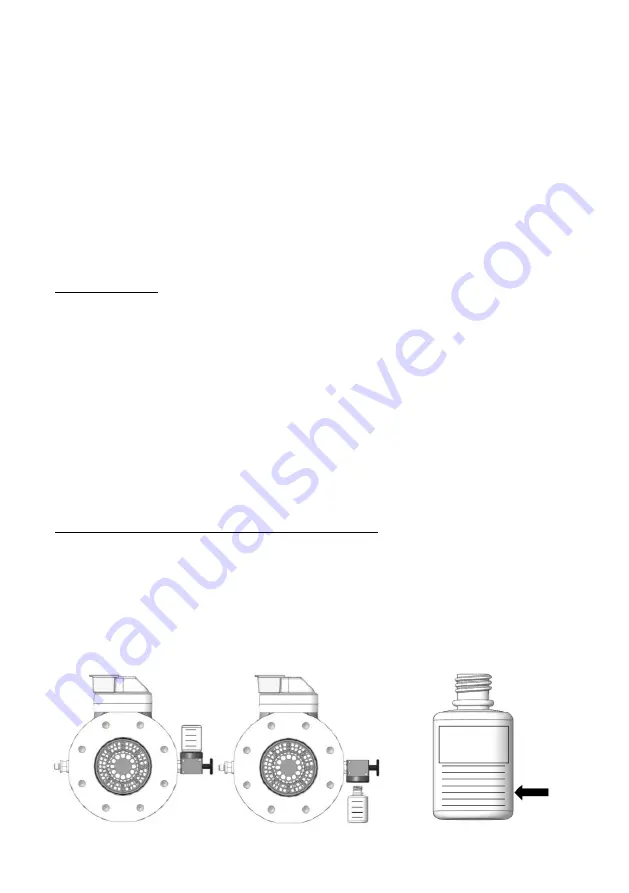
FMT- QA Installation and Operation Instructions - Page 2 of 16
7)
Level the meter within 5mm/m side-to-side and front-to-back and rotate the index the
right way.
8)
Tighten the flange bolts and nuts crosswise and regularly.
9)
Connect the pressure and temperature tapping connections and the electrical pulsers in
accordance with the connection diagram.
10)
Pressurize the meter with care to avoid overloading and shock loads.
11)
Conduct a tightness test.
12)
Slowly speed up the meter and check the meter to determine there is no vibration. It is
recommended to use a ¼Dn bypass to fill the system.
13)
If the meter is equipped with an oil pump the meter must be lubricated (see
Maintenance).
PRECAUTIONS:
1)
Never use the meter as a spool piece during welding.
2)
Never lubricate the meter if the temperature is below 0 ⁰C and at low flow rates.
3)
The meter should be transported and stored in a horizontal position.
4)
Use only devices with electrical characteristics as recommended (see connection
diagrams)
5)
Do not clean the plastic cover of the index with a dry cloth due to the risk of explosion
resulting from electrostatic discharge. Use cloth that has been adequately moistened
with water.
6)
The maximum tightening torque on the pressure and temperature tapping connections
is: 30 Nm. To tighten the swivel nuts; use 2 wrenches to avoid
over tighten
and damage
the meter body.
MAINTENANCE (for meters with oil pump only)
1)
Remove the oil container (by turning open). The oil container must be clean.
2)
Fill the oil container with the recommended oil up to the level as indicated.
3)
Turn the oil pump to vertical position and inject the amount of oil.
4)
After oiling, turn the pump upside down and seal the push button.
5)
The meters must be lubricated every 3-4 months. In case of high load or dirty gas
conditions, the interval can be shortened (2 months)
6)
Do not lubricate when the temperature is below 0 ⁰C or when the meter runs at a low
flow.