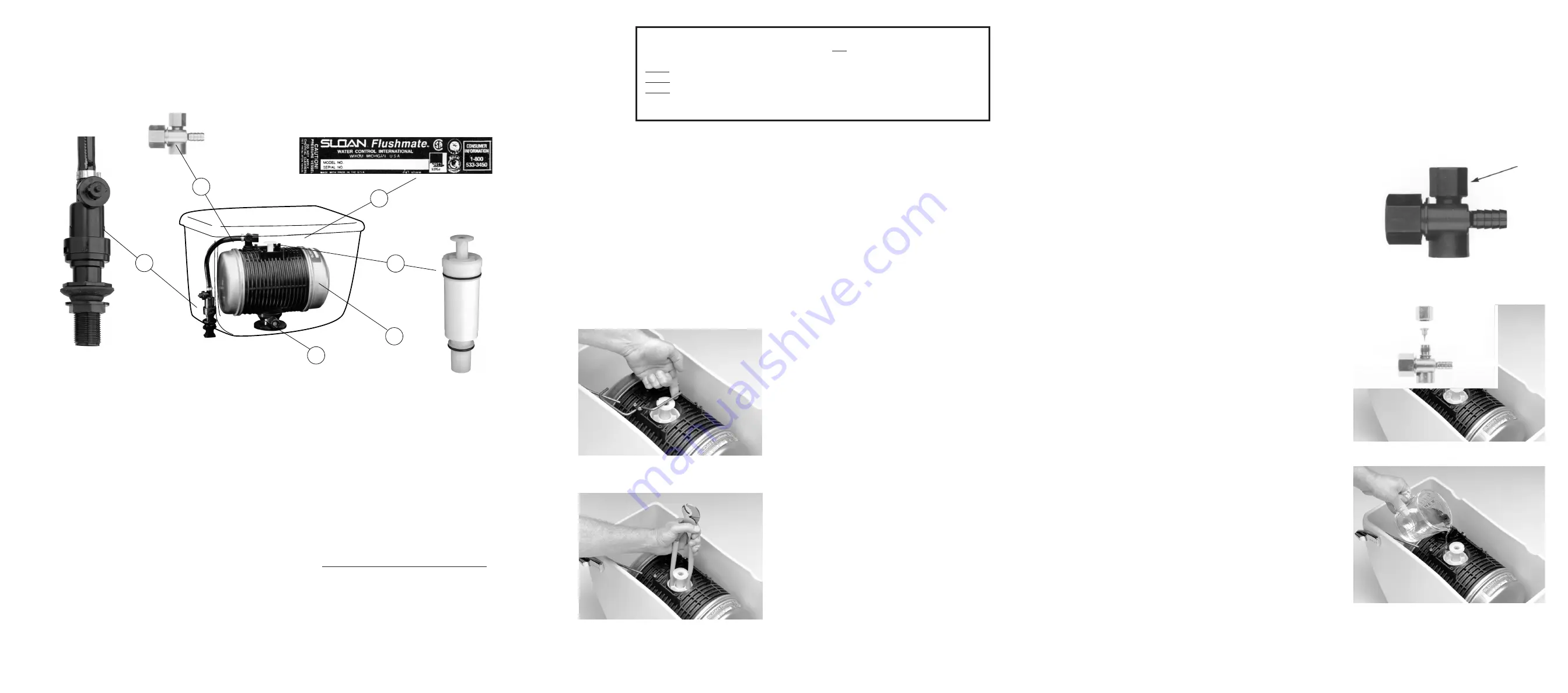
FLUSHMATE
®
501-A SERIES_______________________________________________________
INSTALLATION __________________________________________________________________
The Sloan FLUSHMATE
®
Flushometer-Tank System Fixture installs in the same manner as other water closets. Please follow the
instructions provided by the fixture manufacturer.
Using the gasket, washer and nuts provided with the fixture, assemble the tank to the bowl. Before connecting the supply to the tank,
be sure the supply line is flushed clean. Do this by running water from the supply stop into a bucket until water flows clear.
After connecting the supply line to the tank, turn on the water again and check for leaks. You may be required to make adjustments to
the actuator for either pushbutton type or trip lever type units. Please follow the instructions provided by the fixture manufacturer.
TROUBLESHOOTING _____________________________________________________________
CONDITION: Water runs on and will not shut off.
A newly installed toilet that does not shut off may be caused by inadequate or low pressure, and is usually the result of an insufficient
water supply flow rate into the FLUSHMATE Vessel. (NOTE: The recommended static pressure range by code is 20 p.s.i. to 125 p.s.i.).
If sufficient supply pressure has been verified and the toilet continues to run, the following steps may be required:
Step 1. Make sure supply stop is fully open.
Step 2. Check the Supply Shank Screen for any obstruction that would
restrict the supply.
Step 3: Check the Actuator adjustment (see Installation Procedure). The
linkage rod or push button should not interfere with the flush. On
Pushbutton type units, loosen the setscrew on the actuator (See
Number 4F on the component list) and rotate the Actuator up or
down until proper clearance is obtained (1/8”). For trip lever units,
gently lift the actuator rod and observe proper clearance is
maintained (approximately 1/8” gap between rod and actuator). See
Figure 1.
Step 4. Check the Flush Valve Cartridge Assembly for proper installation.
Proceed as follows:
a) Turn off the water supply and flush the toilet.
b) Remove the Flush Valve Cartridge Assembly using pliers’
handles as shown in Figure 2. NOTE: You may be required to
disconnect the Actuator Linkage Rod to remove the Flush Valve
Cartridge Assembly.
c) Inspect the “O” Rings on the Flush Valve Cartridge and the
seating area inside the tank for wear and/or improper seating.
Step 5. Reinstall the Flush Valve Cartridge Assembly.
First, insert the cartridge into vessel and, while gently
pushing down on the Cartridge, turn the Cartridge counter-
clockwise until you hear an audible click, indicating that the
threads are now aligned. Screw Cartridge clockwise into
place until two black threads of the Vessel are showing.
Next, turn on the water and continue to turn cartridge until
the water stops running. Do not over-tighten.
Step 6. If the Tank continues to run on, push down lightly on the Flush Valve Actuator. If the water stops running, it is an indication that
the Flush Valve Cartridge requires tightening (clockwise). If water still runs on while pushing down on the Actuator, the Flush Valve
Cartridge requires loosening (counter-clockwise).
NOTE: Adjust the Flush Valve Cartridge Assembly in quarter- to half-turn increments until the water stops running. Always turn the water
supply off for all adjustments. Flush Valve Cartridge turns the water off.
Step 7. If replacement of the Flush Valve Cartridge is necessary, follow the instructions in Step 5.
TROUBLESHOOTING _____________________________________________________________
CONDITION: Weak or Sluggish Flush.
Step 1. Check the water pressure (20psi - 125psi recommended). If OK,
then check the Flush System by removing the Tank Cover and tripping the
Actuator. While the unit is flushing, gently raise the Actuator. Water should
flow freely and wash away any debris in the supply line and Vessel.
Step 2. Check the Air Inducer for sufficient air draw. The Air Inducer is
designed to draw air during the refill cycle. To test the Air Inducer, place a
small amount of water (2 to 3 drops) in the orifice of the Air Inducer cap
and flush the toilet. If the Air Inducer is functioning properly the water will
be drawn in. If not, it will need to be cleaned and tested again.
TO CLEAN AIR INDUCER: (Figures 3 & 4)
a) Turn off the water supply and trip the Actuator.
b) Unscrew the Air Inducer Cap, clean thoroughly and remove
any obstructions. Reassemble. (Hand tighten ONLY)
c) Turn on water supply. Wait for the Vessel to refill (30 to 60
seconds). Repeat Step 2 above. If the Air Inducer does not
function properly, replace the Upper Supply Assembly.
Step 3. Check the Flush Valve Cartridge for leaks. Turn the water supply off
and drain the Vessel by tripping the Actuator and holding it down until
completely drained. Next, pour a cup of water onto the Cartridge Housing
area as shown in Figure 5. Turn on the water supply. If a leak is detected
(a steady flow of bubbles from the center of the Cartridge Area), the
Cartridge should be replaced.
Step 4. Check Lower Supply. Turn the water off and relieve the Vessel
pressure by flushing the toilet. Remove the supply line connection to the
shank. Remove any obstruction in the supply shank screen. If necessary,
you can use a small brush to gently brush the screen. Reattach the supply
line to the supply shank and observe connections to assure no leakage.
IMPORTANT: If you are still experiencing a weak or sluggish flush after this
point, it is recommended you replace the entire lower supply group.
Step 5. Check the following:
1. water line pressure (20 - 125psi)
2. obstruction in the bowl trapway
3. obstruction in the drain
4. proper drain ventilation
Consult a professional for their recommendations if any of these
conditions exist. If the drain and drain vent are clear, and the flush has not
been improved, replace the Lower Supply Assembly.
List of Components for 501-A Series*:
1. Lower Supply Group w/Hose BL100504
(A) Supply Shank with Screen
(B) Pressure Regulator w/Back Check
(C) Relief Valve
2. Upper Supply Group BU100505
(D) Air Inducer
(E) Vacuum Breaker
3. Name Plate w/Serial Number
4. Flush Valve Cartridge Assembly C-100500
(F) Actuator w/setscrew
5. Vessel
6. Discharge Extension w/Drain
FLUSHMATE
®
A Division of Sloan Valve Company
Manufactured under one or more of the following U.S. patents:
3,817,279 3,817,286; 3,817,489; 3,820,171,754; 4,233,698 and
5,802,628. Also covered by various foreign patents (country and
number available upon request) and other patents pending.
The Sloan FLUSHMATE
®
Flushometer - Tank System provides the highest
performance capability available today in the ULF (Ultra-Low Fixture) category. That
means it consumes less than 1.6 gallons/6 liters of water per flush. It achieves this
remarkable performance by using compressed air inside the tank, which creates a
turbo-charged flushing action for effective bowl cleaning. Compared to other types of
low consumption water closets, FLUSHMATE offers many distinct advantages.
Outstanding FLUSHMATE
®
Features:
• Positive Bowl Extraction (No Double Flushing)
• Stronger Flushing Action Improves Drainline Carry &
Leaves Bowl Cleaner
• Large Water Spot for Reduced Housekeeping
• Uses less than 1.6 gallons per flush
• Larger Trapway to Eliminate Stoppages
• No Water Leakage Between Flushes
• Non-Sweating Tank Enclosure
WARNING: When servicing or replacing components to the FLUSHMATE
®
Flushometer-Tank
System, make certain that the water supply is turned OFF and the toilet is then flushed to
relieve pressure in the vessel.
NEVER use lubricants on any of the components unless otherwise noted in this manual.
NEVER use corrosive chemicals or household cleaners on FLUSHMATE products.
NEVER use corrosive disinfectants, bowl cleaners or deodorant blocks on FLUSHMATE
®
Products or in the china tank.
Note: It is normal for less than one inch of water to remain in the bottom of the china tank.
FIGURE 1
(A)
(B)
(C)
(D)
(E)
(F)
1
2
3
4
5
6
FIGURE 2
FIGURE 3
FIGURE 4
FIGURE 5
Air Inducer Cap
* Components identified may appear different but are a direct replacement for this series.