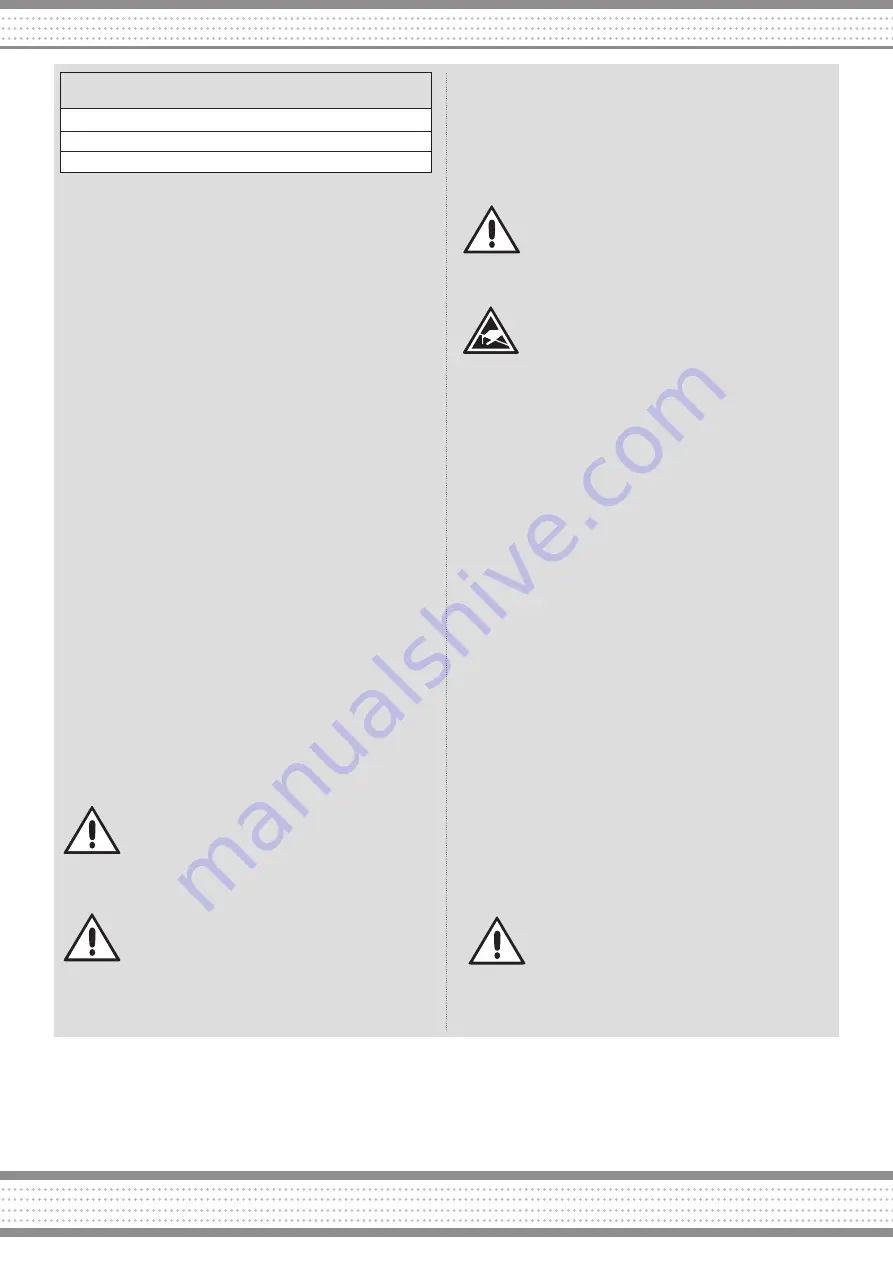
Warning:
The failure protection circuit towards earth is designed ONLY to
protect the inverter from failures earth, occurring on the motor
cable or on the motor itself. The failure protection is NOT designed
to protect people touching the motor or the power cables.
It is forbidden:
To connect PFC (Power factor correction) devices to the outlet
terminals between the inverter and the motor.
To connect capacitors between the outlet terminals or the outlet
terminals and the ground.
N
ote
• It is advisable to avoid the connection of the remote control
switches to the terminals between inverter and motor unless they
operate with stopped motor and inverter.
• When handling cables, please observe the following:
- are not damaged
- they may not be stressed,
- they may not come into contact with rotating components.
Notes concerning responsibility
The TMFR2-TSFR2 driver is a device designed to control the speed
of the pump-motor unit and it must be used with this purpose.
Under no circumstance the manufacturer will be held responsible
for any damage caused by misuse, wrong installation or
incompatible environmental conditions, nor for failures caused by
operation beyond the nominal values. The manufacturer declines
as well any responsibility arising from subsequent accidental
damages. There are no internal parts of the machine where it is
possible to intervene.
Tampering with the unit or using non-original spare parts avoid the
warranty and may cause damages and serious injuries.
Warning
Start–up/commissioning is absolutely prohibited until
it has been ensured that the machine in which the
components described here are to be installed, fulfills
the regulations/specifications of the Directive 2006/42/
CE. If this is not observed, this can result in injury.
Warning
The information and instructions in all of the
documentation supplied and any other instructions
must always be observed to eliminate hazardous
situations and damage.
• For special versions of the machines and equipment, the
information in the associated catalogs and quotations applies.
• Further, all of the relevant national, local land plant/system-
specific regulations and specifications must be taken into
account.
• All work should be undertaken with the system in a no–voltage
condition! If this is not observed, this can result in injury.
Warning
The capacitors mounted in the unit have dangerously
high voltage. For this reason, once the power cord
has been disconnected, it is necessary
to wait three
(3) minutes minimum before any service on the
device.
ESDS information and instructions
Electrostatic Discharge Sensitive Devices
C o m p o n e n t s , w h i c h c a n b e d e s t r o y e d
by electrostatic discharge are individual
components, integrated circuits, or boards, which when handled,
tested, or transported, could be destroyed by electrostatic fields
or electrostatic discharge. These components are referred to as
ESDS (ElectroStatic Discharge Sensitive Devices).
Handling ESDS modules:
• When handling devices which can be damaged by electrostatic
discharge, personnel, workstations and packaging must be well
grounded!
• Generally, electronic modules may not be touched unless work
has to be carried out on them.
• Personnel may only touch components if they are continuously
grounded through ESDS wristlets, they wear ESDS shoes,
ESDS shoe grounding strips in conjunction with an ESDS floor
surface. Boards/modules must only be placed on conductive
surfaces (table with ESDS surface, conductive ESDS foam,
ESDS packaging, ESDS transport container).
• Modules may not be brought close to data terminals, monitors or
television sets (minimum clearance to the screen > 10 cm).
• Do not bring ESDS–sensitive modules into contact with
chargeable and highly–insulating materials, such as plastic
sheets, insulating table tops or clothing made of synthetic
materials.
• Measuring work may only be carried out on the components if
the measuring unit is grounded (e.g. via a protective conductor)
or when floating measuring equipment is used, the probe is
briefly discharged before making measurements (e.g. a bare–
metal control housing is touched).
Warning
Magnetic coupling does not guarantee a defined
release pressure value.
If the hydraulic circuit needs to be protected
from any water hammering generated on the
pump, it is essential to use a pump equipped
with a bypass or a safety valve to be installed
after the pump.
REMOTE CONTROL SWITCH
SPARK QUENCHING UNIT
OR SOLENOID VALVE
CHARACTERISTICS
220Vac, 240Vac >30A
0.5 μF + 100 Ω 0.5W 250V
220Vac, 240Vac <30A
0.1 μF + 100 Ω 0.5W 250V
24Vcc Diode
Summary of Contents for TMFE2
Page 10: ......