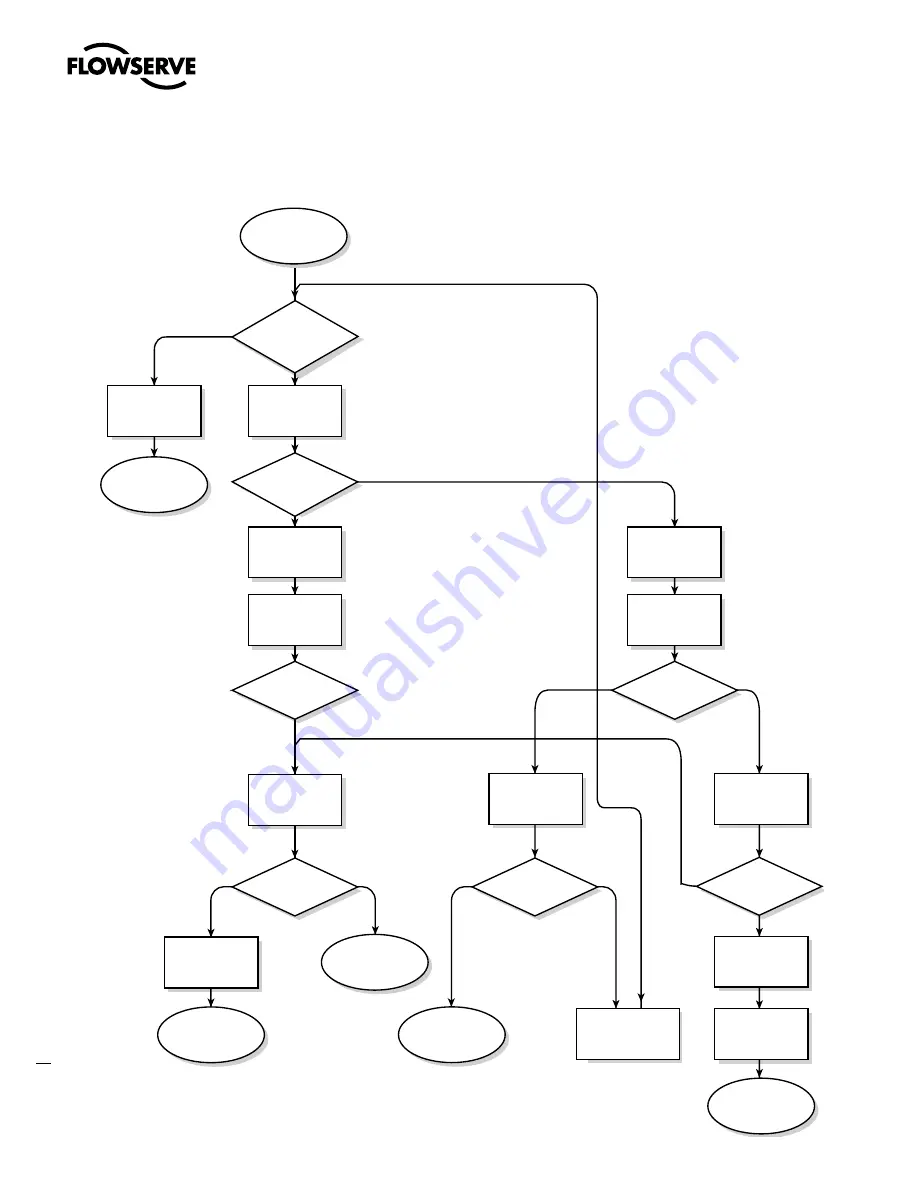
StarPac Intelligent Control System FCD VLENIM0066-02 02/10
56
®
24 StarPac 3 Pressure Sensor Troubleshooting
Figure 28: StarPac 3 Pressure Sensor Troubleshooting Chart
Pressure reading
is incorrect
Is pressure
slightly off or
saturated?
Saturated
Is reading
saturated
low or high?
Low
Slightly
off
Recalibrate
sensor
Make sure
sensor is
plugged in
Yes
Is sensor
working?
No
Swap sensors
Yes
No
Same problem
appear?
Problem is in
wiring or board
Contact Factory
Replace
sensor
Replace
sensor
Check wire harness
for shorts or
contamination
Replace bad
O-rings
Tighten all
fittings
Check fittings
and O-rings
Yes
Is reading
correct?
No
Yes
No
Does reading
return to full
scale?
Reconnect
sensor
Yes
No
Does reading
go to 0?
Disconnect
sensor
High
Clean contacts