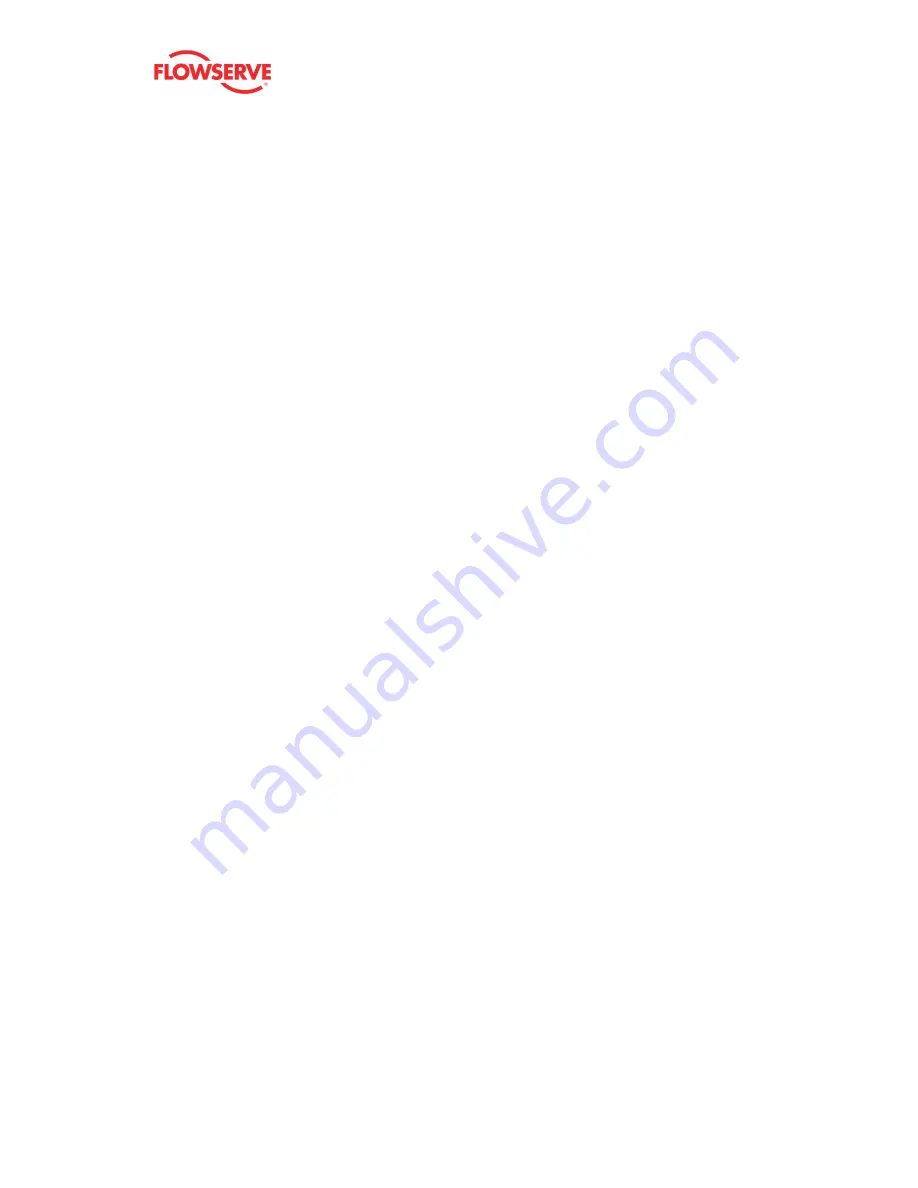
User Instructions - Logix® 520MD+ Series Digital Positioner
FCD LGENIM0105-00
© Flowserve Corporation
44
Field Trial Version – Printed October 28, 2011
Possible Solutions: Signatures and tests can be defined,
initiated, and cancelled through the Off-Line Diagnostics
pages of the DTM.
GRGY
●
●
●
●
STROKE CALIBRATION IN PROGRESS
SETTING INNER LOOP OFFSET
PRESSURE CALIBRATION IN PROGRESS
FRICTION CALIBRATION IN PROGRESS
ANALOG OUTPUT CALIBRATION IN PROGRESS
COMMAND INPUT CALIBRATION IN PROGRESS
Description: A calibration sequence is in progress. The inner
loop offset is an important step of the stroke calibration.
Possible Solutions: The calibration can be canceled from the
corresponding calibration page of the DTM, from the
handheld, or by briefly pressing the BACK button.
GRGR
●
●
●
●
DI COMMAND OVERRIDE
Description: The Multi-Function Card has been configured as
a Discrete Input (DI) and to override the input command,
positioning the valve at a preconfigured set point. The DI
signal is active and the positioner is attempting to control the
valve at the set point.
Possible Solutions: Configure the DI function and set point
using the menu, a handheld or the Multi-Function Card
Configuration page of the DTM.
GRRY
●
●●
●
JOG COMMAND MODE
Description: The positioner has been placed in a local
override mode where the valve can only be stroked using the
UP and DOWN buttons. The positioner will not respond to
analog or digital input commands from HART.
Possible Solutions: Control the valve using the UP and
DOWN buttons. This mode may be cancelled by briefly
pushing the QUICK-CAL/ACCEPT button.
GRRR
●
●●●
JOG CALIBRATION SET 100% POSITION
Description: During a jog calibration, the unit is waiting for the
user to manually adjust the valve position to the desired
100% open position.
Possible Solutions: Use the Up and Down buttons on the
positioner to adjust the valve to the desired fully open
position. The QUICK-CAL/ACCEPT button to accept.
YGGG
●
●●●
POSITION HIGH LIMIT ALERT
POSITION LOW LIMIT ALERT
Description: The position has reached or is exceeding a user
defined position limit. This is similar to a limit switch
indicator.
Possible Solutions: Set the limit to a higher (or lower) value if
more travel is needed, or adjust the command signal back in
the specified range.
YGGY
●
●●
●
ACTUATOR CYCLES WARNING
ACTUATOR TRAVEL WARNING
BELLOWS CYCLES WARNING
BELLOWS TRAVEL WARNING
PILOT RELAY CYCLES WARNING
PILOT RELAY TRAVEL WARNING
VALVE CYCLES WARNING
VALVE TRAVEL WARNING
Description: The cycle or travel limit of the valve, actuator,
bellows or pilot relay has been exceeded. Each cycle
represents two reversals of the direction of valve movement.
The cycle counting criterion and count limit (for the valve,
actuator and bellows) are set by the user to track the usage
of the valve assembly.
Possible
Solutions:
Follow
routine
procedures
for
maintenance when the limit is reached. For example valve
inspection may include checking the packing tightness, and
checking linkages for wear, misalignment, and tightness.
Bellows inspection may include checking bellows for cracking
or leaking. Actuator inspection may include checking the
actuator seals and lubrication. Relay inspection may include
checking for high air consumption and signs of wear on the
spool. After maintenance, reset the travel accumulator.
YGYY
●
●
●●
POSITION AMPLITUDE WARNING
POSITION FREQUENCY WARNING
Description: The amplitude or frequency of the position signal
is above the warning limit. The positioner is controlling the
position of the valve with large or rapid corrections.
Possible Solutions: Verify the limits are set at an appropriate
level. Adjust the selectable Gain switch to a lower setting or
use the Hi Friction setting. Perform a QUICK-CAL which
sets the gains based on valve response. Check for high
friction. If the problem persists replace the relay.
YGYR
●
●
●
●
COMMAND AMPLITUDE WARNING
COMMAND FREQUENCY WARNING
Description: The amplitude or frequency of the command
signal is above the warning limit. This could mean the
control loop has larger swings or is oscillating faster than
desirable.
Possible Solutions: Verify the limits are set at an appropriate
level. Review the control loop parameters and equipment.
Adjust as necessary.
YGRY
●
●
●
●
CONTINUOUS STROKE TEST FAILED WARNING
Description: During the continuous stroke test, the valve did
not move after 5 consecutive attempts. This could mean the
valve has increased friction, a change in process load or
inadequate supply pressure.
Possible Solutions: Check friction, supply pressure and other
alarms or warnings that would indicate difficulty in moving the
valve. Check packing, and air supply. The warning will
clear when the CST function is turned off or when a
successful attempt to move the valve occurs.
YGRR
●
●
●●
PARTIAL STROKE TEST FAILED WARNING
Description: Measured times or forces during the last partial
stroke test did not pass the criteria set by the user. This may
be an indication of corrosion build-up on the valve stem or in
the actuator, low or restricted supply pressure, or a sticking
positioner relay.
Summary of Contents for Logix 520MD+
Page 53: ......