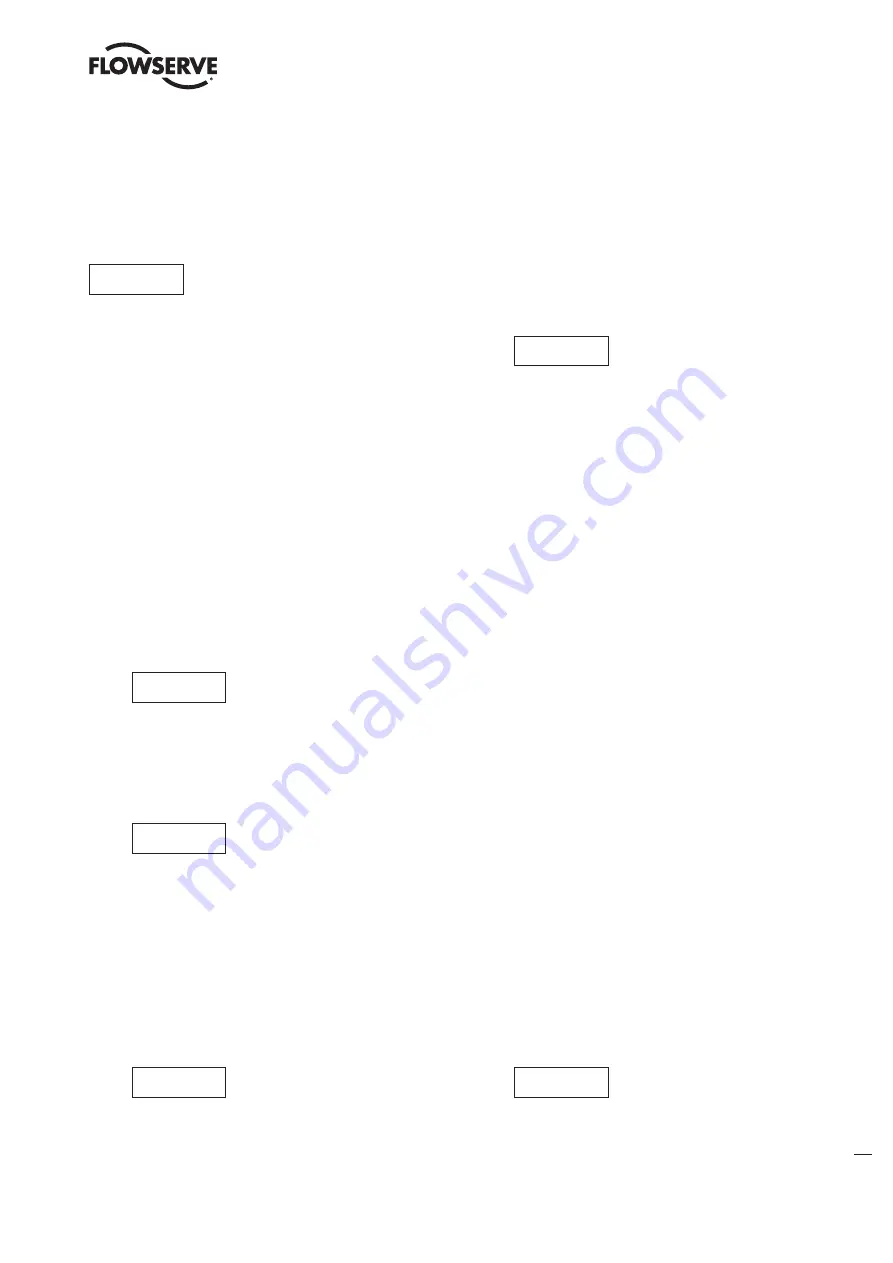
FlowAct Diaphragm Linear Actuator FCD VLENIMFACTA4 10/16
71
flowserve.com
Reassembly instruction of the actuator subas-
sembly
NOTICE
Always replace parts showing wear with
new parts.
22. Lubricate the new O-ring (275) and new scraper ring
(273) with an appropriate lubricant and install into the
guide bushing (253).
23. Lubricate the new O-ring (275) with an appropriate lu-
bricant and install into the guide bushing (373).
24. Fix the stem (211) into the stem clamping tool.
25. Lubricate the new O-ring (272) with an appropriate
lubricant.
26. Lower the distance bushing (374), spacer bushing
(228), disk (220), diaphragm plate (227),
diaphragm (225), O-ring (272), thrust
washer (255) and lock washer (349)
onto the stem (211).
NOTICE
Arrange the distance bushing like an
correctly wearing hat. Its function is
that of an internal stroke stop.
27. Lubricate the thread of the stem (211) with an appro-
priate lubricant and install and finger tighten the stem
extension (380).
NOTICE
The diaphragm plate should be posi-
tioned to the diaphragm with the aid
of the positioning template. Mark the position.
28. Turn clockwise the stem extension (380) using a suit-
able torque wrench, see section 15 torque requirements.
29. Install the distance plate (231) and positioning the
spring adjusting plate (326) such that the imprint and
air connection opposites.
30. Install and align the actuator springs (229).
NOTICE
The surface, respectively the edges
of the spring ends should be aligned
to the actuators center. If these will ignored the spring
may touch the actuators casing and rub in rare cases.
31. Loosen and remove the diaphragm-stem unit (211-
380) out of the stem clamping tool. Lubricate the ac-
tuator stem with an appropriate lubricant.
32. Carefully lower the diaphragm-stem unit (211- 380)
into the diaphragm casing (202 - 334).
NOTICE
Position the diaphragm-stem unit
such that the air connection and the
Mark align.
33. Install the diaphragm casing (202 - 373), positioning
the casing such that the air connections opposites.
34. Lubricate the threats of the long hexagon bolts (336)
with an appropriate lubricant and load the springs uni-
formly in a clockwise sequence by tightening the long
hexagon bolts (336), plain washers (337) and hexagon
nuts (351). Alternative method see
NOTICE
step 12.
35. Install the short hexagon bolts (335), plain washers (337)
and hexagon nuts (351).
36. Tighten the nuts (351) using a crosswise pattern in
four steps, see section 15 torque requirements.
37. Install the protection sleeve (339).
38. Assemble the coupling parts (see page 54).
39. Lubricate the new O-ring (276) with an appropriate
lubricant and install it onto the guide bushing (373).
40. Lubricate the threats of the hexagon bolts (334) and
the new O-rings (279) with an appropriate lubricant.
41. Install the diaphragm casing (202) onto the guide
bushing (373) and tighten the bolts (334) using a
crosswise pattern in two steps, see section 15 torque
requirements.
42. Install the distance plate (231) and positioning the
spring adjusting plate (326) such that the imprint and
air connection opposites.
43. Install and align the actuator springs (229).
NOTICE
The surface, respectively the edges
of the spring ends should be aligned
to the actuators center. If these will ignored the spring
may touch the actuators casing and rub in rare cases.