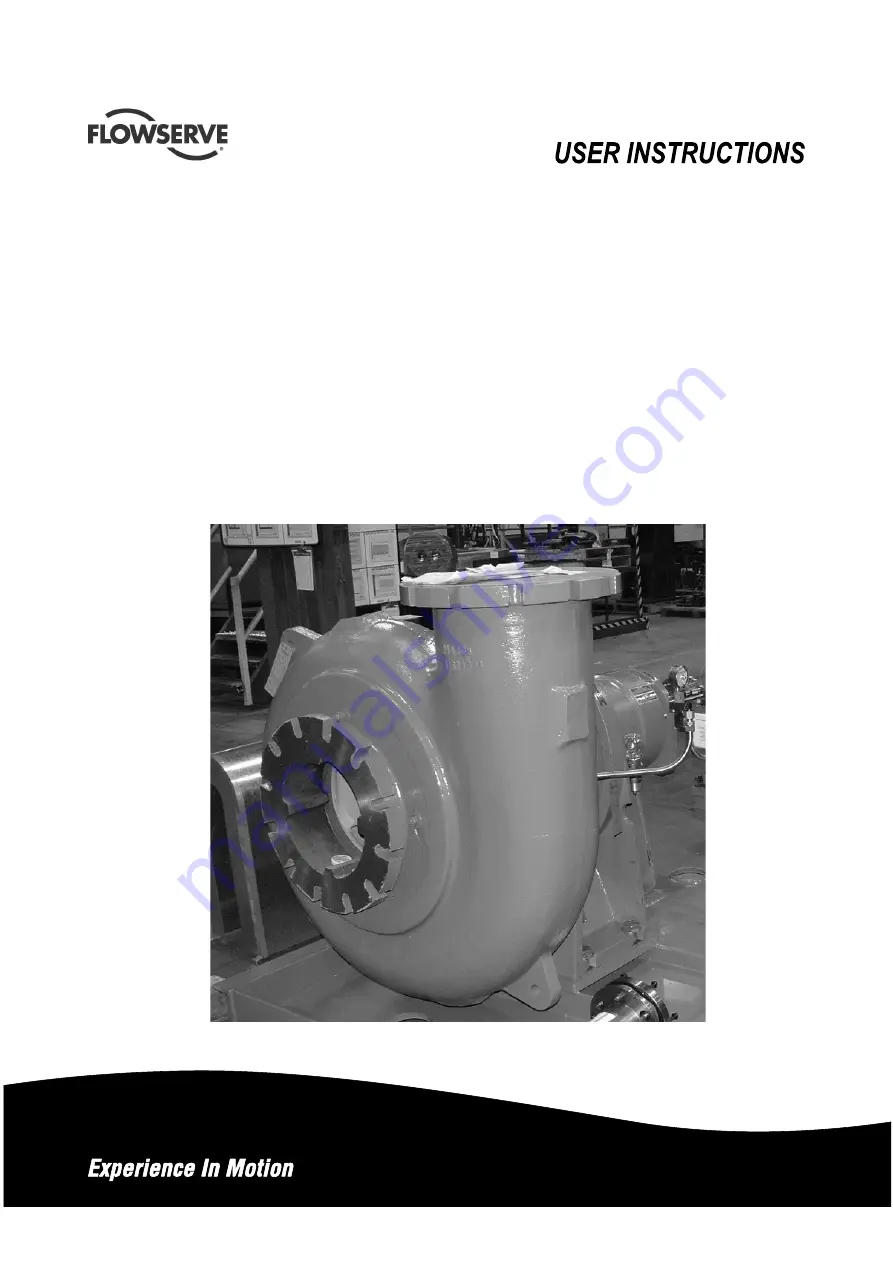
M Slurry Pump
Standard and Severe Duty (includes MX & MS options)
PCN=71569241 – 02/08 (E)
Installation
Operation
Maintenance
Компания ПромХимТех
-
официальный дистрибьютор
насосов
Flowserve
Тел
. 8 800 250-01-54
e-mail: [email protected]