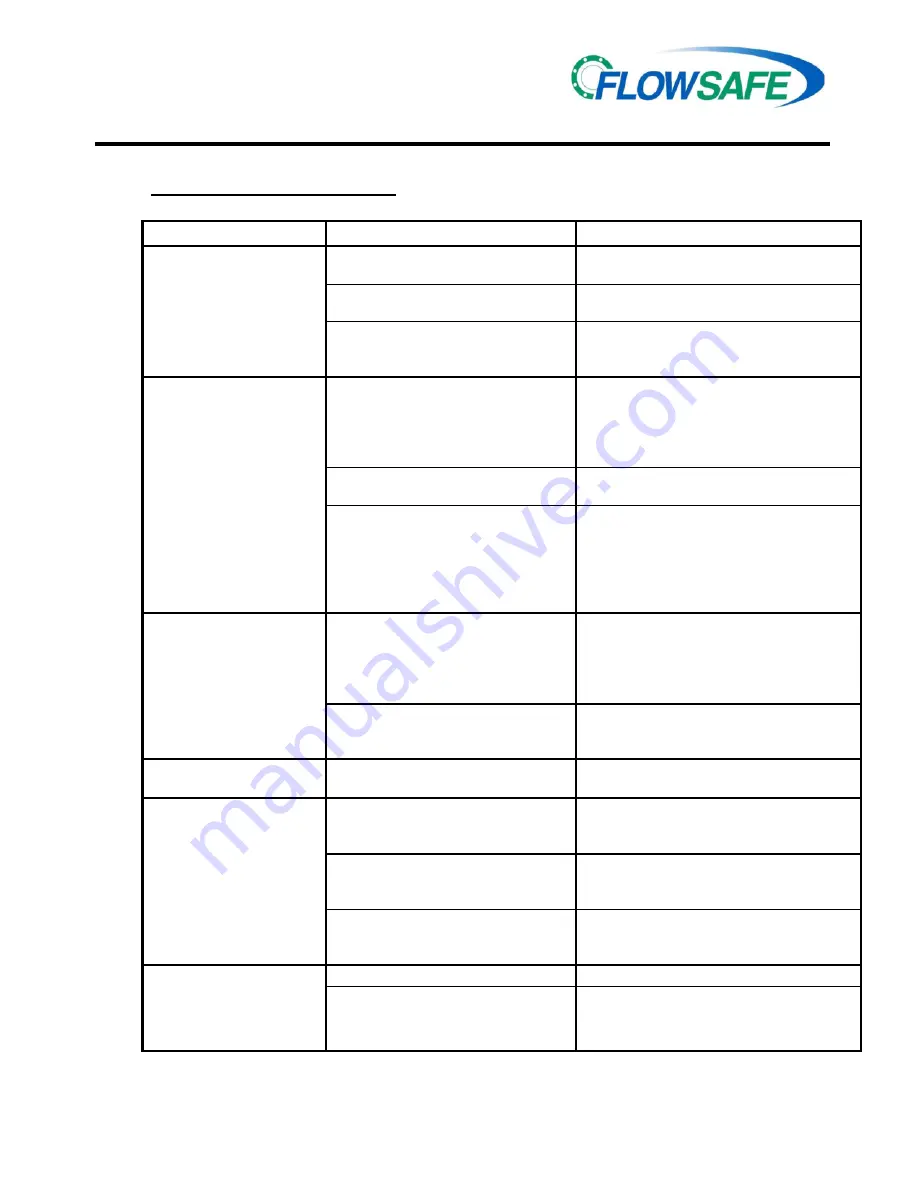
INSTALLATION, OPERATION, &
MAINTENANCE MANUAL
TITLE:
F84L Series Liquid Relief Valve
Rev. J
Page 12 of 18
6.0
TROUBLESHOOTING GUIDE:
Symptom
Possible Cause
Remedy
The valve leaks around
the bushing.
Inadequate bushing torque.
Tighten until the bushing bottoms firmly
on the body.
Sealing surface on body or
bushing is damaged.
Inspect and polish sealing surfaces.
Bushing seal is damaged or
contaminated.
Remove bushing seal. If damaged,
replace with new seal. If contaminated,
clean and replace.
The valve leaks through
the outlet.
Seat or nozzle seating surface is
damaged or contaminated.
Disassemble the valve, remove the
spindle, and examine the seat and
seating surface under magnification. If
damaged, replace with new seat; if
contaminated, clean and reinstall.
Uneven torque on body-to-bonnet
bolts.
Torque bolts evenly (see Section 3.2 for
values)
Operating pressure is too close to
set pressure.
Operating pressure should be less than
90% of set pressure for F84L’s at most
pressures, but less than 80-85% of
set pressures ≤ 500 psig for the F84L-2
(HP), 300 psig for the F84L-2 (LP), or
100 psig for bolted-bonnet sizes.
The valve leaks through
the atmospheric vent
hole in bonnet.
Worn / damaged spindle or seals.
Disassemble valve, remove spindle
assembly, and inspect spindle and two
seals on upper neck. Look for nicks,
tears, or flat spots. Replace as
necessary.
Pipe plugs are not installed
properly.
Tighten or reinstall plug(s).
The valve does not
close.
The spindle is stuck.
Disassemble and check for binding.
Deburr or replace parts.
The valve opens below
the designated set point.
The spring preload is low due to
misadjustment, vibration, or other.
Adjust pressure adjusting screw in
(clockwise). Ensure PA screw lock nut
and cap are tight.
The seat leaks due to possible
damage, allowing early simmer
and pop.
Disassemble and inspect seat; replace
if damaged.
Spring washer is not in proper
contact with spindle.
Ensure that dimpled area of spring
washer is aligned with top of spindle.
The valve opens above
the designated set point.
The spring preload is high.
Adjust PA screw out (counterclockwise).
The spindle is stuck or sticking.
Disassemble and check for binding.
Deburr or replace parts.