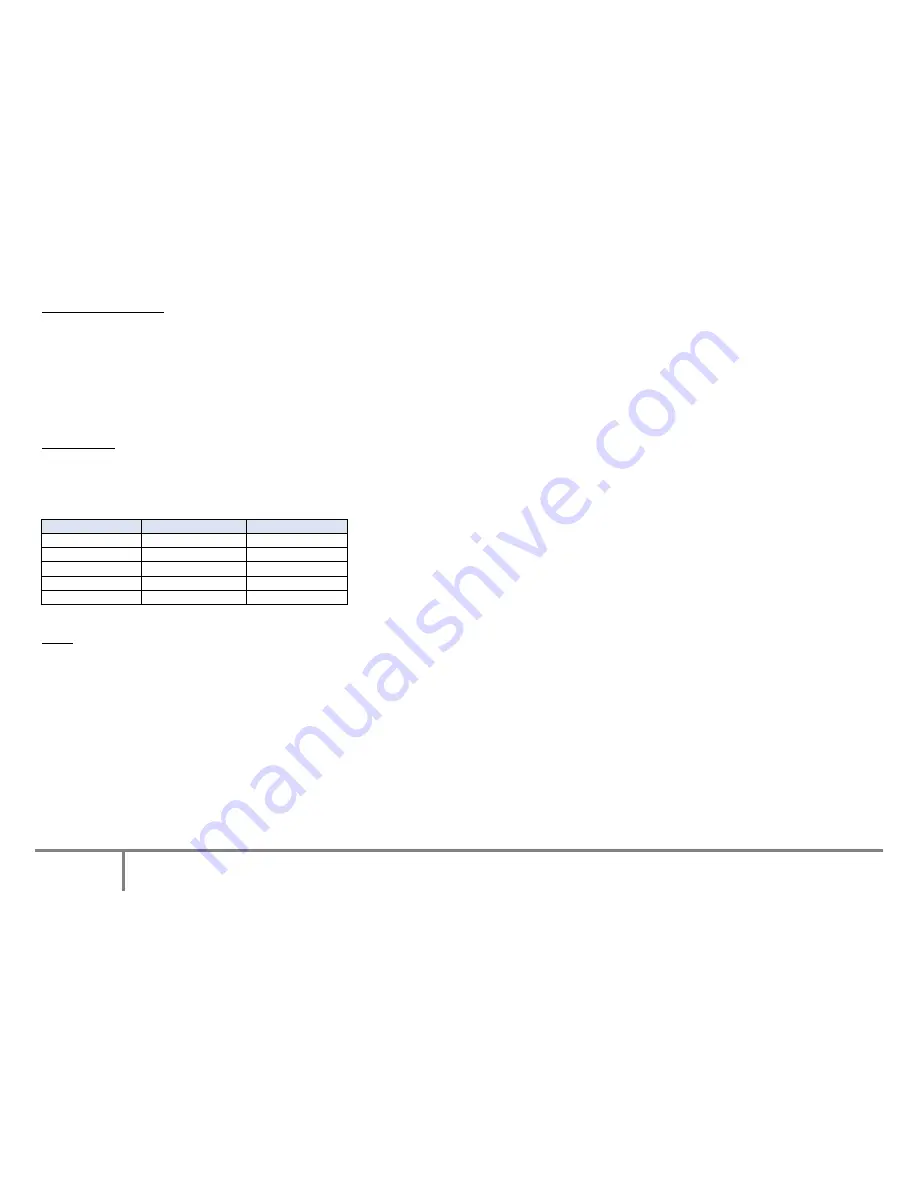
10
User Manual 160 DualArc ENG
FLOW160DA025
ARC WELDING BASICS
Arc welding is a process in which metals are joined together using heat developed by a welder. Current passes through the metals via the work clamp and the electrode (and the electrode holder), thus forming intense
heat which results in a weld. The incandescent space between the weld area and the burning electrode is commonly referred to as the arc.
This unit is an AC (alternating current) welder, which means that current travels in both directions of the welding circuit, in quick alternations (50 or 60 times per second, for 50Hz and 60Hz frequencies).
Electrode selection:
The diameter (thickness) of the welding electrode should be approximately the same as the thickness of the metal being welded. However, specific electrodes have different properties suited to the welding job to be
done, such as type of metal, weld position, type of flux (coating) of the electrode etc. The thicker the metal, and the electrode, the higher the amperage setting needed to weld (this can be seen on the chart on the top
portion of the welding machine). Read the instructions of the electrode you are using, as they contain more specific guidelines. The chart below provides a benchmark for welding carbon steel with an E6013 electrode.
Electrode diameter
Metal thickness
Amperage needed
1/16 inches ; 1.6mm
1/16 inches ; 1.6mm
40-55
1/16 inches ; 1.6mm
5/64 inches ; 2.0mm
50-70
1/16 inches ; 1.6mm
3/32 inches ; 2.4mm
75-95
1/8 inches ; 3.2mm
1/8 inches ; 3.2mm
100-140
1/8 inches ; 3.2mm
5/32 inches ; 4.0mm
140-180
Current:
Current represents the actual flow of electricity and is regulated by a rotating knob on the welder. The current to be used depends on the size (diameter) and type of electrode used, position of the weld, and the
thickness of the weld piece. Consult specifications listed on the electrode package or generalized chart in the case of the unit. Excessive current burns through light metals, and the weld bead is flat and porous or the
bead undercuts the work piece. The bead appears high and irregular if the current is too low.