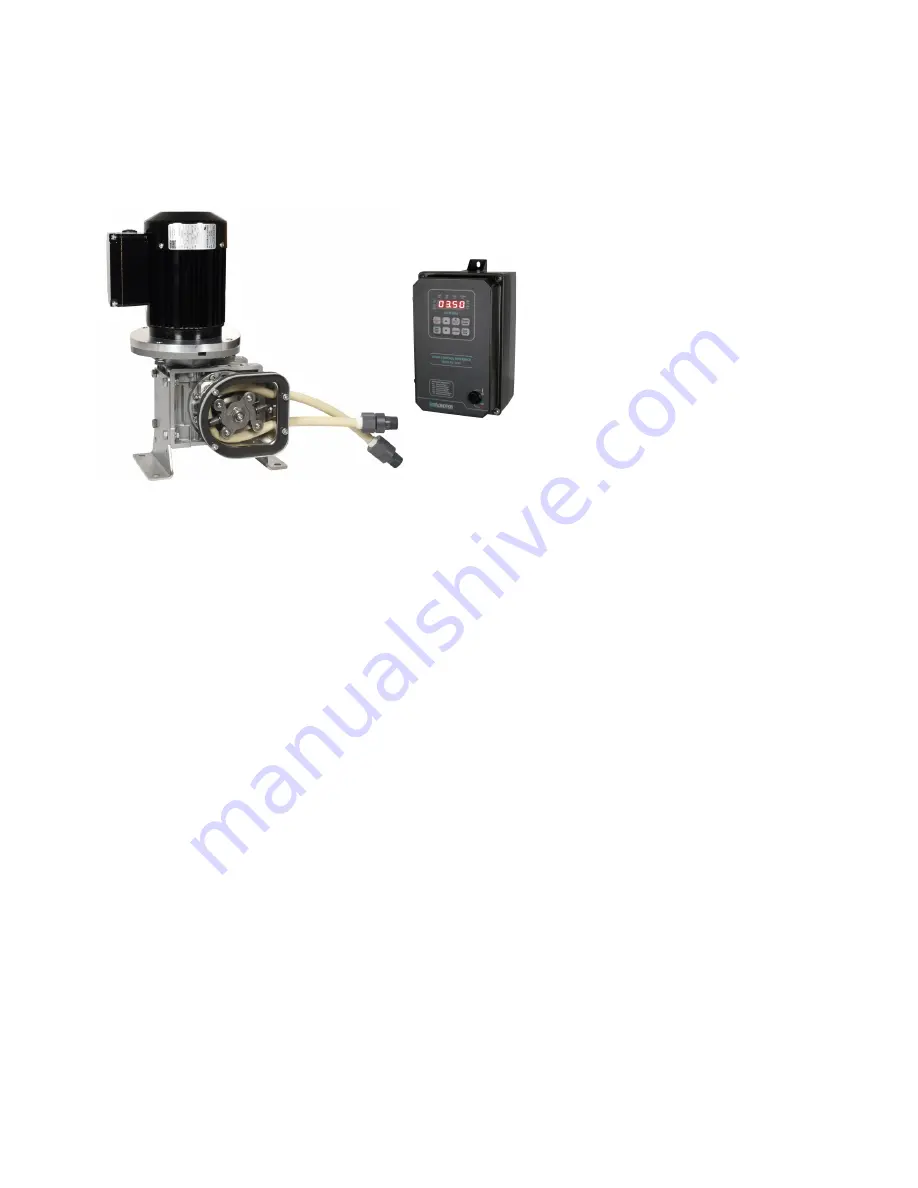
1.0 - System Overview
The V21 Chemical Feed Pump consists of a controller, motor, gearbox and peristaltic pump.
1.1 Safety
In the interests of safety, this pump and the tubing selected should only be used by competent, suitably trained
personnel after they have read and understood this manual, and considered any hazard involved. Any person
who is involved in the installation or maintenance of this equipment should be fully competent to carry out the
work.
Maintenance and repair should be performed by qualified personnel only. Make sure that no
voltage is applied while work is being carried out on the pump or motor. The motor must be
secured against accidental start up.
1.2 Receiving
Inspect all cartons for damage, which may have occurred during shipping. Carefully unpack equipment and
inspect thoroughly for damage or shortage. Report any damage to carrier and/or shortages to supplier. All
major components and connections should be examined for damage and tightness, with special attention given
to PC boards, plugs, knobs and switches.
1.3 Customer Modification
Flomotion Systems, Inc., its sales representatives and distributors, welcome the opportunity to assist our
customers in applying our products. Many customizing options are available to aid in this function. Flomotion
Systems, Inc. cannot assume responsibility for any modifications not authorized by its engineering department.
1.4 Information for Returning Pumps
Equipment that has been contaminated with, or exposed to, body fluids, toxic chemicals or any other
substance hazardous to health must be decontaminated before it is returned to Flomotion Systems or its
distributor.
Please contact Flomotion Systems for a Return Authorization number and instructions for returning
the pump.
pg. 3