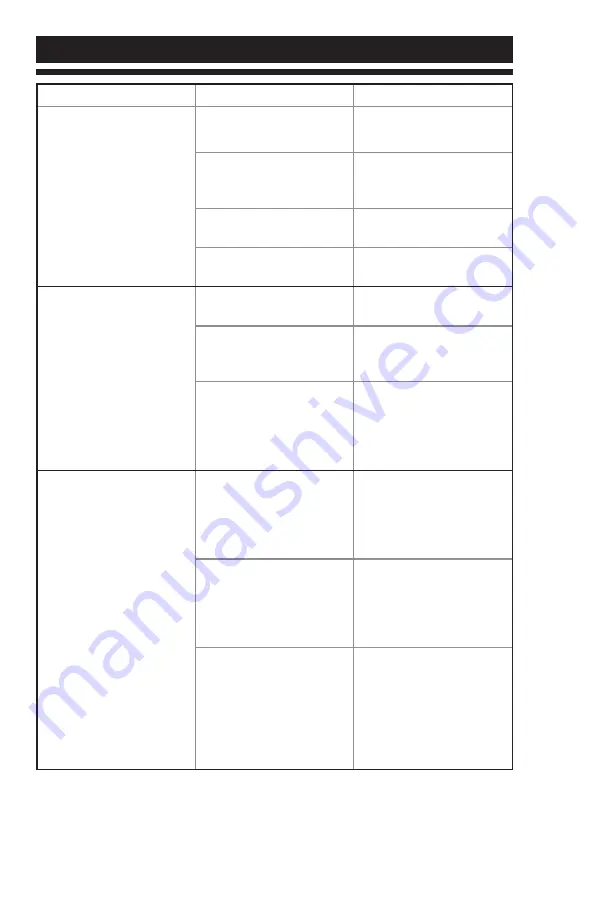
7
TROUBLESHOOTING
Symptom
Probable Cause
Corrective Action
A
�
Meter counter does
not operate
�
(Normal
fuel flow)
Broken counter
assembly
�
Replace counter
�
Counter alignment
Look for loose or
missing fasteners, bent
or misaligned parts
�
Foreign material in
counter assembly
�
Remove and clean
counter assembly
�
Missing or worn bevel
gear
�
Replace bevel gear
�
B
�
Meter counter does
not operate
�
(Little or no fuel flow)
Clogged strainer in
meter inlet
�
Clean or replace
strainer
Jammed rotors from
foreign material in rotor
assembly
�
Remove and clean rotor
assembly
�
Other system
components
malfunctioning
�
Check all system
components tank to
nozzle for clogs and/or
malfunctions
�
Repair as
necessary
�
C
�
Fuel leakage
�
Leakage between
coverplate and housing
�
Remove coverplate and
inspect for damaged,
missing or incorrectly
seated seal
�
Replace
as required
�
Leakage at fittings
Remove fittings and
inspect for damaged,
missing or incorrectly
seated seals
�
Replace
as required
�
Leakage at threads
�
Remove meter and
reseal all threaded
connections with thread
tape or pipe thread
sealing compound
approved for use with
flammable liquids�