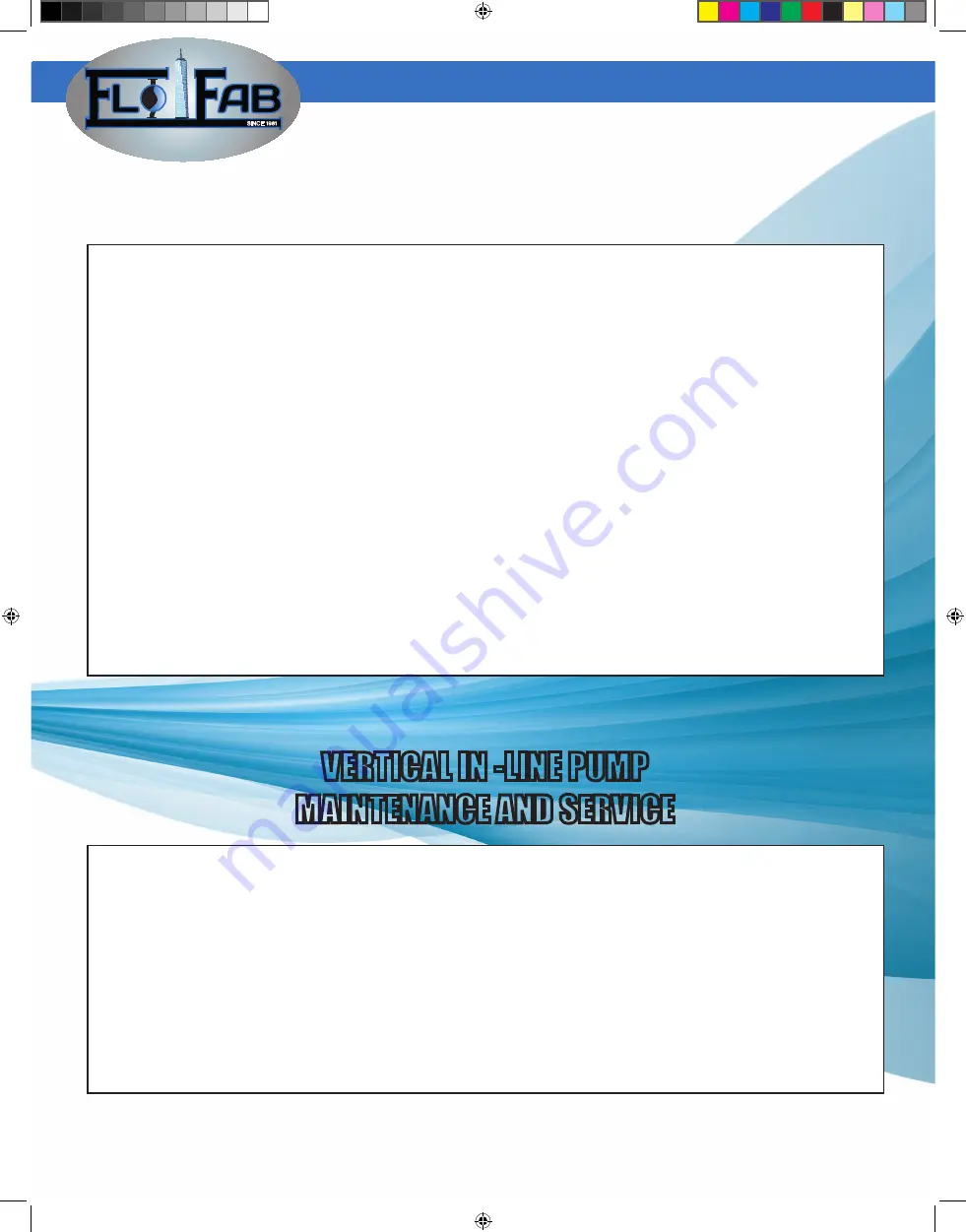
SINCE 1981
8
1 . Protect pump with a suitable strainer
2.
Never pump a liquid for which the pump was not designed (check with your FLO FAS
representative).
3.
Keep the right amount of the right lubricant in bearings at all times, Following lubrica-
tion instructions.
4.
Check periodically pump and motor alignment.
5.
Any down sloping towards the pump in suction piping should be corrected.
6.
See that piping puts no strain on pump casing.
7.
Never allow pump to run dry.
8.
Examine wearing rings at regular intervals.
9.
If shaft sleeves are badly scored, replace them immediately.
10. If the liquid being pumped contains grit, o separate source of sealing liquid should be
used.
11. A routine maintenance schedule should be set-up to ensure an optimum inspection and
service operation in order to get the best service out of your pumping equipment.
PREVENTIVE MAINTENANCE
VERTICAL IN -LINE PUMP
MAINTENANCE AND SERVICE
Vertical pumps are built to operate without periodic maintenance with the exception of lubrica
-
tion motor bearings with silicone grease such as Dow-Corning 44, Keystone #78 or Supermill
ASU 06752 grease every 3 months. Good operational life will depend upon proper pump sele
-
dion, installation and continuous water lubrication of the mechanical seals. The air vent plug
must always be loosened to thoroughly vent casing before start-up and to insure water lubrica-
tion of mechanical seals.
Impurities in the system will shorten the operational life of mechanical seals due to the general-
ly abrasive charaderistics of these impurities. Most common is black iron oxide which is highly
magnetic and has a tendency to fonn hard coating on all surfaces in contact with water. Water
treatment is also an important factor in seal life. It is recommended that the chromate content
in wafer be limited to 250 ppm.
I.O.M - 880RI SERIES
IOM 880RI.indd 9
2017-11-14 13:04:01
Summary of Contents for 880RI Series
Page 14: ......
Page 15: ......
Page 16: ......
Page 17: ......
Page 18: ......
Page 19: ......
Page 20: ......
Page 21: ......
Page 22: ......
Page 23: ......
Page 24: ......
Page 25: ......
Page 26: ......
Page 27: ......
Page 28: ......
Page 29: ......
Page 30: ......
Page 31: ......
Page 32: ......
Page 33: ......
Page 34: ......
Page 35: ......
Page 36: ......
Page 37: ......
Page 38: ......
Page 39: ......
Page 40: ......