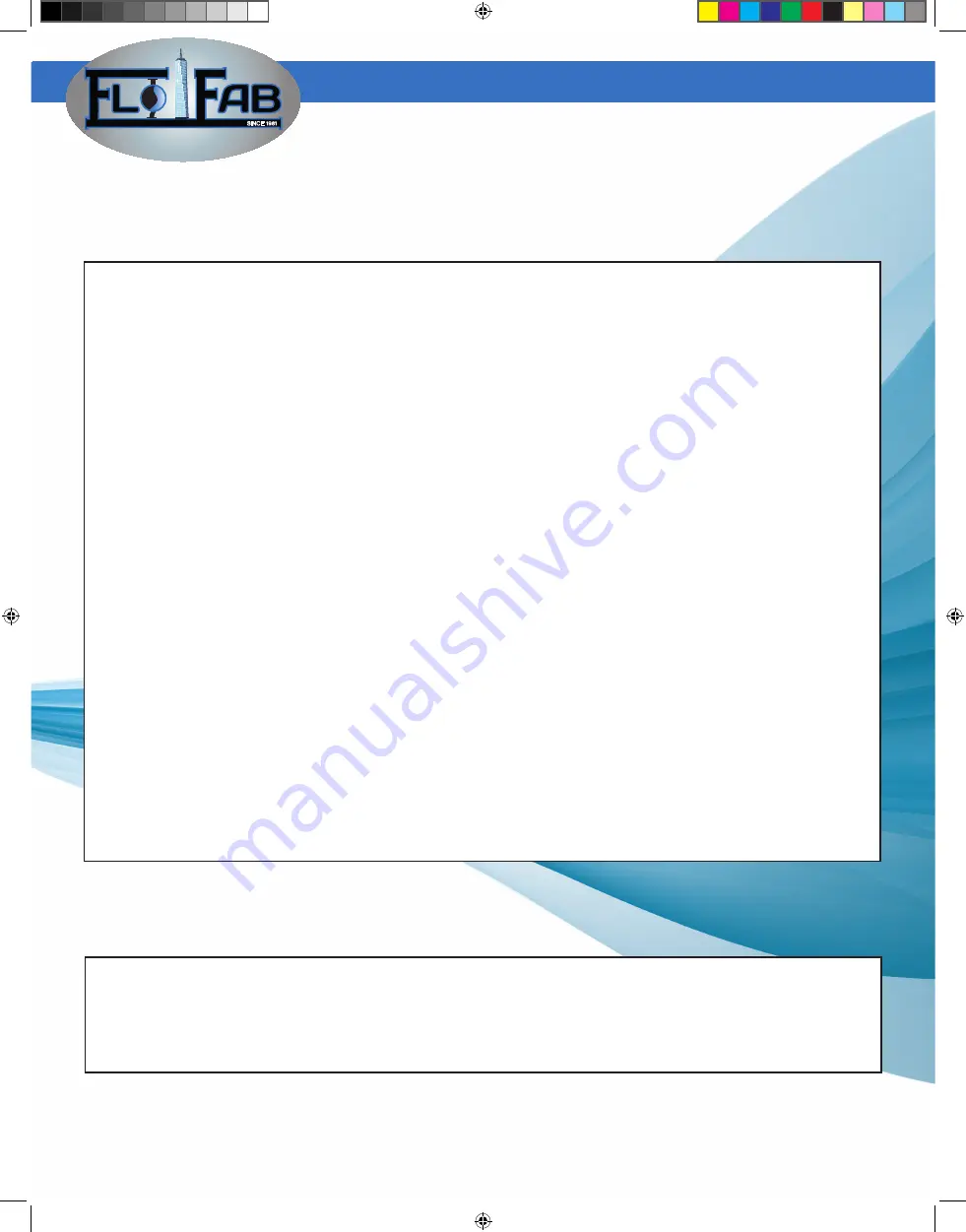
SINCE 1981
4
Each plate has a gasket that produces a sealing and channel system through the entire plate
pack in which the two heat exchanging media flow in a counter-current direction.
The circular portion of the gasket stops the fluid from going across the heat transfer plate and
sends it to the next open channel. The remaining portion or field gasket, directs the opposing
fluid across the heat transfer surface.
The gasket can be mechanically clipped to the plate with the glue free “U” shaped clip or glued
in place.
STARTING OF ELECTRIC MOTOR DRIVEN PUMPS
1. Before connecting motor and starter to the line:
1.1. Check wiring information available inside the conduit box.
1.2. Check voltage and frequency of power supply with what s shown on motor nameplate.
1.3. Check current rating of overload relays and fuses against nameplate full load current
value.
2.
Check lubrication and pocking (see MAINTENANCE}.
3.
Check if rotor is free to turn. It must be possible to revolve the rotor by hand. If the
rotor drags even slightly, do not operate until the cause of trouble is located and correc-
ted.
4.
For unit with fluid drive, refer to the maintenance instructions of Auid drives.
5.
If unit is for high temperature application, refer to operating instructions For high tem-
perature pumps.
6.
Prime the pump. A pump is primed when cosing and suction line are filled with liquid
and when all the air contained in the pump has been allowed to escape. If pump is to
operate under suction lift without foot valve, priming is done by pumping air out by
means of an ejector, on exhauster or a vacuum pump.
7.
Check direction of driver rotation. Proper direction is indicated by arrow on pump ca
sing.
8.
Check electric motor current as soon as motor is started to verify whether or not the
mechanical load applied corresponds to the motor rating. The continuous full load cur
rent value should be within the electric motor nameplate rating with service factor taken
into account.
OPERATION
A.
MAKE SURE THE GATE VALVE ON PUMP SUCTION IS FULLY OPEN AS THROTILING ON
SUCTION SIDE IS HARMFUL TO THE PUMP.
B.
MAKE SURE PUMP WILL NOT RUN DRY. MOST CENTRIFUGAL PUMPS HAVE CLOSE CLEA-
RANCES AND CANNOT RUN DRY WITHOUT SERIOUS DAMAGE RESULTING.
CAUTION
I.O.M - 880RI SERIES
IOM 880RI.indd 5
2017-11-14 13:03:59
Summary of Contents for 880RI Series
Page 14: ......
Page 15: ......
Page 16: ......
Page 17: ......
Page 18: ......
Page 19: ......
Page 20: ......
Page 21: ......
Page 22: ......
Page 23: ......
Page 24: ......
Page 25: ......
Page 26: ......
Page 27: ......
Page 28: ......
Page 29: ......
Page 30: ......
Page 31: ......
Page 32: ......
Page 33: ......
Page 34: ......
Page 35: ......
Page 36: ......
Page 37: ......
Page 38: ......
Page 39: ......
Page 40: ......