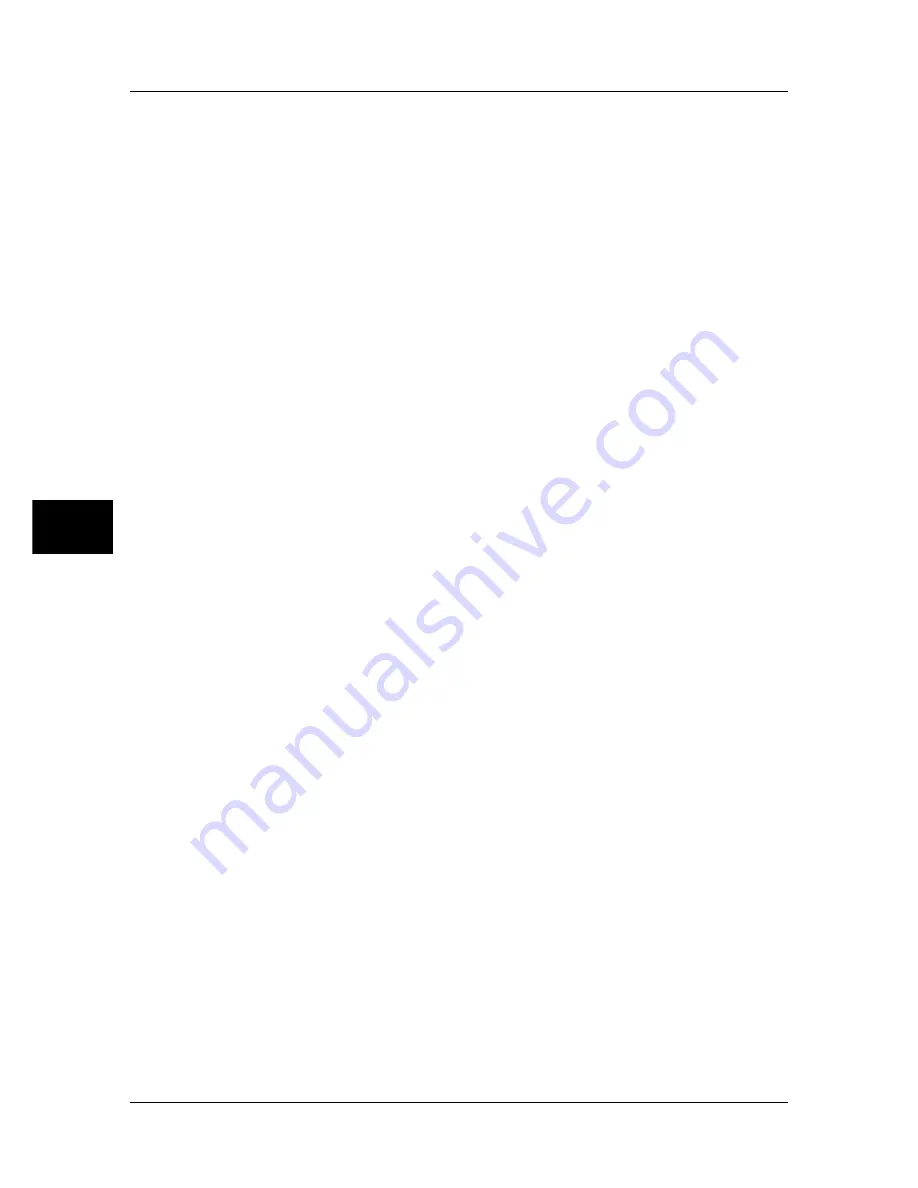
The classification of the defects gives a more detailed meaning that not only takes
into account the situation at the time of inspection (which is certainly of great impor-
tance), but also the possibility to normalize the over-temperature to standard load
and ambient temperature conditions.
An over-temperature of +30°C (+86°F) is certainly a significant fault. But if that over-
temperature is valid for one component working at 100% load and for another at 50%
load, it is obvious that the latter will reach a much higher temperature should its load
increase from 50% to 100%. Such a standard can be chosen by the plant’s circum-
stances. Very often, however, temperatures are predicted for 100% load. A standard
makes it easier to compare the faults over time and thus to make a more complete
classification.
7.2.5
Priority
Based on the classification of the defects, the maintenance manager gives the defects
a repair priority. Very often, the information gathered during the infrared survey is put
together with complementary information on the equipment collected by other means
such as vibration monitoring, ultrasound or the preventive maintenance scheduled.
Even if the IR inspection is quickly becoming the most used method of collecting in-
formation about electrical components safely with the equipment under normal oper-
ating conditions, there are many other sources of information the maintenance or the
production manager has to consider.
The priority of repair should therefore not be a task for the IR camera operator in the
normal case. If a critical situation is detected during the inspection or during the
classification of the defects, the attention of the maintenance manager should of
course be drawn to it, but the responsibility for determining the urgency of the repair
should be his.
7.2.6
Repair
To repair the known defects is the most important function of preventive maintenance.
However, to assure production at the right time or at the right cost can also be impor-
tant goals for a maintenance group. The information provided by the infrared survey
can be used to improve the repair efficiency as well as to reach the other goals with
a calculated risk.
To monitor the temperature of a known defect that can not be repaired immediately
for instance because spare parts are not available, can often pay for the cost of in-
spection a thousandfold and sometimes even for the IR camera. To decide not to
repair known defects to save on maintenance costs and avoid unnecessary downtime
is also another way of using the information from the IR survey in a productive way.
7
20
Publ. No. 1558439 Rev. a156 – ENGLISH (EN) – February 28, 2006
7 – Introduction to thermographic inspections of electrical installations
Summary of Contents for TermaCAM E45
Page 2: ......
Page 4: ......
Page 6: ......
Page 7: ...ThermaCAM EX300 User s manual Publ No 1558439 Rev a156 ENGLISH EN February 28 2006...
Page 162: ...148 Publ No 1558439 Rev a156 ENGLISH EN February 28 2006...
Page 163: ......