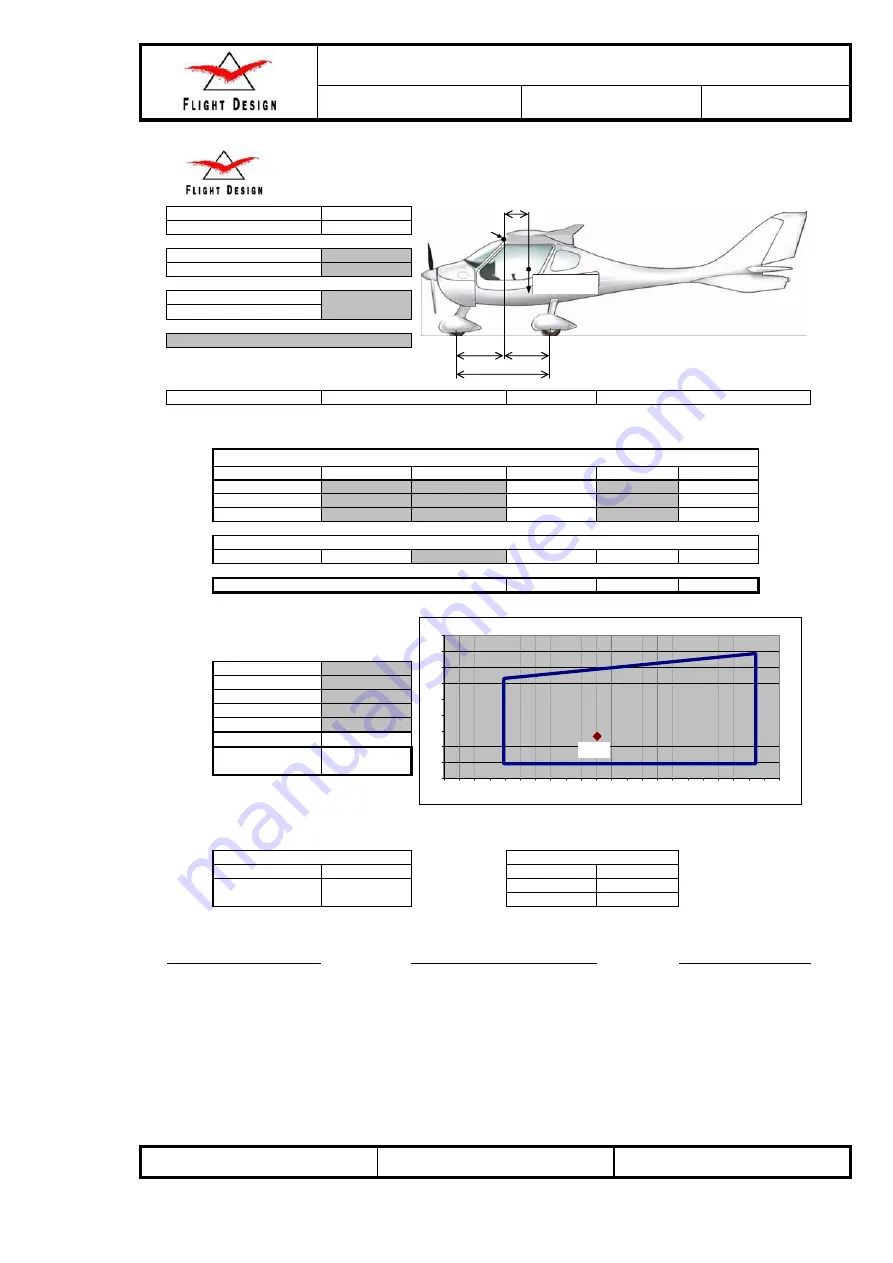
Aircraft Operating Instructions (AOI)
Type:
CT
Series:
CTLS
LSA
Page: 6-2
AU 010 11000
Revision No. 4
Date: 29 Apr 2008
XXXX
CT
CTLS
xx-xx-xx
yyyyyyy
Datum Plane:
Support point
Gross weight
Tara
Net weight
Distance to ref
Moment
Nose wheel
169,75 lb
0,00 lb
169,75 lb
33,9 in
-5748 lb*in
Main wheel left
266,75 lb
0,00 lb
266,75 lb
28,3 in
7562 lb*in
Main wheel right
264,11 lb
0,00 lb
264,11 lb
28,3 in
7487 lb*in
Fuel
0 gal
0,00 lb
8,3 in
0 lb*in
700,62 lb
13,3 in
9301 lb*in
Component weight
Wing left
78,92 lb
Nicht löschen - Vorgabe für Diagramm
Wing right
77,60 lb
639,329806
9,80313
Stabilizer
12,35 lb
639,329806
20,58305922
Rudder
4,63 lb
804,6737213
23,720211
Fuselage
527,12 lb
804,6737213
9,80313
Control sum
700,62 lb
639,329806
9,80313
MTOW
1322,75 lb
Empty weight
700,62 lb
Max payload
622,13 lb
Max pl. fuselage
600,09 lb
17.Oct.2007
Date
dd-mm-yyyy
Type:
Model:
Production Number:
Total weight
Deductions
Empty Weight and cg
Grey fields require inputs
Weight and Balance of LSA Aircraft
Signature
Fedchun
Kherson, Ukraine
City
Engine Number:
Equipment list
with date:
Scaling and Empty Aircraft cg
Wing leading edge
Tunnel roof in cabin horizontal
Datum Point:
Weight of non-lifting
parts
700,62 lb
Max weight of non-
lifting parts
1144,18 lb
Summary:
Certification Basis
Data of Aircraft
Allowed empty aircraft cg range
Aircraft
8
10
12
14
16
18
20
22
24
26
600 610 620 630 640 650 660 670 680 690 700 710 720 730 740 750 760 770 780 790 800 810 820
Weight [lb]
cg po
siti
on
[in
]
b
a
G
1
G
2
x
s
G=G
1
+G
2
datum
point
c
b
a
G
1
G
2
x
s
G=G
1
+G
2
datum
point
c
Warning:
The empty weight data in this example does not correspond to an
actual aircrafts. Use only the empty weight and center of gravity data
from the most current weight record!
The weighing record provides an insight into the state of the aircraft at the time of
weighing. In addition to the empty weight with the currently installed equipment and
the relevant center of gravity, the weighing record also states the empty weight with