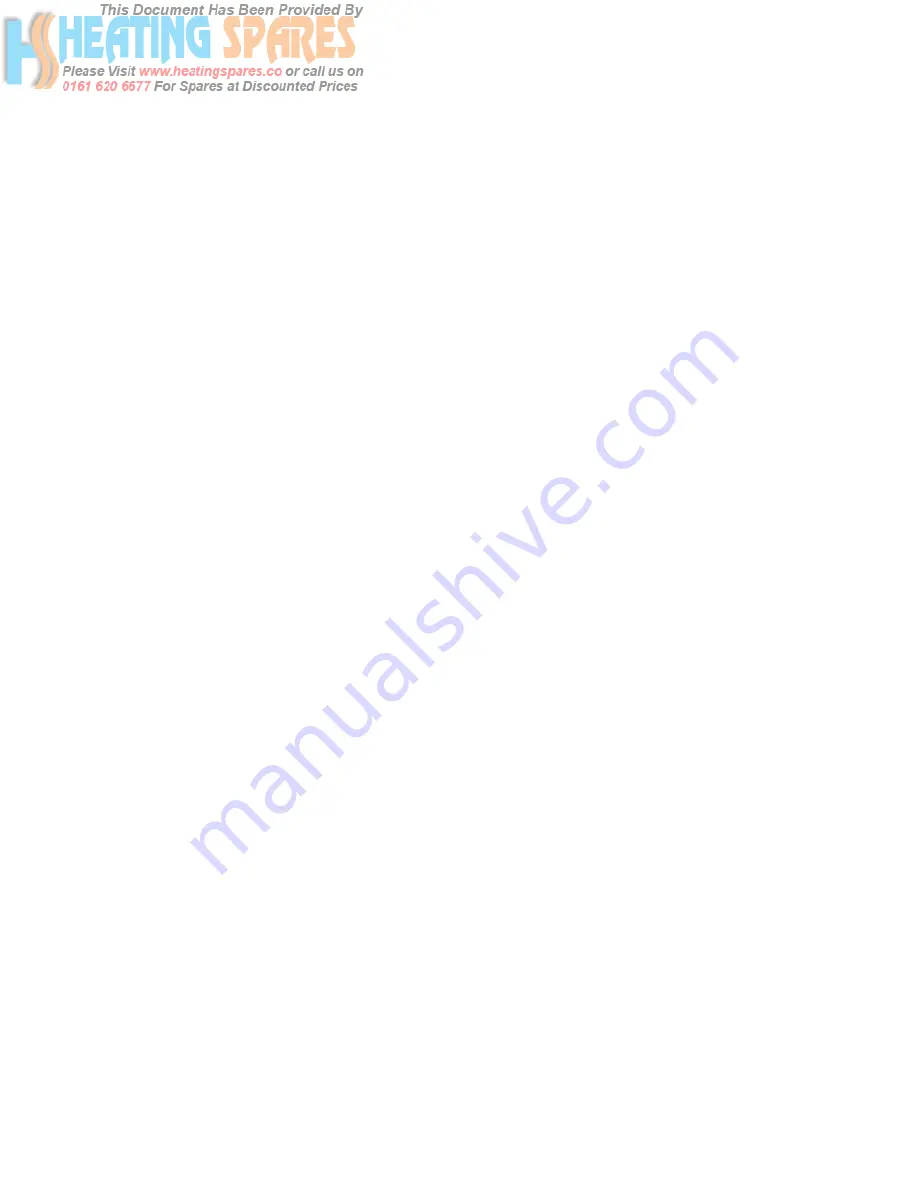
Supplied By www.heating spares.co Tel. 0161 620 6677
2.4
GAS TIGHTNESS
a)
Remove the pressure test point screw from the inlet elbow and fit a
manometer.
b)
Turn on the main gas supply and light the fire as described in section
3.2 and carry out a gas tightness test.
c)
Check that the gas pressure is 20.0 mbar (± 1.0 mbar), 8.0 in w.g. +/-
0.4 in w.g.
d)
Turn off the fire, remove the manometer and refit the pressure test point
screw. Check the pressure test point screw for gas tightness with the
appliance turned on using a suitable leak detection fluid or detector.
3.1
Completing the Assembly
a)
Fit the radiants by carefully inserting the upper end first into the radiant
canopy, and then lowering and seating the base of the radiants into the
radiant support channel.
b)
Refit the dress guard.
3.2
Lighting the Appliance
a)
Light the pilot by depressing the control knob at the “off” position and
turn anti-clockwise (with the control depressed) to the second position
marked *.
b)
When the pilot lights, (pilot can be seen through the bottom window of
right hand radiant) hold the control knob down for 10 seconds.
c)
If the pilot fails to light, repeat the ignition sequence and hold in the
control knob for slightly longer.
d)
When the pilot has lit, release the control knob from the depress
position, depress slightly again and turn the control anti-clockwise to the
high position and check for clearance of combustion products as
detailed below.
12