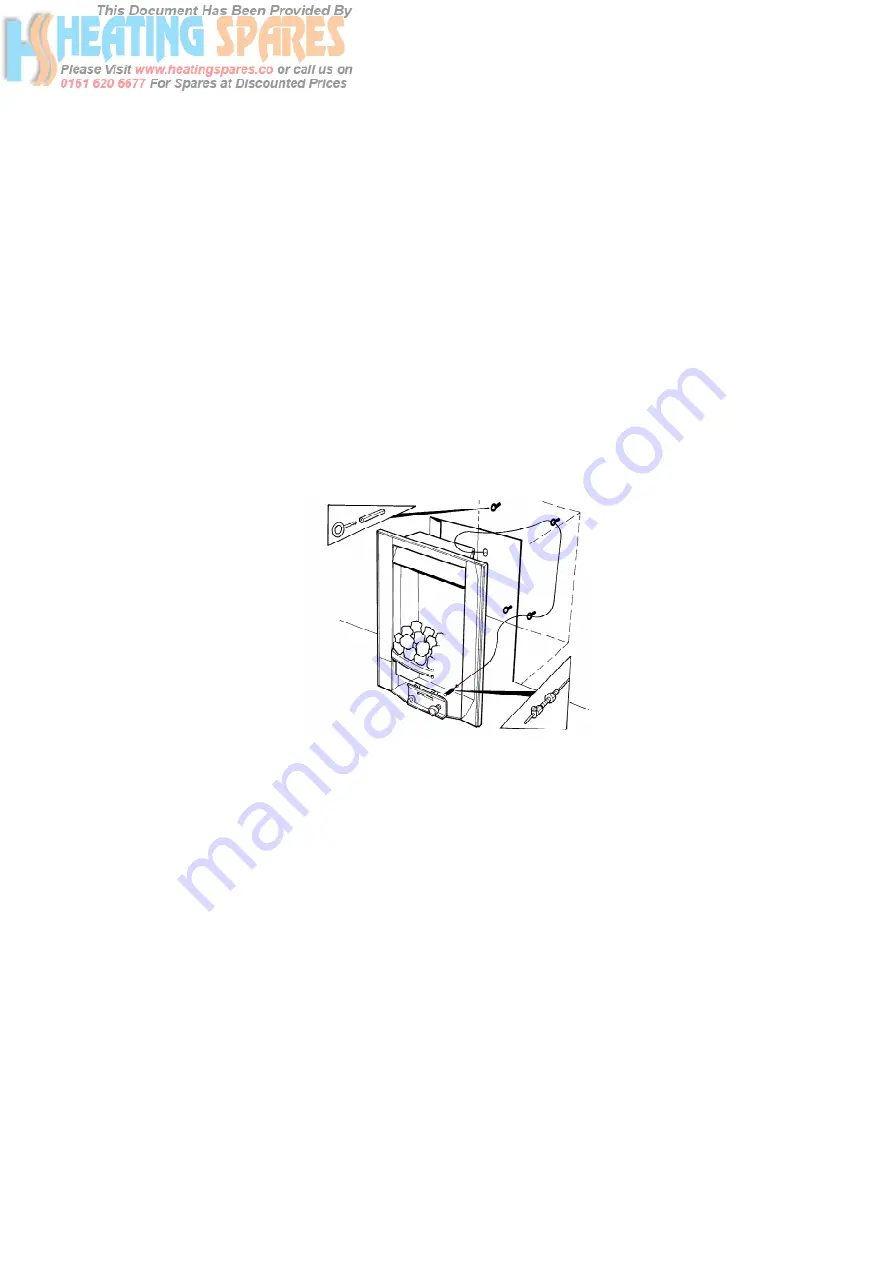
Supplied By www.heating spares.co Tel. 0161 620 6677
g)
Position the fire carefully on the (protected) surface of the hearth and
reach into the fire opening. Thread each of the cables vertically
downwards through the pair of fixing eyes on the same side of the fire.
Thread the free end of the cables through the corresponding circular
hole on each side of the lower rear of the fire. Carefully slide the fire
box back into the fire opening and pull both cables tight.
h)
Thread a tensioning screw over each of the cables and ensure that the
tensioning nut is screwed fully up against the hexagon shoulder of the
tensioning screw (this provides maximum travel for the tensioning nut).
i)
Fit a screwed nipple on to each of the cables and pull hand tight up
against the tensioning screw, then secure each nipple with a flat
bladed screwdriver. See fig. 8 below
Fig. 8
j)
Evenly tighten the tensioning nuts to tension both cables and pull the
fire snugly against the wall. Do not overtighten, it is only necessary to
pull the seal up against the sealing face of the wall, it does not need to
be compressed. Check that there are no gaps behind the seal.
k)
With the fire securely in place, if a concealed gas connection has been
made through either of the access holes in the sides or rear of the fire,
the holes should be closed around the pipe to prevent leakage of air
through the gap around the pipe.
l)
Refit the burner. Fit the four retaining screws and check that the burner
is correctly locked into position.
14