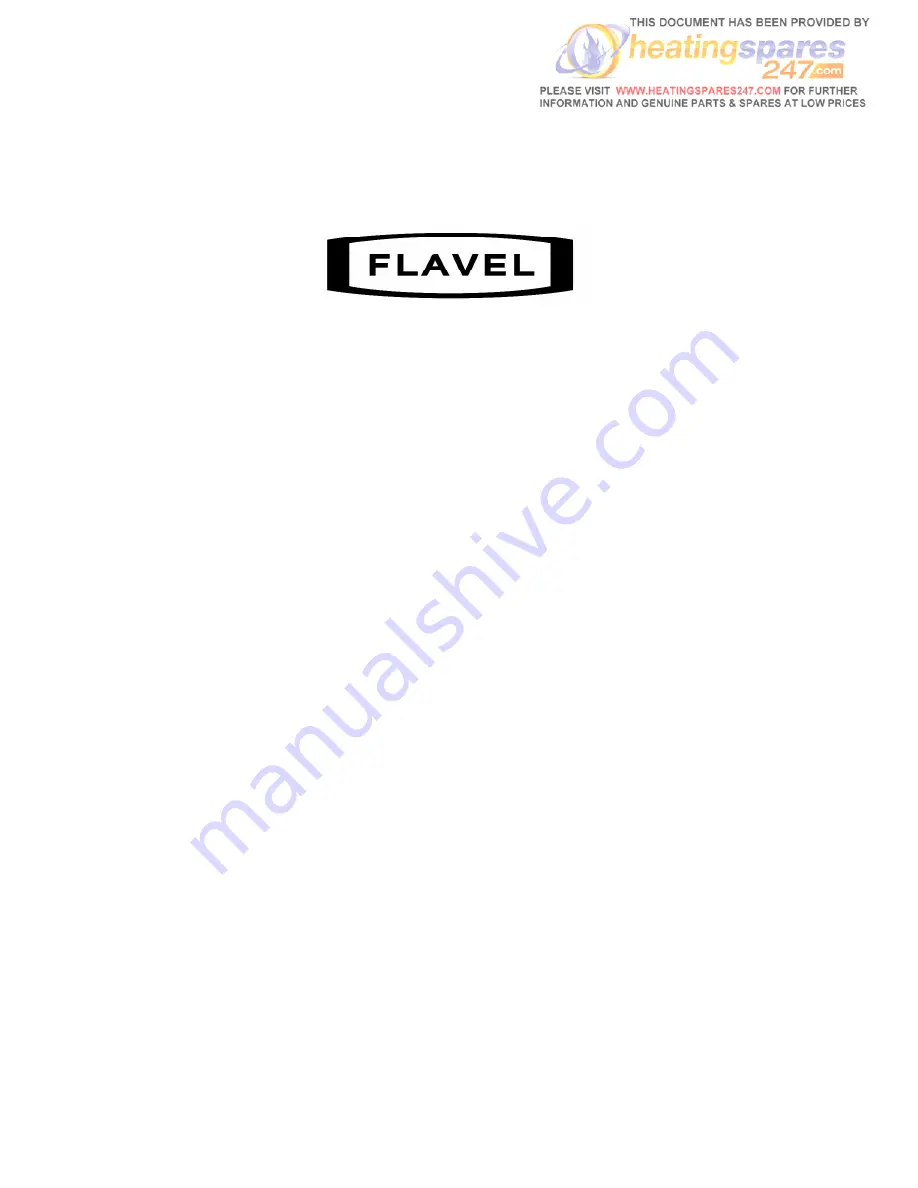
EMBERGLOW
CLASSIC
G.C. No. 32-022-034 (NG Models)
G.C. No. 32-022-035 (LPG Models)
RADIANT CONVECTOR GAS FIRE
User Instructions
This section of the instructions should be read by the user before
operating the appliance and retained for future reference
Model No. FEMC00MN is for use on Natural Gas (G20) at a supply
pressure of 20 mbar in G.B. / I.E.
Model No. FEMC00MP is for use on Propane Gas (G31) at a supply
pressure of 37 mbar in G.B. / I.E.
Summary of Contents for Emberglow Classic FEMC00MN
Page 30: ......