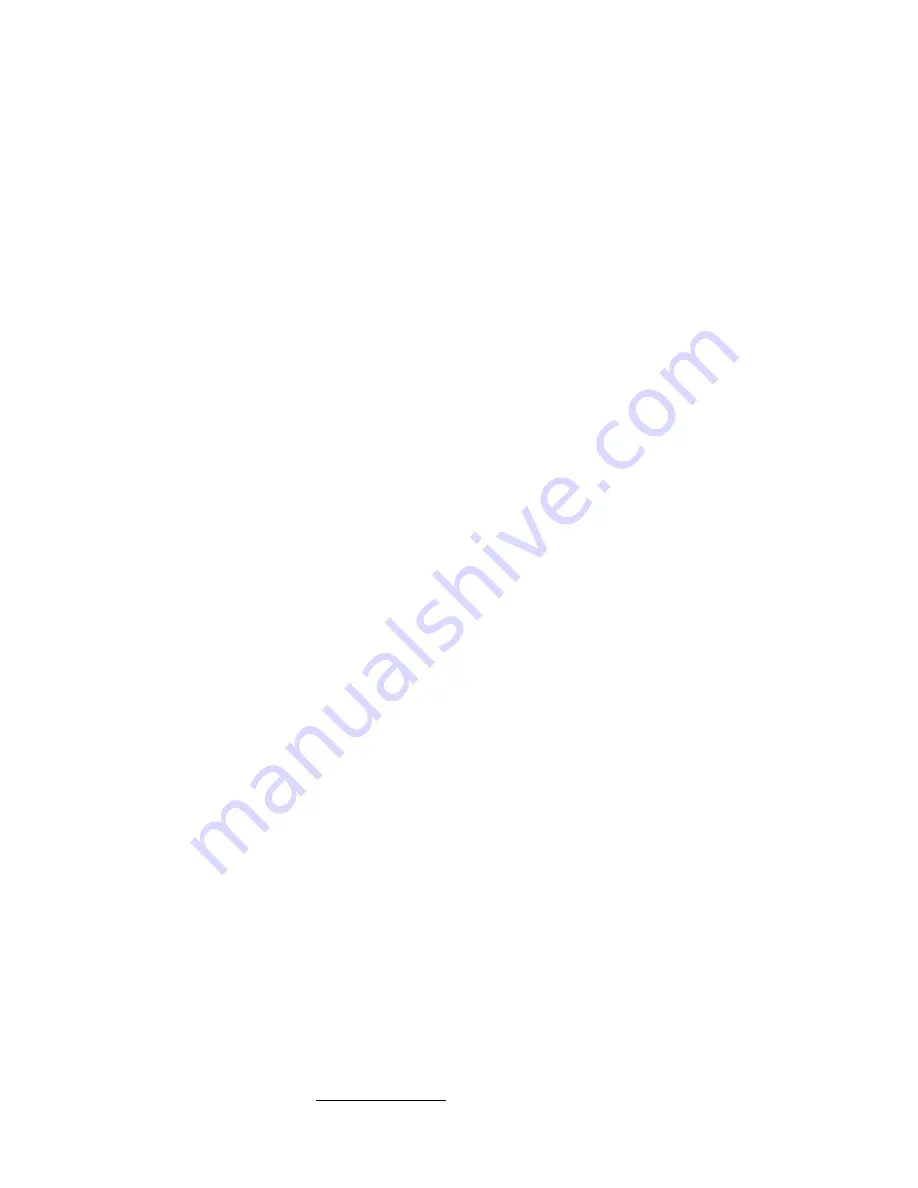
Inventor
Ⅱ
User Guide | www.flashforge.com
400-699-1063
5
Notice
Safety Notice
! Notices
: Read all the instructions in the manual and familiarize yourself with the
FlashForge Inventor
Ⅱ
User Guide before setting-up and using. Failure to comply with
the warning and instructions may result in individual injury, fire, equipment damage or
property damage.
PLEASE STRICTLY FOLLOW ALL THE SAFETY WARNINGS AND NOTICE
BELOW ALL THE TIME.
· Work Environment Safety
①
Keep your work place tidy.
②
Do not operate Inventor
Ⅱ
in the presence of flammable liquids, gases or dust.
③
Keep Inventor
Ⅱ
out of children and untrained people’s reach.
· Electrical Safety
①
Always use the Inventor
Ⅱ
with a properly grounded outlet. Do not refit
Inventor
Ⅱ
plug.
②
Do not use Inventor
Ⅱ
in damp or wet locations. Do not expose Inventor
Ⅱ
to
burning sun.
③
In case of device damage, please use the power supply provided by FlashForge.
④
Avoid using the device during an thunderstorm.
⑤
In case of uncertain accident, please unplug the device if you do not use it for long.
·Personal Safety
①
Do not touch the nozzle and build plate during printing.
②
Do not touch the nozzle after finishing printing.