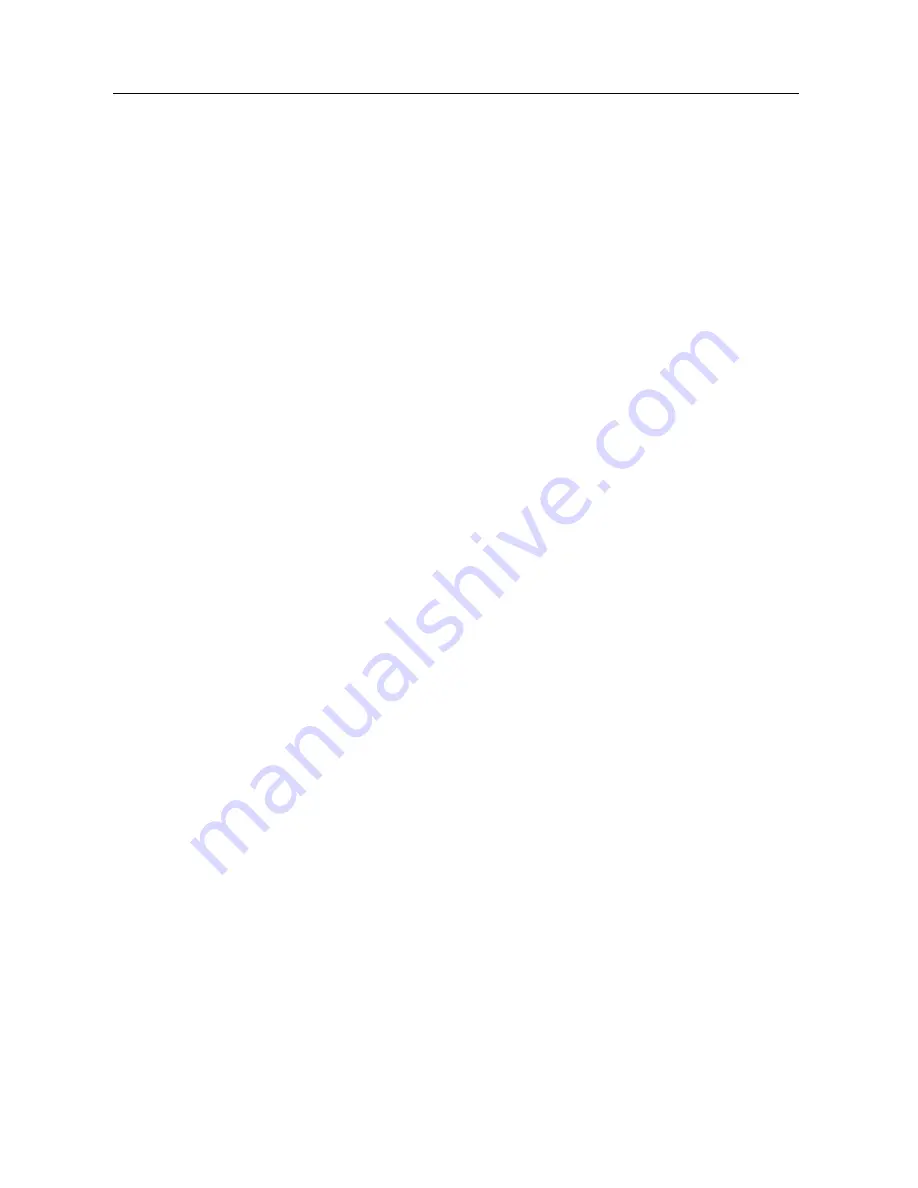
Maintenance Manual FK 9
B&F Technik Vertriebs GmbH
Revision 2
Section 0 Introduction
page 1
document code: des.003
TABLE OF CONTENTS
0.
INTRODUCTION ....................................................................................................................................... 0-6
0.1.
Revisions ..................................................................................................................................... 0-6
0.2.
Record of Revisions ................................................................................................................... 0-6
0.3.
List of effective Pages ................................................................................................................ 0-7
1.
GENERAL ................................................................................................................................................. 1-1
1.1.
Equipment List ............................................................................................................................ 1-1
1.1.1.
Placards .................................................................................................................................... 1-2
1.1.2.
Instrument Markings ................................................................................................................. 1-2
1.2.
Sources to purchase Parts ........................................................................................................ 1-2
1.3.
List of disposable replacement parts ....................................................................................... 1-3
1.4.
Engine specifications ................................................................................................................. 1-3
1.4.1.
Power Plant Limitations ............................................................................................................ 1-3
1.5.
Weight and Balance ................................................................................................................... 1-4
1.5.1.
Abbreviations and Terminology ................................................................................................ 1-4
1.5.2.
Basic Empty Weight .................................................................................................................. 1-4
1.5.3.
Weighing ................................................................................................................................... 1-5
1.5.4.
Required Tools .......................................................................................................................... 1-5
1.5.5.
Parts/materials required ............................................................................................................ 1-5
1.5.6.
Level of maintenance ................................................................................................................ 1-5
1.5.7.
Certification required ................................................................................................................. 1-5
1.6.
Tire Inflation Pressure ................................................................................................................ 1-6
1.7.
Approved Oils and Capacities................................................................................................... 1-6
1.7.1.
Oil .............................................................................................................................................. 1-6
1.7.2.
Fuel ........................................................................................................................................... 1-6
1.7.3.
Coolant ...................................................................................................................................... 1-6
1.7.4.
Brake Fluid ................................................................................................................................ 1-6
1.8.
Recommended Fastener Torque Values .................................................................................. 1-7
1.9.
General Safety Information ........................................................................................................ 1-7
1.10.
Instructions for Reporting ......................................................................................................... 1-7
2.
INSPECTIONS .......................................................................................................................................... 2-1
2.1.
Inspections .................................................................................................................................. 2-1
2.1.1.
Required Tools .......................................................................................................................... 2-1
2.1.2.
Parts/materials required ............................................................................................................ 2-1
2.1.3.
Level of maintenance ................................................................................................................ 2-1
2.1.4.
Certification required ................................................................................................................. 2-1
2.2.
General Advice ........................................................................................................................... 2-1
2.3.
Regular Maintenance and Lubrication Schedule .................................................................... 2-2