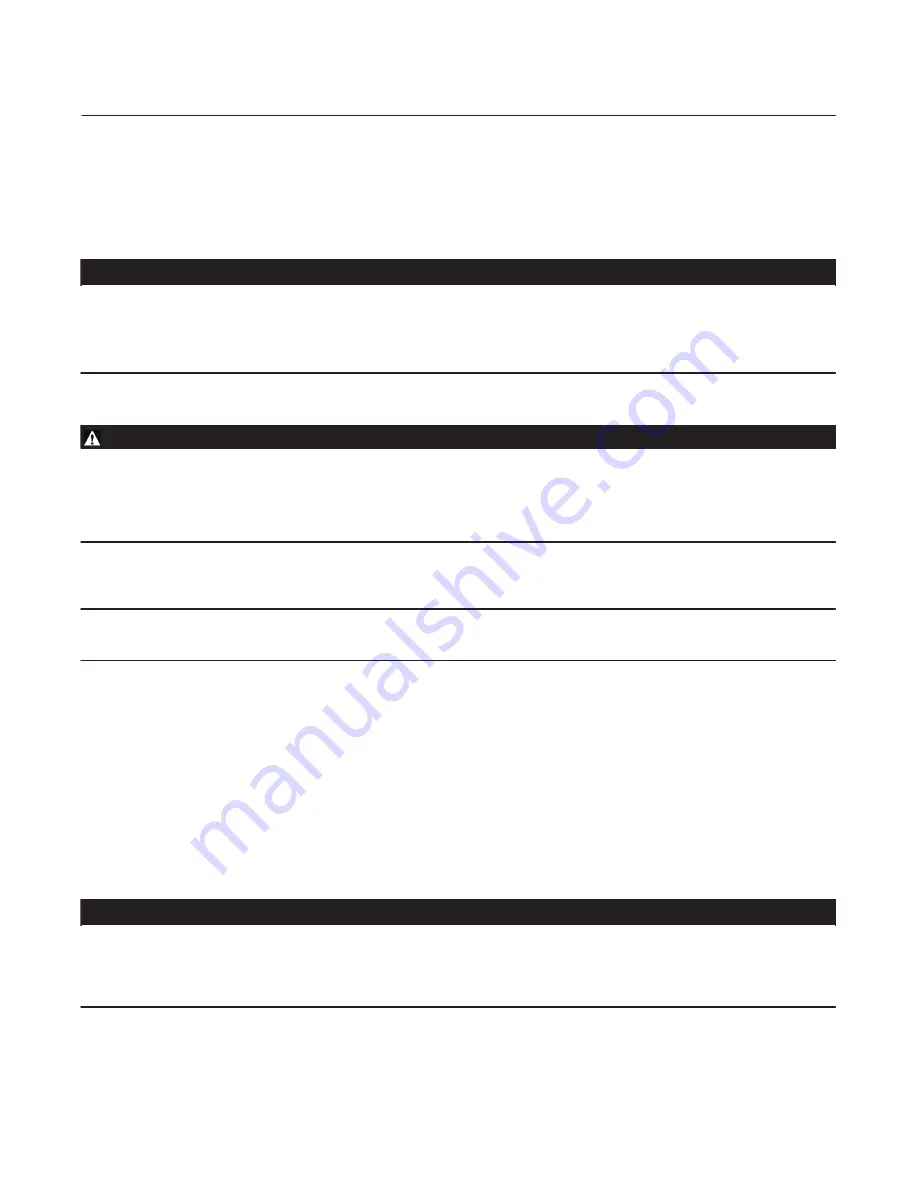
Instruction Manual
D103211X012
NotchFlo DST Valve
March 2011
10
3. Remove either the yoke locknut (key 32) or the hex nuts (key 30), and remove the actuator from the bonnet (key
18).
4. Loosen the packing flange nuts (key 21) so that the packing (keys 22, 23, 209, or 210, figures 3, 4, or 5) is not tight
on the valve plug stem (key 6). Remove any travel indicator disk and stem locknuts from the valve plug stem
threads.
CAUTION
When lifting the bonnet (key 18), be sure that the valve plug and stem assembly (keys 5 and 6) remains on the seat ring
(key 4). This avoids damage to the seating surfaces as a result of the assembly dropping from the bonnet after being lifted
part way out. The parts are also easier to handle separately.
Use care to avoid damaging gasket sealing surfaces.
WARNING
To avoid personal injury or property damage caused by uncontrolled movement of the bonnet, loosen the bonnet by
following the instructions in the next step. Do not remove a stuck bonnet by pulling on it with equipment that can stretch
or store energy in any other manner. The sudden release of stored energy can cause uncontrolled movement of the bonnet.
If the cage sticks to the bonnet, proceed carefully with bonnet removal and support the cage so that it will not fall
unexpectedly from the bonnet.
Note
The following step also provides additional assurance that the valve body fluid pressure has been relieved.
5. Hex nuts (key 14) attach the bonnet to the valve body. Loosen these nuts approximately 3 mm (1/8 inch). Then
loosen the body‐to‐bonnet gasketed joint by either rocking the bonnet or prying between the bonnet and valve
body. Work the prying tool around the bonnet until the bonnet loosens. If no fluid leaks from the joint, proceed to
the next step. If fluid leaks from the joint, the process pressure was not relieved from the valve as noted in the
Warning at the beginning of the Maintenance section in this manual.
6. Unscrew the hex nuts (key 14) and carefully lift the bonnet off the valve stem. If the valve plug and stem assembly
starts to lift with the bonnet, use a brass or lead hammer on the end of the stem and tap it back down. Set the
bonnet on a cardboard or wooden surface to prevent damage to the bonnet gasket surface.
7. Remove the valve plug (key 5), bonnet gasket (key 11), cage (key 2), cage gaskets (if applicable) (key 65), seat ring
(key 4), and the seat ring gasket(s) (key 12).
CAUTION
Inspect the seat ring, cage, bonnet, and body gasket surfaces. These surfaces must be in good condition, with all foreign
material removed. Small burrs less than approximately 0.076 mm (0.003 inch) in height (the thickness of a human hair) can
be ignored. Scratches or burrs that run across the serrations are not permitted under any conditions, since they will
prevent the gaskets from sealing properly.
8. Clean all gasket surfaces with a good wire brush. Clean in the same direction as the surface serrations, not across
them.