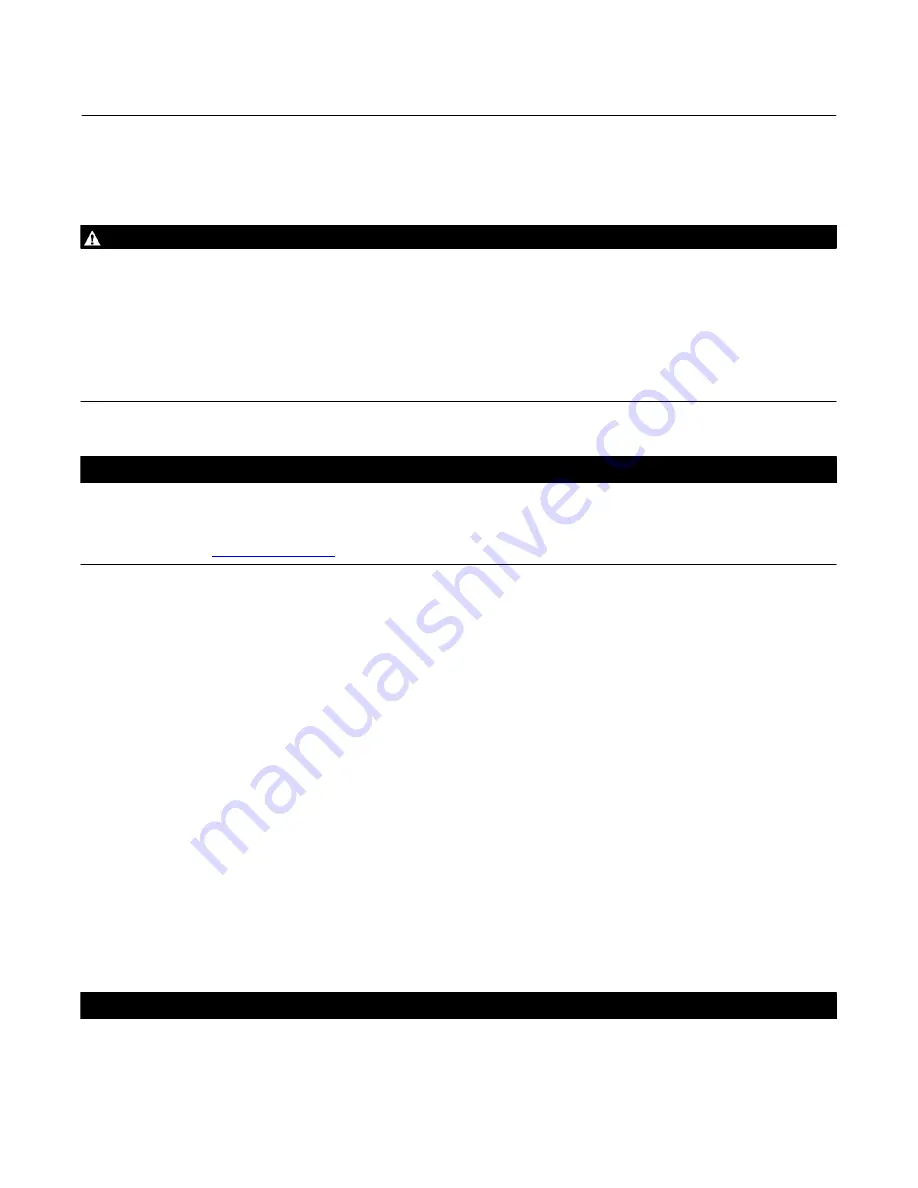
Instruction Manual
D103298X012
Control-Disk Valve
June 2017
4
Installation
Key numbers in this procedure are shown in figure 10 unless otherwise indicated.
WARNING
Always wear protective gloves, clothing and eyewear when performing any installation operations to avoid personal
injury.
To avoid personal injury or property damage resulting from the bursting of pressure retaining parts, be certain the service
conditions do not exceed either the valve body rating or the flange joint rating, or other limits given in table 1 or on the
nameplate. Use pressure‐relieving or pressure‐limiting devices to prevent the service conditions from exceeding these
limits.
If installing into an existing application, also refer to the WARNING at the beginning of the Maintenance section on page 7
in this manual.
CAUTION
The valve configuration and construction materials were selected to meet particular pressure, temperature, pressure drop,
and controlled fluid conditions specified in the customer's order. Because some valve body/trim material combinations are
limited in their pressure drop and temperature range capabilities, do not apply any other conditions to the valve without
first contacting your
Emerson sales office
or Local Business Partner.
The maximum allowable inlet pressures for steel and stainless steel valve bodies are consistent with the
pressure‐temperature ratings shown in table 1, except where further limited by the trim and packing material
temperature capabilities given in table 3. Valves are also available in CW2M and M35‐2 valve body materials. The
CW2M valve body material is not listed in EN 12516-1 or in ASME B16.34. The M35-2 valve body material is listed in
ASME B16.34, but is not listed in EN 12516-1. Valve bodies constructed of these materials mate with EN and ASME
flanges, but must not be installed in systems requiring conformance to EN or ASME standards if not included in EN or
ASME pressure/temperature ratings. Maximum allowable inlet pressures for Control‐Disk valve bodies made of CW2M
or M35‐2 construction materials are shown in table 4.
1. Install a three‐valve bypass around the control valve assembly if continuous operation is necessary during
inspection and maintenance of the valve.
2. Inspect the valve body to be certain it is free of foreign material.
3. The valve is normally shipped as part of a control valve assembly, with an actuator mounted on the valve body.
If the valve body and actuator have been purchased separately or if the actuator has been removed for maintenance,
mount the actuator, and adjust actuator travel before inserting the valve body into the line. This is necessary due to
the measurements that must be made during the actuator adjustment process. Refer to the Actuator Mounting
section on page 18 of this manual and to the separate actuator instruction manual for mounting and adjusting
instructions before proceeding.
4. Inspect adjacent pipelines to be certain they are free of any foreign material, such as pipe scale or welding slag, that
could damage the valve body seating surfaces.
CAUTION
Damage to the disk (key 3) will occur if any pipe flanges or piping connected to the valve body interfere with the disk
rotation path. However, the disk can be rotated without interference when the valve body is installed between adjacent
pipe flanges or piping that has an inside diameter equal to or greater than either schedule 80 pipe or compatible EN pipe