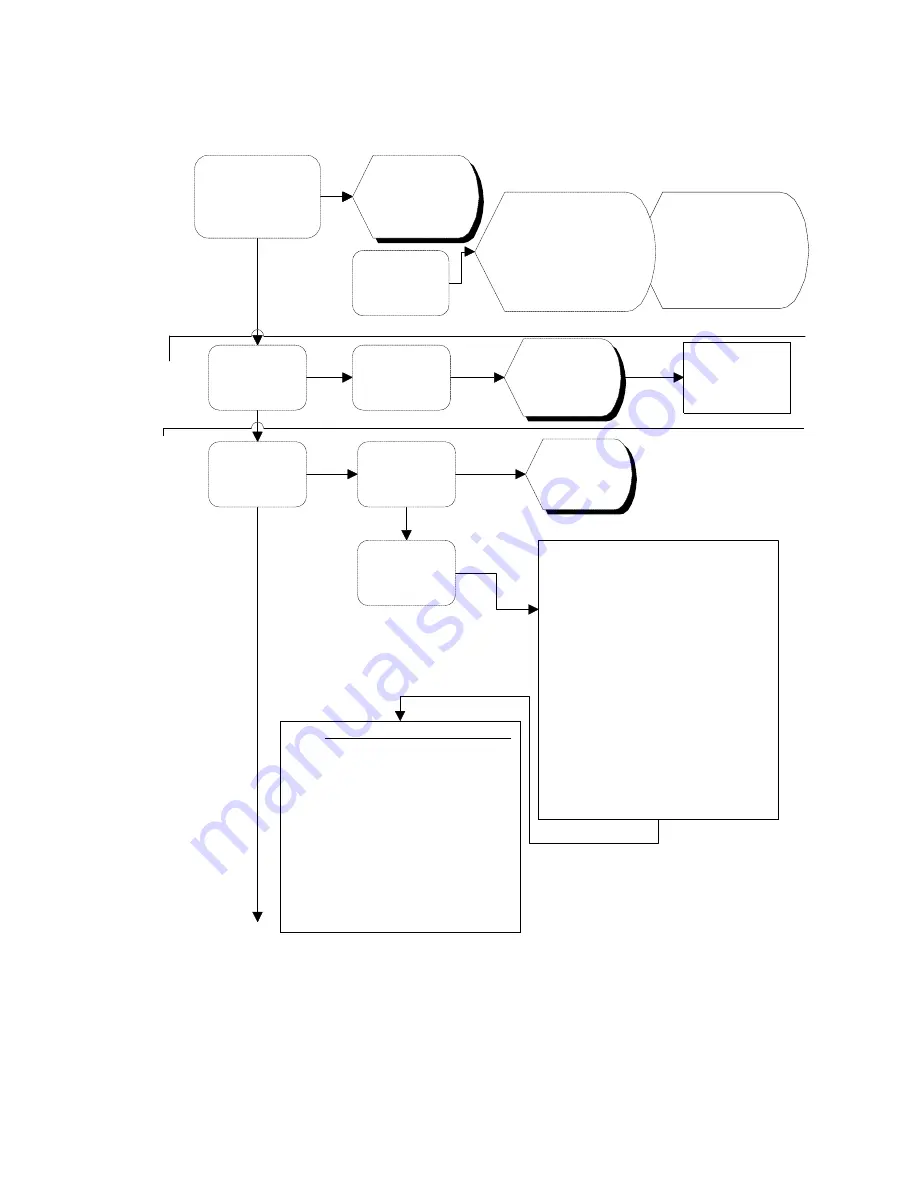
- 18 -
4.4
Diagnostics Quick Reference Flow Chart
To clear the current
fault code press the
Keylock once. Note if
you press Keylock
again you will remove
the previous fault.
Press and hold
Keylock, then
Start/Pause buttons
for 6 seconds
Press
Start/Pause
button
Press Power
button
Press
Start/Pause
button
Press Power
Button
Press
Start/Pause
button
Press Keylock
button to turn
output On/Off
All LED's &
LCD segments
except Keylock
are illuminated
Initiate Pen upload via
Rinse program LED.
At the same time, first
the current, then the
previous fault code will
be displayed in the
LCD
Cycles
through every
LED & LCD
segment
Hardware
output
diagnostic
test mode
Disconnect
power supply to
exit Show Off
mode
EU = Exhaust valve
FU = Water Inlet Valve
dd = Detergent diverter valve
Er = Element relay
LS = Lid seal pump
rd = Rinse aid dispenser
P1 = Wash pump motor
P2 = Drain pump motor
dF = Drying fan
temp = currentwater temperature
Note:
Display green = output on
Display red = output off
Tub microswitch can be tested at
any time. Rinse LED on = Open
Rinse LED off =Closed
LED Heavy Normal Light Delicate
EU Off Off Off On
FU Off Off On Off
dd Off Off On On
LS Off On Off Off
rd Off On Off On
P1 Off On On Off
P2 Off On On On
dF On Off Off Off
Er On Off Off On
temp On Off On Off
#1 Display
Mode
#2 Show Off/Demo Mode
#3 Hardwre Output Test
Mode
See Next
Page