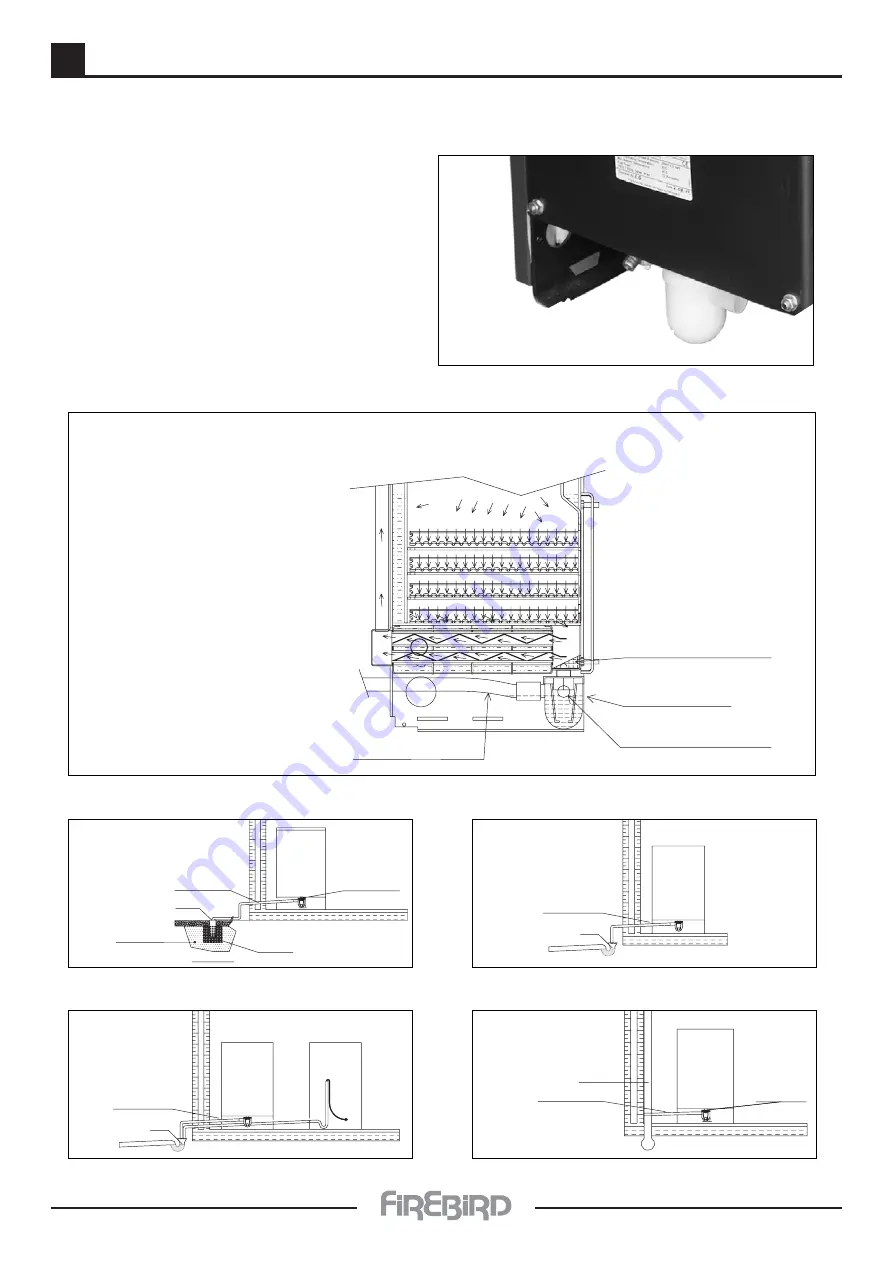
6
12
6.3 INSTALLATION - CONDENSATE DISPOSAL
CONDENSATE DISPOSAL
METHOD 1
CONDENSATE TRAP
IMPORTANT
Always prime condensate
trap with water.
Figure 1
Boiler
Sealed
Condensate Drain
Condensate Drain
Trap
Lime Stone
Chippings
Free Draining Soil
Soak Away
F
igur
e 1
Boiler
Condensate Drain
Washing
Machine
Gully
Waste
Pipe
Trap
F
igur
e 2
Boiler
Condensate Drain
Gully
Trap
F
igur
e 3
Boiler
Condensate drain
Stack
Trap
Discharge pipe
Condensate drain must have
a minimum diameter of 22mm
and it must be supported with
a 2.5˚ (1:100) fall from boiler.
F
igur
e 4
Condensate drain baffle
Condensate drain float
Condensate baffle and condensate trap
Condensate trap
Condensate hose
Before switching on your
Firebird condensing oil boiler
check that:
(1) The float & condensate drain
baffle are in place.
(2) That the condensate trap
is
primed.
(3) The condensate discharge
pipe is a corrosion
resistant
pipe.
The condensate trap is located
at the base of the boiler.
Summary of Contents for Enviromax Kitchen C12
Page 2: ......
Page 27: ...6 25 6 7 INSTALLATION FLUE ASSEMBLY SLIMLINE SYSTEMPAC...