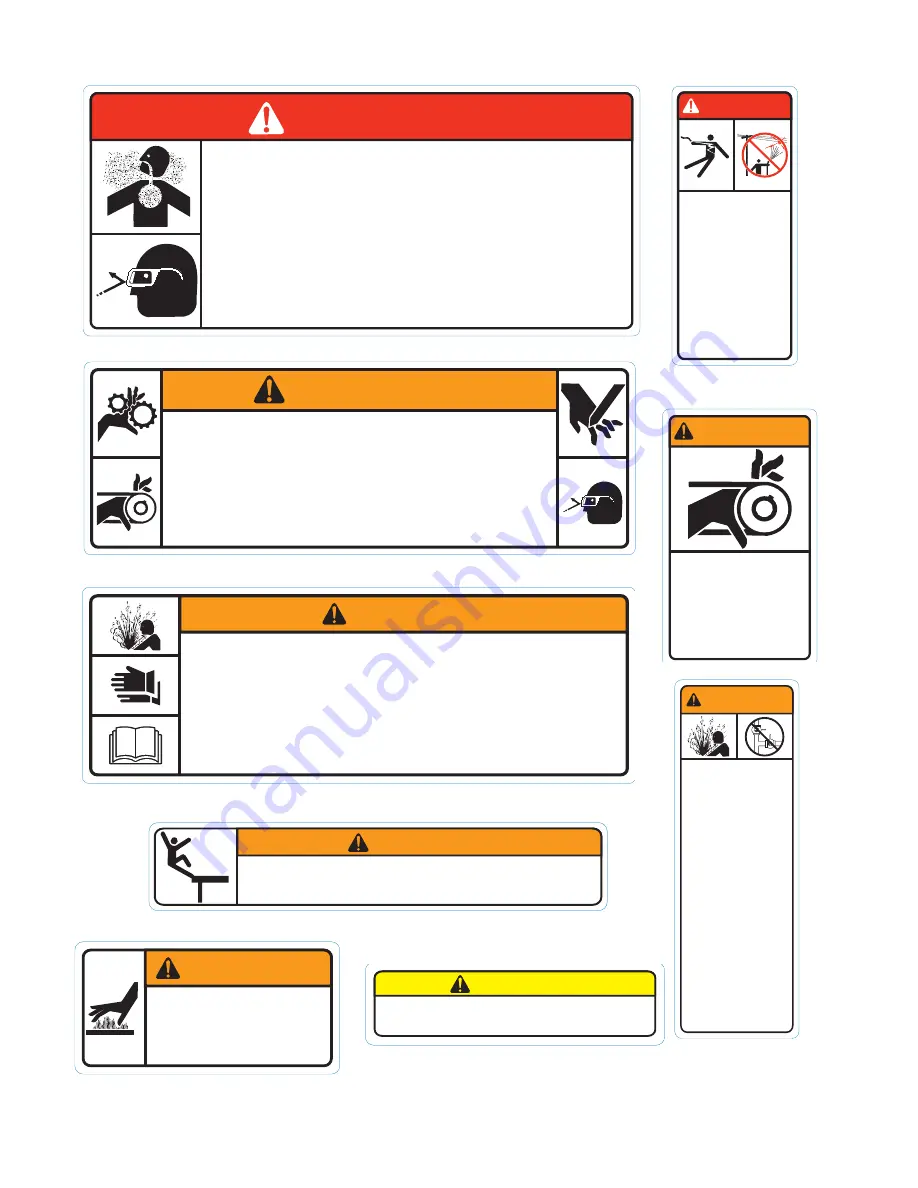
5
CURRENT SET OF SAFETY DECALS
P/N 5216
BURN HAZARD!
Contents could be
under pressure.
DO NOT come in
contact with material.
Ensure material in line
is not hot before
loosening clamps or
opening valves.
DO NOT operate pump
with both recirculation
and discharge valves
closed.
DO NOT use remote
valve unless
recirculation valve is
open.
Excessive heat or
bodily injury could
occur.
Failure to comply could
result in death or
serious injury.
WARNING
P/N 11567
DANGER
ELECTROCUTION
HAZARD!
DO NOT aim stream
toward electrical
lines.
Avoid spraying
toward bystanders.
Failure to comply
will result in death
or serious injury.
P/N 12179
Do not operate
without guards in
place.
Failure to comply
could result in death
or serious injury.
WARNING
012278
BURN HAZARD!
Hot exhaust!
Stay back!
Failure to comply could result
in death or serious injury.
WARNING
CONFINED SPACE HAZARD!
(Reference: OSHA 29 CFR 1910.146)
Before entering tank:
1. Drain, flush, and ventilate tank interior.
2. Turn off engine and disconnect battery cables.
3. Continuously ventilate area or wear appropriate breathing apparatus.
4. Provide standby individual outside tank able to communicate with
person inside and able to remove him with a lifeline if necessary.
FLYING MATERIAL HAZARD!
Wear eye protection around operating equipment.
Failure to comply will result in death or serious injury.
P/N 12686-01
DANGER
P/N 12688
FALL HAZARD!
ALWAYS face ladder when mounting and dismounting.
Failure to comply may result in moderate or minor injury.
CAUTION
P/N 12821
FALL HAZARD!
All gates must be closed during operation.
Failure to comply could result in death or serious injury.
WARNING
P/N 31462
BURN HAZARD!
Cooling system is under pressure.
Allow system to cool before handling.
Remove radiator cap slowly.
Wear appropriate safety gear.
Failure to comply could result in death or serious injury.
RADIATOR HANDLING INSTRUCTIONS
1. Use a 50/50 solution of water and antifreeze. Using 100% antifreeze will result in engine damage.
2. Check and replenish water prior to use. More water will be consumed when operating in hot conditions.
3. If overflow pipe begins emitting vapor, check and replenish water.
4. Remove and clean screen when dirty.
5. Check and clean fins periodically. Clogged fins will increase water consumption.
6. Protect radiator from fertilizer corrosion by washing radiator core with water.
WARNING
P/N 31463
SEVER HAZARD!
Keep hands clear!
Rotating fan and gears.
DO NOT operate without guards or doors in place.
Shut off engine, disconnect battery, and allow all moving parts to
stop before servicing.
FLYING DEBRIS!
Wear eye protection around equipment.
Failure to comply could result in death or serious injury.
WARNING
Summary of Contents for HydroSeeder TITAN280
Page 25: ...19 NOTES...
Page 44: ...38 3 2 2 8 1 10 4 6 2 6 9 1 2 9 7 8 LUBRICATION LOCATIONS...
Page 46: ...40 NOTES...