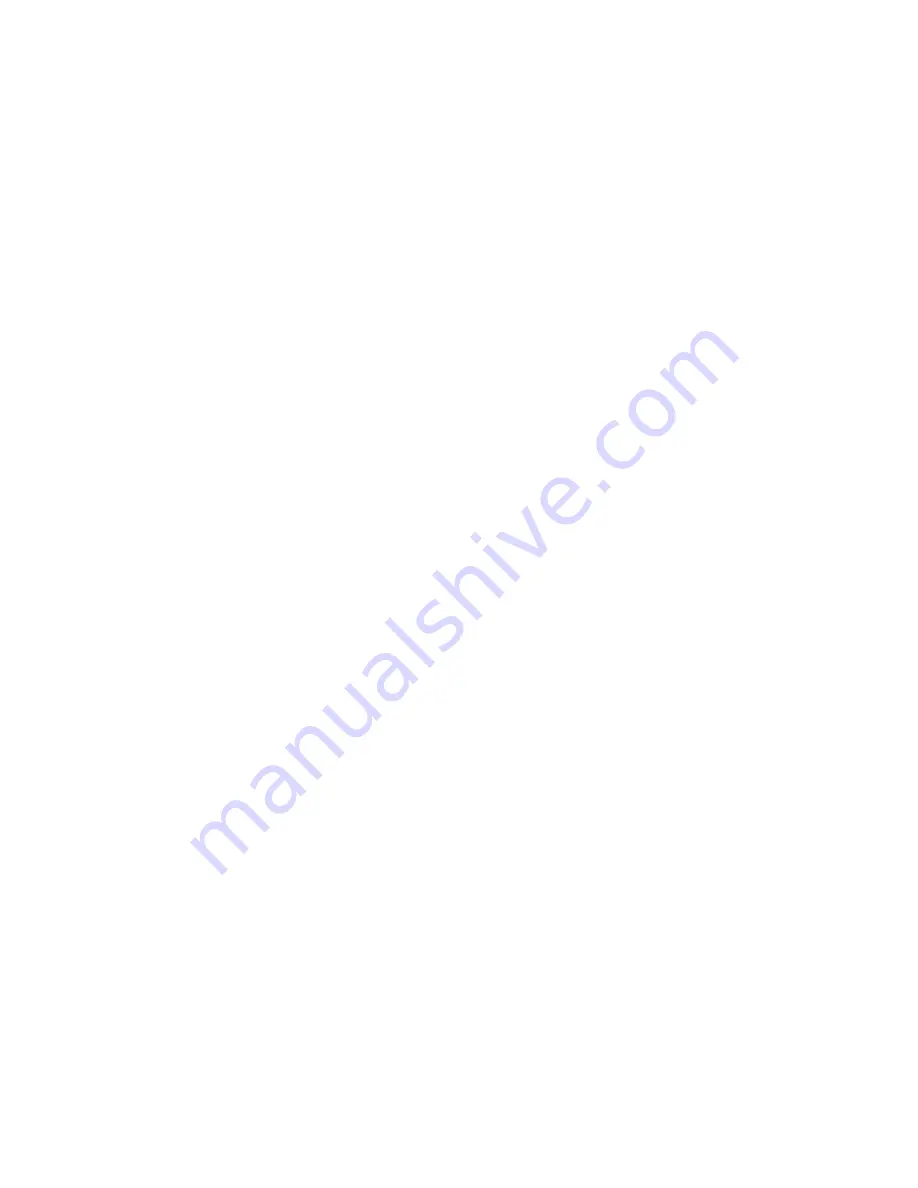
9
2. Holding the pump coupling half (item 2) in one hand, unthread the pump shaft (item 10) from the bearing
assembly (item 3) by turning it counterclockwise (right hand threads).
3. Remove the bearing assembly (item 3) and the seal assembly (item 4) from the pump head (item 5) being
careful not to damage the threaded area at the bottom of the bearing assembly. Discard the seal assembly
(never reuse the old seal).
Inspection
1. Visually inspect the compressor (item 11), and the 3 center bearings (item 9) for wear or damage. Replace as
needed.
2. Inspect the bearing assembly (item 3) for rust, corrosion, or tightness. Replace as needed.
3. Inspect the pump shaft in the seal area for wear and replace as needed.
Reassembly
1. Install the intake tube (item 6) into the pump head (item 5) by threading it counterclockwise (left hand
threads).
2. Insert the pump shaft assembly up through the bottom of the intake tube until the threaded part of the
shaft sticks out slightly from the pump head.
3. Warm up the seal assembly (item 4) with a heat lamp or by soaking it in hot water to aid in the installation
process.
4. Slide the seal over the shaft threads and onto the shaft so that the lip in the center of the seal is facing the
bottom of the pump. Push the seal just past the step on the shaft being careful not to damage the lip.
5. Thread on the bearing assembly. Carefully press the bearing assembly into the pump head, until the top of the
bearings are flush with the top of the pump head.
6. Turn the coupling half to verify there is no binding inside the pump.
Note:
Repair instructions can be downloaded from our web site at www.finishthompson.com or contact Technical Service at
1-800-888-3743.