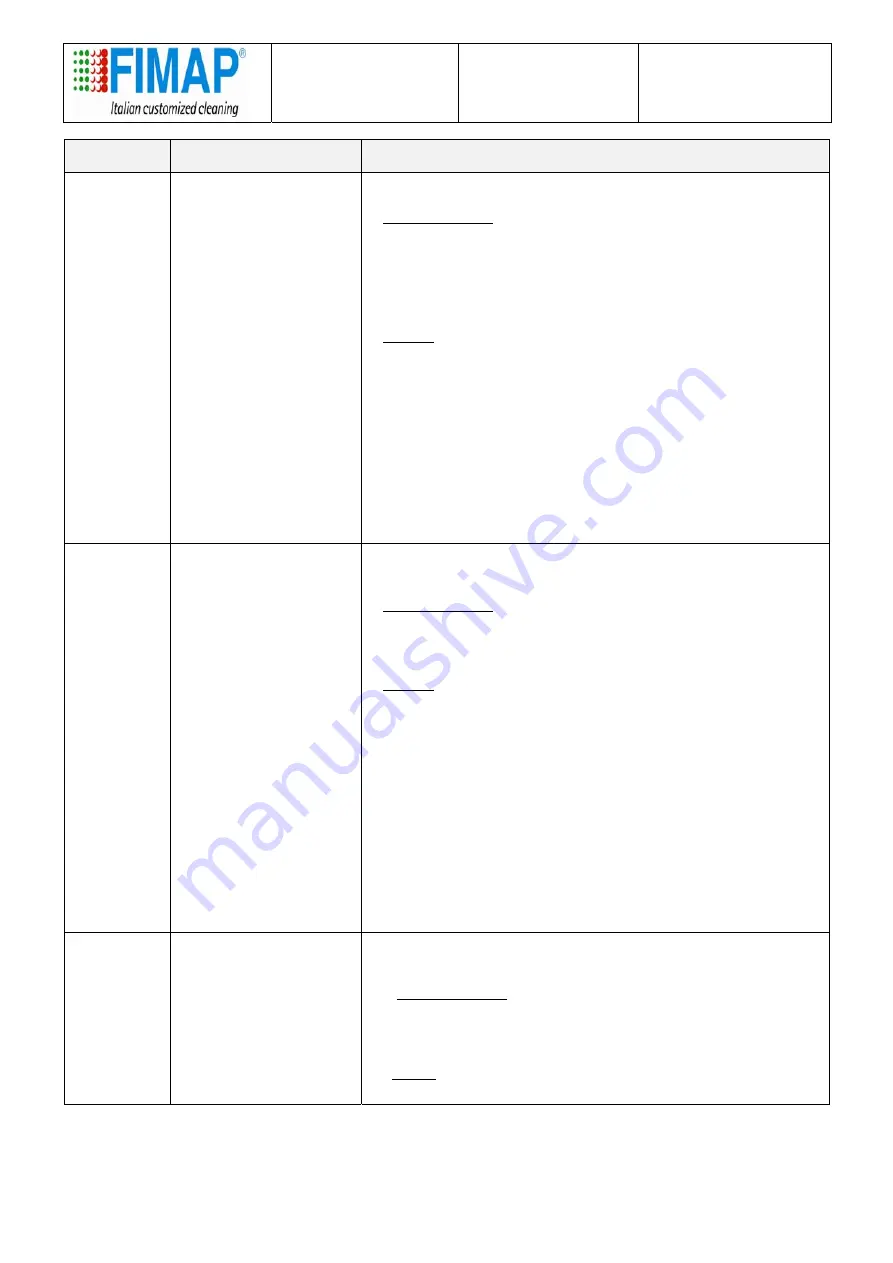
ADJUSTMENT
AND
INSPECTION
MAGNA 85 – 100 BS
Doc.
Issued 12/2006
Rev. 00
Pag.
5 di 18
Number of
blinkings
MESSAGE
NOTES
2 INCORRECT
START
Incorrect starting sequence
Possible causes
-
-
-
error in the sequence Key/drive selection made by the
operator
the micro pedal and/or micro drive are stuck
wiring not correct
Actions
check the starting sequence which is:
-
-
-
-
-
switch on the key
select drive (forwards/backwards)
press the accelerator
check that the drive microswitch and the manipulator
forward/backward traverse selector do not have the
contacts stuck and that they work correctly
verify the continuity of the circuit that connects the micro
drive pedal, the chopper card and the drive manipulator.
3 VMN
LOW
The first check recognises a voltage VMN lower than the
25% of the battery voltage
Possible causes
-
-
wrong connections on the motor
motor current leakage to the ground
Actions
-
-
-
check that the motor terminals are well isolated from the
motor casing both inside and outside the motor. Verify that
there is not dirt that causes current leakage between the
terminals and the motor body
verify that the motor is not wet and in case dry with an air
flow
check that the connections on the motor and on the
chopper card are correct (verify the type of traction motor
assembled, the correct wiring and the connections on the
chopper VMN, positive and negative)
if the problem persists replace first the chopper card and, if
necessary, also the motor
3 VMN
HIGH
Starting test check possible faults on the power circuit
branch .
Possible causes
-
-
chopper power branch damaged
MOSFET logic control damaged
Action
-
replace the chopper card