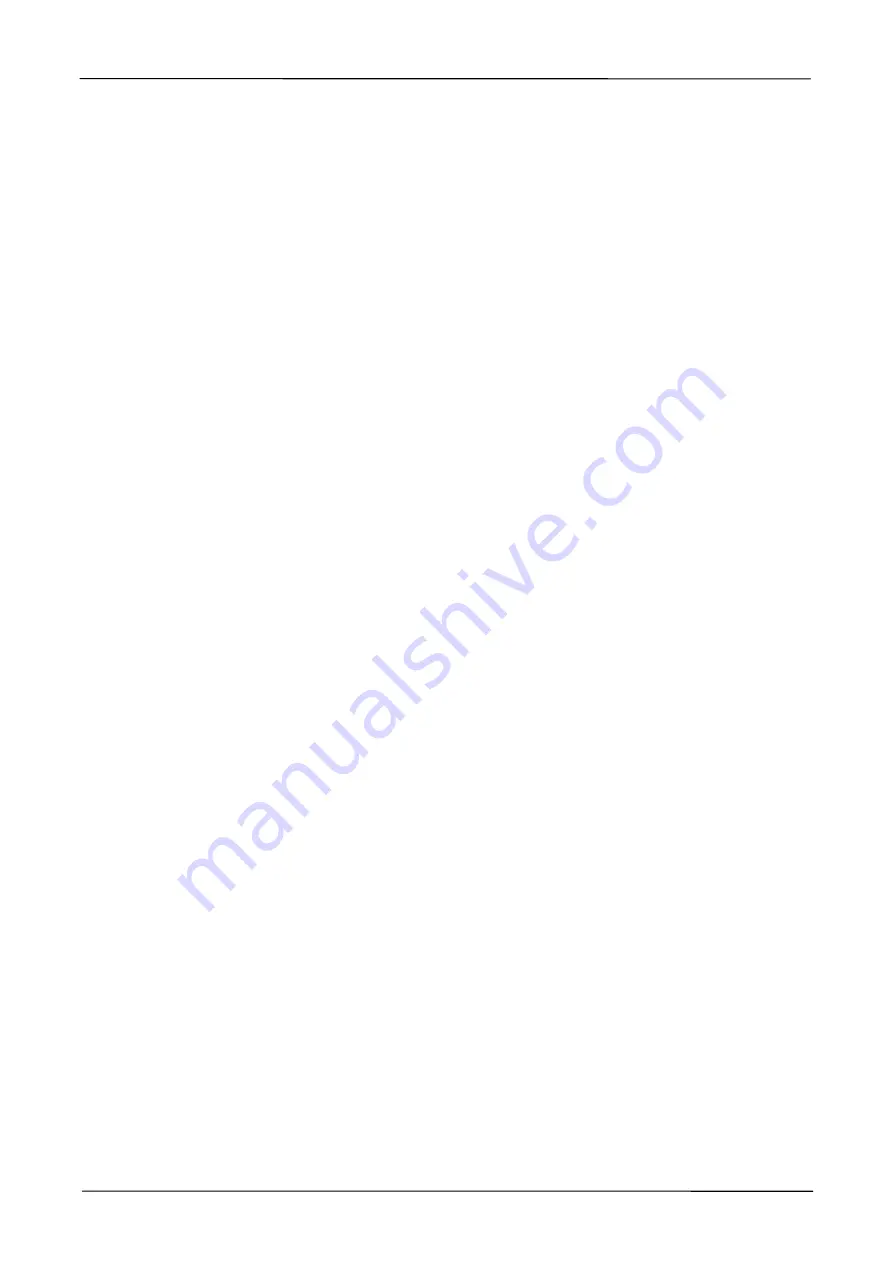
Position control for Servo unit
P3S_I
Data: 13/01/16
Codice: P3S_I Rev 1.0
page 3/14
Description
The controller
P3S_I
combined to the
SERVO_E
positioning unit carries out a particular suitable system for
the automation of machines that require driving of motorized axes.
The inputs of the position controller start, and emergency are opto-insulated.
The values are displayed on a high-brightness 5-digit display (range -9999 +99999) while an auxiliary 2-digit
display shows the program step during execution or the working constants.
The keyboard with 16 keys and 6 function indicators make the use and setting up of the positioning unit very
easy and immediate. The positioning unit can be linked up to 32 Servo units in network and can store up to
99 positioning program.
In order to optimize the positioning accuracy there are some parameters that can balance the system inertia,
clearances, wear and tear of mechanical couplings. Available working modes are: automatic, manual, single
positioning. A relays-output signals the positioning of all axes, a second possible connection error.
Serial connection to SERVO is RS485 with MODBUS RTU protocol. The keeping of data during machine off
is guaranteed by a non-volatile EEPROM memory. Suitable applications are in automatic size change,
motorized adjusting of reference marks, end strokes for cutting and bending.
Installation
Before installing the instrument, read the following warnings:
a) Connect the instrument strictly following the instructions of the manual.
b) Carry out the connections using the correct wires within the limits of the tension and power supply as
indicated in the technical data.
c) The instrument does not have an ON/OFF switch, hence it comes on when connected to the power supply.
For safety reasons, the equipment connected permanently to the power supply requires a bi-phasal selector
switch which should be within easy reach of the operator.
d) If the instrument is connected to any apparatus not isolated electrically, carry out an earth connection to
avoid it being connected directly through the structure of the machine.
d) It is the responsibility of the user to check, before using , the correct settings of the parameters of the
instrument to avoid damage to persons or things.
e) The instrument cannot function in a dangerous environment (inflammable or explosive). It can be
connected to elements that operate in the same atmosphere only through appropriate interfaces, according
to the current safety regulations.
g) Avoid dust, humidity, corrosive gases, heat sources.
Power supply
a) Before connecting the instrument, check that the power supply tension is within the permitted limits and
that it corresponds to the one indicated on the tag.
b) Carry out the electrical connections with the instrument disconnected.
c) For the power line to instruments and sensors, a power supply line separate from that of the power is
required : it is necessary to use an isolating transformer.
d) The power line should provide a device that separates the set fuses of the instruments and should not be
used to regulate relays, contactors, etc.
e) If the network tension is very disordered (eg. from the change-over of the power units, motors, inverters,
welders, etc.), use the appropriate filters of the network.
f) If an earth connection is needed, ensure that the plant has a good earth system: tension between neutral
and earth <1V and the resistance <6 Ohm.