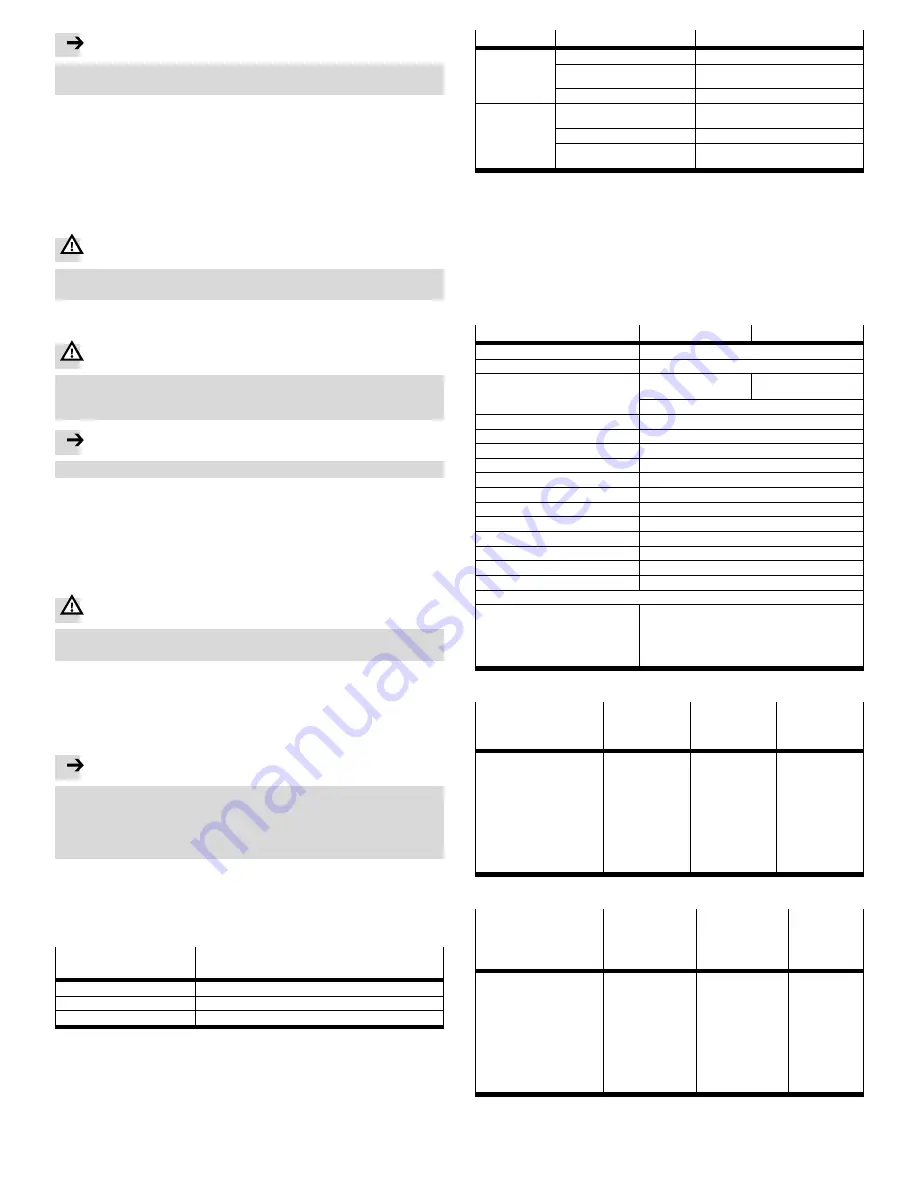
7
Commissioning
Note
• Commissioning should only be conducted by qualified personnel.
• Only little resistance may operate at the valve output.
• Observe the specifications on the rating plate.
• Start up the valve only if it is fully mounted and built-in.
• Check the connection points for tightness.
• Before commissioning, check to ensure the operating conditions and permiss-
ible limit values have been observed (
Technical Data).
8
Operation
• Observe the operating conditions.
• Always observe the permissible limit values.
Warning
Danger of injury from the hot surfaces of the valve.
• Do not touch the valve during operation or immediately afterward.
9
Dismantling
Warning
Danger of injury from the hot surfaces of the valve and pipeline.
Piping system and valve can be hot and under pressure.
• Allow the valve and pipelines to cool and make them pressureless.
Note
The valve should only be dismantled by qualified personnel.
1. De-pressurise the pipeline and valve.
2. Switch off the voltage.
3. Allow the valve and pipeline to cool.
4. Remove the valve from the pipeline (remove the electrical push-in connector and
fittings).
9.1 Dismantling of the solenoid coil
If repairs are required, the solenoid coil can be replaced.
Warning
Danger of injury from the hot surfaces of the valve.
• Do not touch the valve during operation or immediately afterward.
Dismantling:
1. Switch off the voltage.
2. Disconnect the electrical plug connector.
3. Let the solenoid coil and valve cool off.
4. Loosen the retaining nut and remove the solenoid coil from the armature guiding
tube.
Note
With solenoid coils for alternating current (VACN-H1-A1-..A):
A dismounted solenoid coil, when powered, can be destroyed within a short
time.
• Connect a solenoid coil to voltage only if it is correctly mounted on the arma-
ture tube of the basic valve.
10
Accessories
The following table shows appropriate solenoid coils for an armature tube 14 mm
with device plug in accordance with EN 175301-803, form A.
Current information on accessories
www.festo.com/catalogue.
Appropriate solenoid
coils
1)
Characteristic coil data
VACN-H1-A1-1
24 V DC ± 10 %; 11.9 W
VACN-H1-A1-2A
110 V AC ± 10 % (60 Hz); 18.5 VA
VACN-H1-A1-3A
230 V AC ± 10 % (60 Hz); 18.8 VA
1)
Technical data
www.festo.com/catalogue
data sheet
Fig. 3
11
Trouble-shooting
Malfunction
Possible cause
Remedy
Valve does not
close
Valve defective.
• Replace valve.
Flow direction is incorrect.
• Install the valve according to the
terminal identification code.
Nominal voltage still applied.
• Check electrical connection.
Valve does not
open
Solenoid coil or valve defective.
• Replace solenoid coil.
• Replace valve.
Operating pressure is too high.
• Reduce the operating pressure.
Nominal voltage is interrupted or
insufficient.
• Check voltage.
Fig. 4
• Send the defective solenoid coils to our repair service. Information about spare
parts and accessories
www.festo.com/spareparts.
12
Maintenance and care
• Check the valve at least once every 6 months for leakage.
• Check the valve at least once every 6 months for function.
• Clean the exterior of the valve regularly with a soft cloth. The permissible
cleaning agent is soap suds.
13
Technical data
General
VZWE-E-...
VZWE-F-...
Valve function
2/2-way, single solenoid, closed
Manual override MO
None
Design
Corner design
Straight version with
flange
Diaphragm valve
Reset method
Mechanical spring
Type of control
Piloted
Actuation type
Electrical
Mounting position
Any
Sealing principle
Soft
Direction of flow
Non-reversible
Operating medium
Compressed air to ISO 8573-1:2010 [7:4:4]
Note on operating/pilot medium
Operation with lubricated medium not possible
Operating pressure
[bar]
0.35 ... 8
Differential pressure
[bar]
0.35
Ambient temperature
[°C]
–20 ... +60
Protection class
IP65 in accordance with EN 60529
Information on materials
Housing
Screws
Armature tube
Seal
Diaphragm
Die-cast aluminium (EN AC-47100D)
High-alloy steel (1.4301)
High-alloy steel
Nitrile rubber
NBR-PA
Fig. 5
Characteristics
Nominal size
Flow factor
Product weight
[mm]
[m
3
/h]
[kg]
VZWE-E-M22C-M-G34-200-H
VZWE-E-M22C-M-G1-250-H
VZWE-F-M22C-M-G1-250-H
VZWE-E-M22C-M-G112-400-H
VZWE-F-M22C-M-G112-400-H
VZWE-E-M22C-M-G2-500-H
VZWE-F-M22C-M-F600-500-H
VZWE-E-M22C-M-G212-620-H
VZWE-F-M22C-M-F750-620-H
VZWE-F-M22C-M-F890-760-H
20
25
25
40
40
50
50
62
62
76
15
22
22
48
48
78
78
95
95
210
0.420
0.420
0.430
1.300
0.950
2.800
3.300
3.100
3.100
3.600
Fig. 6
Characteristics
Process valve
connection 1
(input)
Process valve
connection 2
(output)
Max.
tightening
torque
1)
[Nm]
VZWE-E-M22C-M-G34-200-H
VZWE-E-M22C-M-G1-250-H
VZWE-F-M22C-M-G1-250-H
VZWE-E-M22C-M-G112-400-H
VZWE-F-M22C-M-G112-400-H
VZWE-E-M22C-M-G2-500-H
VZWE-F-M22C-M-F600-500-H
VZWE-E-M22C-M-G212-620-H
VZWE-F-M22C-M-F750-620-H
VZWE-F-M22C-M-F890-760-H
G
¾
G1
G1
G1
½
G1
½
G2
Flange-
@
60 mm
G2
½
Flange-
@
75 mm
Flange-
@
89 mm
G
¾
G1
Flange-
@
92 mm
G1
½
Flange-
@
106 mm
G2
Flange-
@
145.5 mm
G2
½
Flange-
@
145.5 mm
Flange-
@
162 mm
60
200
200
240
240
300
–
2)
350
–
2)
–
2)
1)
Max. tightening torque for connecting thread
2)
No thread connection present
Fig. 7