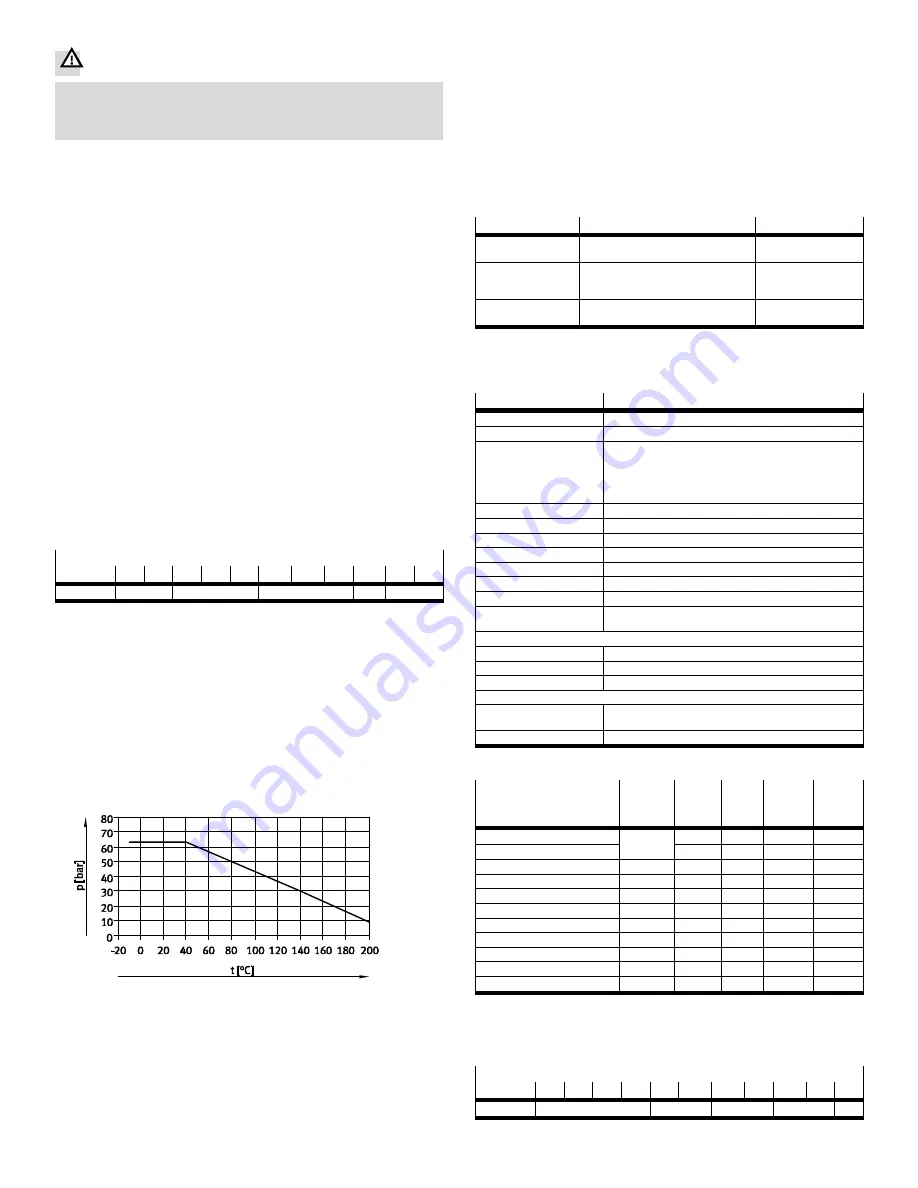
7
Mounting
Assembly and operation only by trained, qualified personnel.
Warning
Danger of crushing! Danger of shearing!
During operation of the ball valve, body parts can be crushed or cut in the orifice
of the ball valve.
Do not reach into the orifice of the ball valve.
Before installation, execute a function test.
The ball valve must be able to be put correctly into the end position. Ball valves
with detectable operative malfunctions must
not
be installed.
Ensure that the equipment is free of stress during installation.
When mounting a semi-rotary drive, observe the documentation for the semi-
rotary drive.
Avoid additional piping connector forces.
The ball valve construction takes typical stress in operation within the tubing into
consideration. Longitudinal or bending forces can occur in piping systems that are
subject to temperature fluctuations.
Use appropriate mountings on the process valve to avoid such forces.
Information for product variants with a 'W' connection type (weld end):
1. To protect the seals in the middle section of the ball valve: Completely dismantle
both connecting flanges from the ball valve and weld on separately.
2. Allow the connecting flanges to cool down and reconnect the middle part, to
gether with the seals, via the tie rods. When doing this make sure the seals are
clean.
3. Tighten the tie rods crosswise and check the connection points for tightness -
for tightening torques
è
Fig. 5
Information for product variants with a 'G' connection type (pipe thread):
The piping connectors of the ball valves have a female thread to EN 10226 and
must be bolted to the tubing with appropriate fittings.
Use appropriate sealing material on the pipe connections.
1. Screw the pipelines into the connecting thread of the ball valve and check the
connection points for tightness.
2. Tighten the tie rods crosswise and check the connection points for tightness -
for tightening torques
è
Fig. 5
Tightening torques Tie rod
VZBA-...-
¼"
y
"
½"
¾"
1"
1¼"
1½"
2"
2½"
3"
4"
[Nm]
10
21
41
70
72
Fig. 5
8
Commissioning
Make sure that the permissible pressure range of the product is not exceeded
(
è
Technical Data).
The actuating elements of the ball valves are harmonised to the maximum forces
of the shaft and ball. Changes to these components are impermissible and can
cause damage.
9
Operation
Make sure that the permissible limit values are adhered to (
è
Technical Data).
Permissible medium pressures are shown in the pressure-temperature diagram
(
è
Fig. 6).
The permissible medium pressure sinks as a function of the temperature of the
medium.
1
2
1
Pressure p [bar]
2
Temperature of medium t [°C]
Fig. 6
Pressure–temperature diagram
10
Maintenance and care
The ball valves VZBA are maintenance-free. For the sake of operational safety, it is
recommended to operate them at least once or twice a year. Depending on the
operating conditions, the ball valves and connection points should be checked for
tightness at regular intervals.
11
Disassembly and repair
Due to the design of closed ball valves, residual fluid may be retained in the ball
passage.
Before dismantling:
Completely relieve the pressure in the tubing and the process valve.
Operate the ball valve to completely drain the ball passage.
Especially with harmful media, make sure:
that no one is in front of the outlet orifice when it opens.
the tubing is completely drained before disassembly, and it must be rinsed in
order to avoid risk from dangerous media.
Repair must be performed only by trained personnel using the set of wearing parts
from Festo. Information about spare parts and auxiliary means can be found at
www.festo.com/spareparts.
12
Troubleshooting
Malfunction
Possible cause
Remedy
Leakage at the switch
ing shaft
Wear of the sealing elements (packing
gland) on the switching shaft
Re-adjust the gland
nut (
è
Fig. 10)
Leakage at the separate
halves of the housing
The housing seal has been crushed
between one or both of the threaded
flanges when inserting the middle part
Replace the housing
seals
1)
Leakage in the ball
valve through-hole
Ball seal damaged by solids in the medium
Replace the ball
seals
1)
1)
Please refer to the spare parts catalogue on the Internet (
è
www.festo.com/spareparts).
Fig. 7
13
Technical data
General data
VZBA-...-63-T-22-...-V4V4T
Process valve connection
è
Type code Fig. 2
Type of mounting
In-line installation
Medium
– Compressed air as per ISO 8573-1:2010 [-:-:-]
– Inert gases
– Water - no water vapour
– Neutral fluids
– Other media on request
Actuation type
Mechanical
Sealing principle
Soft
Mounting position
Any
Flange hole pattern
è
Type code Fig. 2
Design
2-way ball valve
Direction of flow
reversible
Temperature of medium
[°C] –10 ... +200
Process valve nominal
pressure (PN)
63
Materials
– Seals
PTFE, reinforced PTFE
– Housing
high-alloy stainless steel (1.4408)
– Ball, shaft
high-alloy stainless steel (1.4401/1.4408)
CE mark (see declaration of conformity
è
www.festo.com)
– VZBA-¼" to VZBA-1"
no, in accordance with EU Pressure Equipment Directive, art.3,
par.3
– VZBA-1¼" to VZBA-4"
yes, in accordance with EU Pressure Equipment Directive
Fig. 8
VZBA-...-63-T-22-...-V4V4T
Actuating
torque
Flow
rate Kv
I.D.
Nominal
size (DN)
Product
weight
[Nm]
1)
[m
3
/h]
2)
[mm]
3)
[g]
...-
¼
"-...-63-T-22-F0304-V4V4T
6
7
10
8
650
...-
y
"-...-63-T-22-F0304-V4V4T
10
12
10
650
...-
½
"-...-63-T-22-F0304-V4V4T
10
19.4
16
15
650
...-
¾
"-...-63-T-22-F0304-V4V4T
14
45.6
20
20
850
...-1"-...-63-T-22-F0405-V4V4T
17
71.5
25
25
1250
...-1
¼
"-...-63-T-22-F0405-V4V4T
24
105
32
32
1850
...-1
½
"-...-63-T-22-F0507-V4V4T
29
170
38
40
2800
...-2"-...-63-T-22-F0507-V4V4T
44
275
50
50
4550
...-2
½
"-...-63-T-22-F0710-V4V4T
78
507
65
65
9200
...-3"-...-63-T-22-F0710-V4V4T
112
905
80
80
13950
...-4"-...-63-T-22-F10-V4V4T
140
1414
100
100
22300
1)
Torque required for actuation at PN; dependent on pressure, temperature and medium
2)
Flow rate of water at 15 °C and at a differential pressure of 1 bar, measured in accordance with
VDI/VDE 2173
3)
Smallest flow diameter
Fig. 9
Tightening torques Gland nut
VZBA-...-
¼"
y
"
½"
¾"
1"
1¼"
1½"
2"
2½"
3"
4"
[Nm]
2,5
3,4
5,9
19,6
24,5
Fig. 10