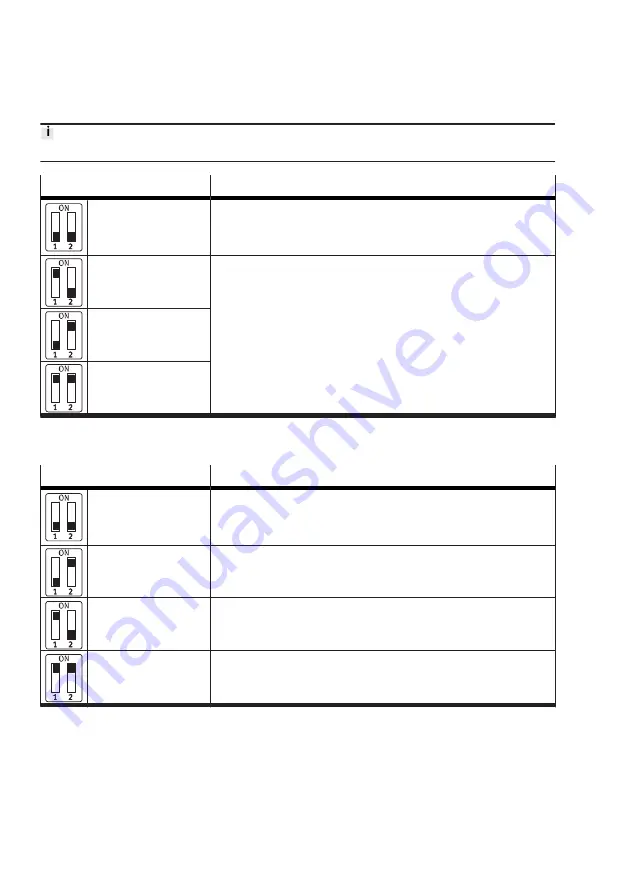
54
Festo — MSE6-E2M — 2022-08d
Commissioning
Setting operating mode, DIL switch 1
All switch elements of the DIL switch 1 must be in the OFF position.
DIL switch 1
Setting operating mode
DIL 1.1: OFF
DIL 1.2: OFF
(factory setting)
Remote I/O operating mode
All functions of the energy efficiency module are controlled directly
by the controller or by a higher-level PLC.
DIL 1.1: ON
DIL 1.2: OFF
Not supported by the energy efficiency module.
DIL switch elements 1.1 and 1.2 must be in the OFF position.
DIL 1.1: OFF
DIL 1.2: ON
DIL 1.1: ON
DIL 1.2: ON
Tab. 39: Setting the operating mode with DIL switch 1
Setting diagnostic mode, DIL switch 2
DIL switch 2
Setting operating mode, in remote I/O operating mode
DIL 2.1: OFF
DIL 2.2: OFF
(factory setting)
The ‘E/A-Diagnose-Interface’ and status bits are switched off or
the diagnostics mode is set via the hardware configuration of the
configuration software
1)
, + 0 byte I/0 byte O
DIL 2.1: OFF
DIL 2.2: ON
The status bits are on, + 1 byte I/0 byte O
2)
DIL 2.1: ON
DIL 2.2: OFF
The I/O diagnostics interface is switched on, + 2 bytes I/2 byte O
3)
DIL 2.1: ON
DIL 2.2: ON
Reserved for future extensions
1) Revision 21 and above
2) Status bits occupy 1 byte of address space, 8 I bits
3) The I/O diagnostics interface occupies 4 bytes address space, 16 I and 16 O bits
Tab. 40: Setting diagnostic mode using DIL switch 2
8.6.5
Commissioning and configuration
Commissioning and configuration of the bus node depend on the higher-order control.