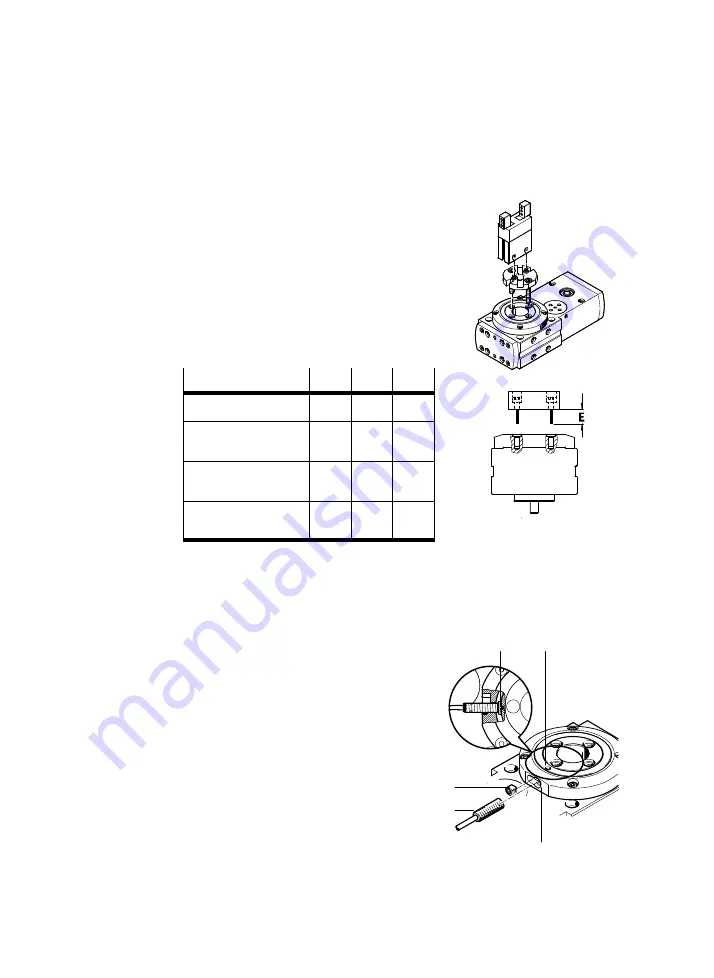
ERMB
Festo ERMB 2018-12a English
9
Fitting the work load
S
Place the centre of gravity of the work
load if possible centrically to the drive
shaft.
S
Fasten the work load to the drive shaft
with at least 2 screws and 2 centring
sleeves (diagonal) or with the aid of kits.
ERMB-...
20
25
32
Screw
M4
M6
M6
Tightening
torque
[Nm]
2.9
9.9
9.9
Max. screw-
in depth E
[mm]
9.6
12
12
Centring
sleeves
[mm]
dia.
7x3
dia.
9x4
dia.
9x4
Fig. 8
Fitting electric components
Fitting an inductive proximity switch as reference switch:
1. Turn the drive shaft until the marking
hole (A) reaches the threaded hole
6
.
2. Push the clamping element (C) into the
recess intended for this.
3. Screw the proximity switch (D):
– at first into the hole
6
until it touches
the switching cam (B).
– then unscrew it approx. 0.6 of a turn
(
o
0.6 mm).
4. Screw the threaded pin (
ß
2.5) into the
clamping unit (C). The tightening torque
is 0.8 Nm.
Fig. 7
Fig. 9
(A)
(B)
(C)
(D)
6