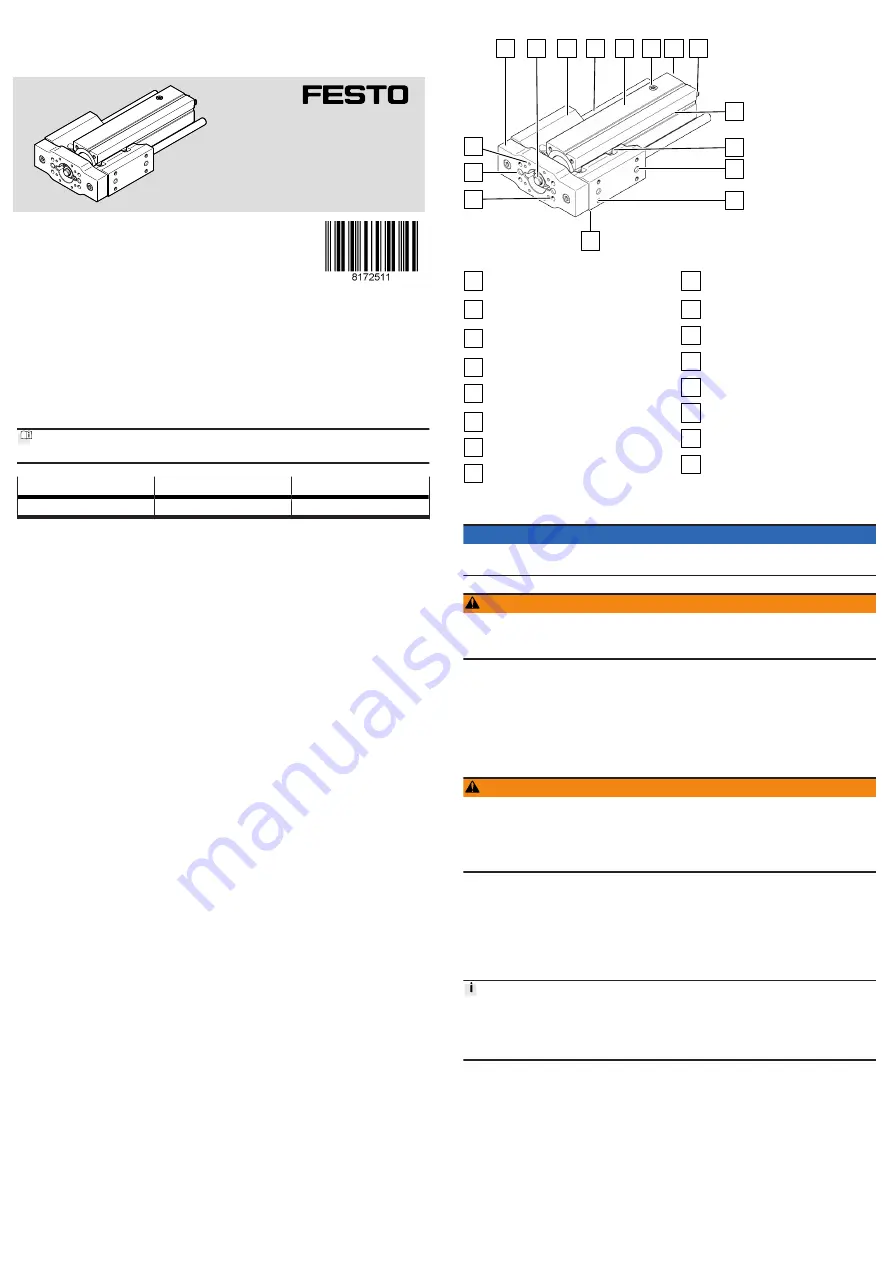
EPCC-BS-KF
Electric cylinder
Festo SE & Co. KG
Ruiter Straße 82
73734 Esslingen
Deutschland
+49 711 347-0
www.festo.com
Operating instructions
8172511
2022-03
[8172513]
Translation of the original instructions
© 2022 all rights reserved to Festo SE & Co. KG
1
Applicable documents
All available documents for the product
Document
Product
Contents
Assembly instructions
Guide unit EAGF-P2-KF
–
Tab. 1: Applicable document
2
Safety
2.1
Safety instructions
–
Observe labelling on the product.
–
Before working on the product, switch off the power supply and secure it
against being switched on again.
–
Store the product in a cool, dry environment protected from UV and corrosion.
Keep storage times short.
–
Store the product in ambient conditions without oils, greases and grease-dis-
solving vapours.
2.2
Intended use
The electric cylinder with guide unit is used as intended for positioning payloads
in connection with tools.
2.3
Training of qualified personnel
Work on the product may only be carried out by qualified personnel who can
evaluate the work and detect dangers. The qualified personnel have knowledge
and experience in dealing with electric drive systems.
3
Additional information
–
Contact the regional Festo contact if you have technical problems
–
Accessories and spare parts
4
Product overview
4.1
Function
The electric cylinder converts the rotary motion of the mounted motor into a
linear motion of the piston rod. The drive screw converts the torque of the motor
into a feed force. The linear movement of the piston rod is guided by two guide
rods of the guide unit. Sensors monitor end positions, reference position and
intermediate position.
4.2
Product design
1
2
3
4
5
6
7
8
9 10 11
12
13
14
15
16
Fig. 1: Product design EPCC-BS-KF, example EPCC-BS-45-100-10P-A-KF
1
Through-hole for attachment
component
2
Centring hole for attachment
component
3
Threaded hole for attachment
component
4
Yoke plate
5
Piston rod with male thread or
female thread
6
Guide housing
7
Guide rod
8
Cylinder profile
9
Sealing air connection with filter
element
10
Interface for motor mounting kit
11
Drive hub
12
Slot for sensor bracket
13
Through-hole for mounting
14
Centring hole for mounting
15
Threaded hole for mounting
16
Threaded hole and centring hole
for mounting
5
Transport
NOTICE
Unexpected and unbraked movement of components
• Secure moving components for transport.
WARNING
Risk of injury due to falling product
If the product is lifted incorrectly, it may fall and cut, crush or separate body parts.
• Lift the product only with suitable load-bearing equipment.
–
Store and transport the product in its original packaging. Observe the weight,
the dimensions and the ambient conditions.
–
Take the centre of gravity of the product into consideration.
–
Store and transport the product in a horizontal position.
6
Assembly
6.1
Safety
WARNING
Risk of Injury due to Unexpected Movement of Components
For vertical or slanted mounting position: when power is off, moving parts can
travel or fall uncontrolled into the lower end position.
• Bring moving parts of the product into a safe end position or secure them
against falling.
6.2
Unpacking product
1. Open packaging.
2. Remove all transport materials, e.g. foils, caps, cardboard boxes.
3. Remove the product from the packaging and place it on the mounting surface.
4. Dispose of packaging and transport materials.
6.3
Mounting motor
Transverse load on the drive hub
When mounting the motor and motor mounting kit, do not exceed the maximum
transverse load F
R
of the drive hub, e.g. toothed belt tension when mounting the
parallel kit