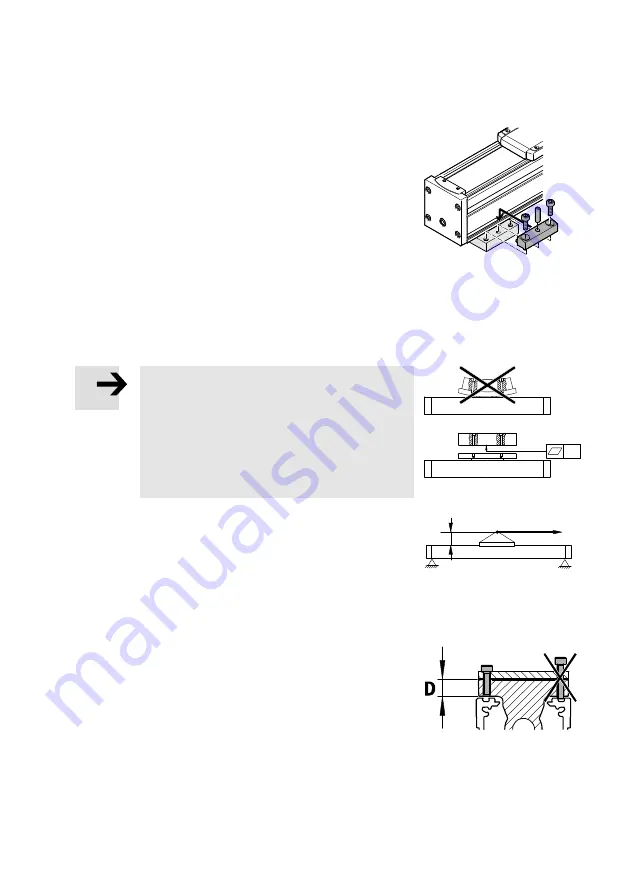
ELFC-KF
Festo – ELFC-KF – 2017-02 English
7
7.2
Mounting
Select mounting components
è
www.festo.com/catalogue.
Mount the mounting components outside the positioning range
to avoid collisions.
Fasten axis to the profile (e.g. with profile mounting EAHF-L2).
Tighten screws evenly.
Fig. 4
7.3
Attachment
Prerequisites
Note
A warped attachment component bends the slide
and shortens the service life of the guide.
Use an attachment component with an even
surface.
Evenness: t = 0.01 mm
Fig. 5
t
Place rated load in such a way that the break-down torque res
ulting from force F (parallel to the axis of motion) and lever arm
“a” are kept as small as possible
è
Avoid collisions of the mounting part and payload with other
mounting parts
a
F
Fig. 6
Mounting
Fasten the attachment to the slide with screws and centring
sleeves. Observe screw-in depth D and tightening torque
è
For attachment components with their own guide:
Adjust the guide and axis so that they are exactly parallel, or use
a connection that permits tolerance compensation. In this way,
the guide is not overloaded.
Fig. 7