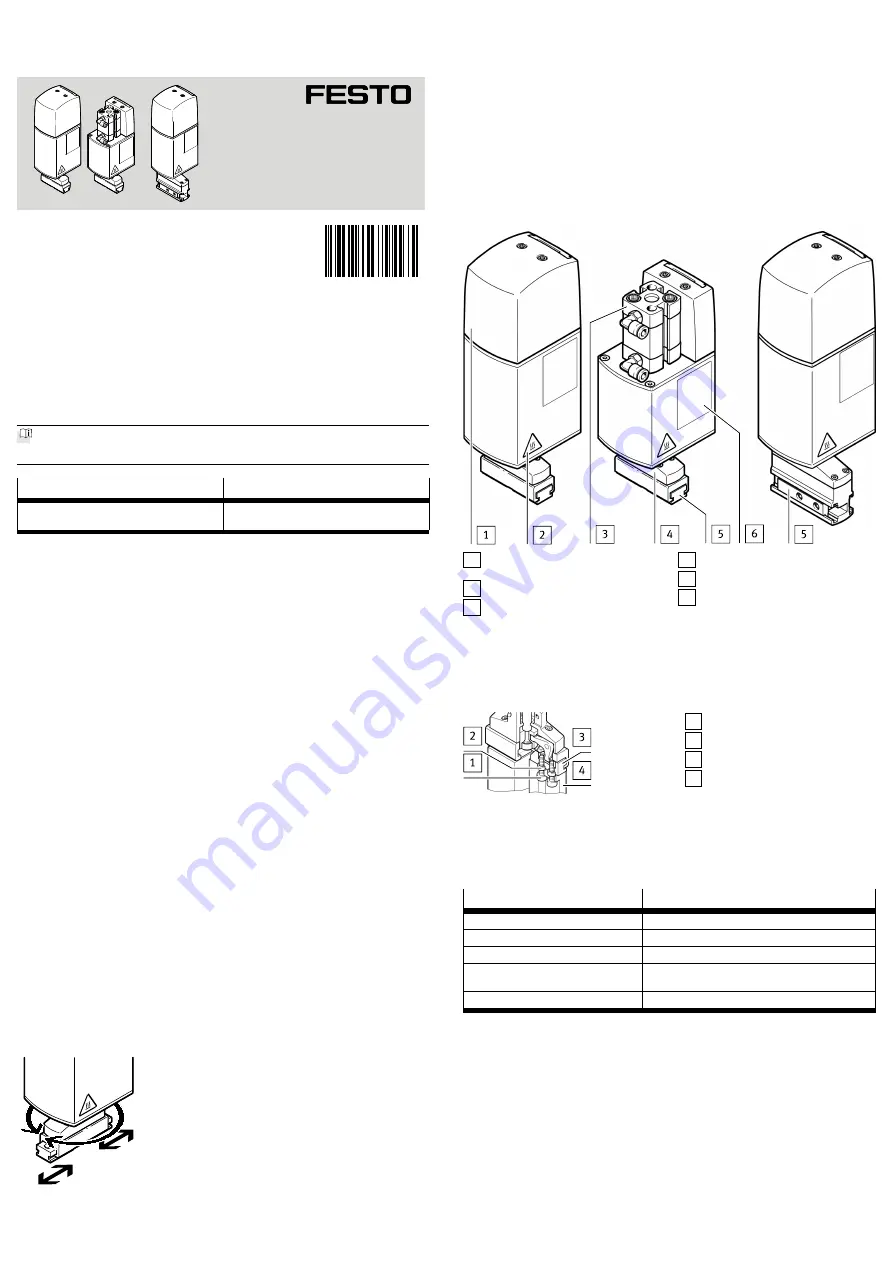
Translation of the original instructions
1
About this document
1.1
Applicable documents
All available documents for the product
è
Identifier
Contents
Application note
Application examples for connection and com
missioning
Tab. 1 Documentation for rotary gripper module
2
Safety
2.1
General safety instructions
–
Only use the product in original status without unauthorised modifications.
–
Only use the product if it is in perfect technical condition.
–
Observe labelling on the product.
–
Store the product in a cool, dry, UVprotected and corrosionprotected envir
onment. Ensure that storage times are kept to a minimum.
–
Prior to mounting, installation and maintenance work: Switch off power sup
ply and secure it from being switched back on.
–
Observe tightening torques. Unless otherwise specified, the tolerance
is ± 20 %.
2.2
Intended use
The intended use of the product is to grip, hold and rotate payloads (workpieces).
2.3
Foreseeable misuse
Gripping where the point of application is on the inside is not intended.
EHMD...GE: In normal operation, hitting the stop when moving in the opening
direction is not intended.
2.4
Training of qualified personnel
Only qualified personnel may perform installation, commissioning, maintenance
and disassembly of the product.
The qualified personnel must be familiar with the installation and operation of
electrical and pneumatic control systems.
3
Additional information
–
Accessories
è
4
Service
Contact your regional Festo contact person if you have technical questions
è
5
Product overview
5.1
Functional principle
Fig. 1 Functional principle
The product is a combined rotating and gripping module. Gripping occurs in the
closing direction of the gripper jaws (point of application on the outside).
The parallel gripper can be actuated electrically (EHMD...GE) or pneumatically
(EHMD...GP), depending on version.
In both versions, the parallel gripper can be continuously rotated by means of the
electric axis of rotation.
Gripping force backup
EHMD...GP: without gripping force backup. Backup for the gripping force can
only be ensured using additional measures (e.g. uninterruptible compressed air
supply).
EHMD...GE: with gripping force backup. If the power supply is interrupted, a min
imum gripping force is ensured by the mechanical design. However, the maximum
gripping force cannot be maintained.
5.2
Product design
EHMD-40-RE-GE | EHMD-40-RE-GP | EHMD-40-RE-GE-16
1 Stepper motor for the gripper func
tion (installed in the housing)
2 Warning hot surface
3 Pneumatic cylinder for gripper
function
4 Rotatable gripper module
5 Gripper jaw
6 Product labelling
Fig. 2 Product design
6
Mounting
6.1
Mounting the gripper fingers (EHMD-40-RE-GE/-GP)
1 Screw
2 Centring sleeve
3 Gripper jaw
4 Gripper jaw blank (not in scope of
delivery)
Fig. 3 Mounting the gripper fingers
1. Press centring sleeves
2
into locating holes in the gripper jaws
3
.
2. Apply mediumstrength screw locking agent to socket head screws
1
.
3. Position gripper fingers
4
on the gripper jaws
3
.
4. Screw in socket head screws
1
. Comply with the tightening torque.
EHMD-40-RE-...
-GE/-GP
Centring hole
[mm]
5
H9
Centring sleeve
ZBH5
Threaded hole
M3
Max. screwin depth in grip
per jaw
[mm]
8.3
Tightening torque
[Nm]
1.2
Tab. 2 Mounting the gripper fingers
8108367
EHMD-40-RE-...
Rotary gripper module
8108367
201906a
[8108369]
Instructions | Use
Festo
SE
& Co. KG
Ruiter Straße 82
73734 Esslingen
Germany
+49 711 3470
www.festo.com