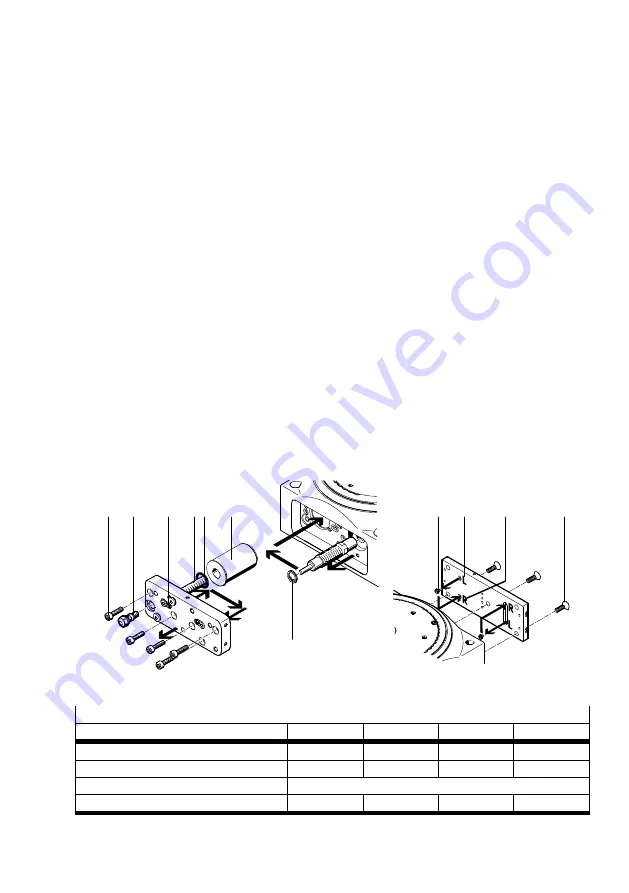
DHTG
Festo – DHTG – 2018-02e English
15
Conversion from clockwise rotation (as supplied) to anti-clockwise rotation:
1. Loosen the clamping element (K) of the adjusting screw one rotation.
2. Unscrew the adjusting screw
6
a few rotations.
3. Unscrew flow control screw
aJ
and the fastening screws (M) from the sub-base.
4. Using pliers, remove the retaining ring (S) on the shock absorber.
5. Fit the following:
–
the shock absorber with the retaining ring in the adjacent hole
–
the O-ring (P) / buffer (for DHTG-65) in the adjacent groove
–
the distance piece (T) in the same hole (distance piece omitted for 2/3 index stations)
–
the sub-base with the fastening screws and the flow control screw in reverse sequence
(tightening torque
è
6. Unscrew the fastening screws (N) on the stop plate.
7. Unscrew:
–
both locking screws (O) on the rear of the stop plate to begin with,
–
then screw them in again into the open holes (tightening torque
è
The open holes
(R) or (L)
in Fig. 14 determine the direction of rotation
(Holes (R) open: clockwise rotation).
8. Screw the fastening screws (N) on the stop plate again (tightening torque
è
The rotary indexing table remains pneumatically controlled as before.
9. Screw in the adjusting screw
6
until the desired cushioning is achieved
è
10.Tighten the clamping element (K) of the adjusting screw (tightening torque
è
(M)
aJ
(N)
(O)
(P)
(K)
(L)
(R)
(T)
(S)
6
Fig. 14
Tightening torque
Size
65
90
140
220
Flow control screw
aJ
[Nm]
1.5
1.5
5.5
5.5
Fastening screws (M)
[Nm]
2.9
2.9
9.9
9.9
Plug screw (O)
[Nm]
0.5
Fastening screws (N)
[Nm]
1.5
2.9
5.9
5.9
Tab. 17