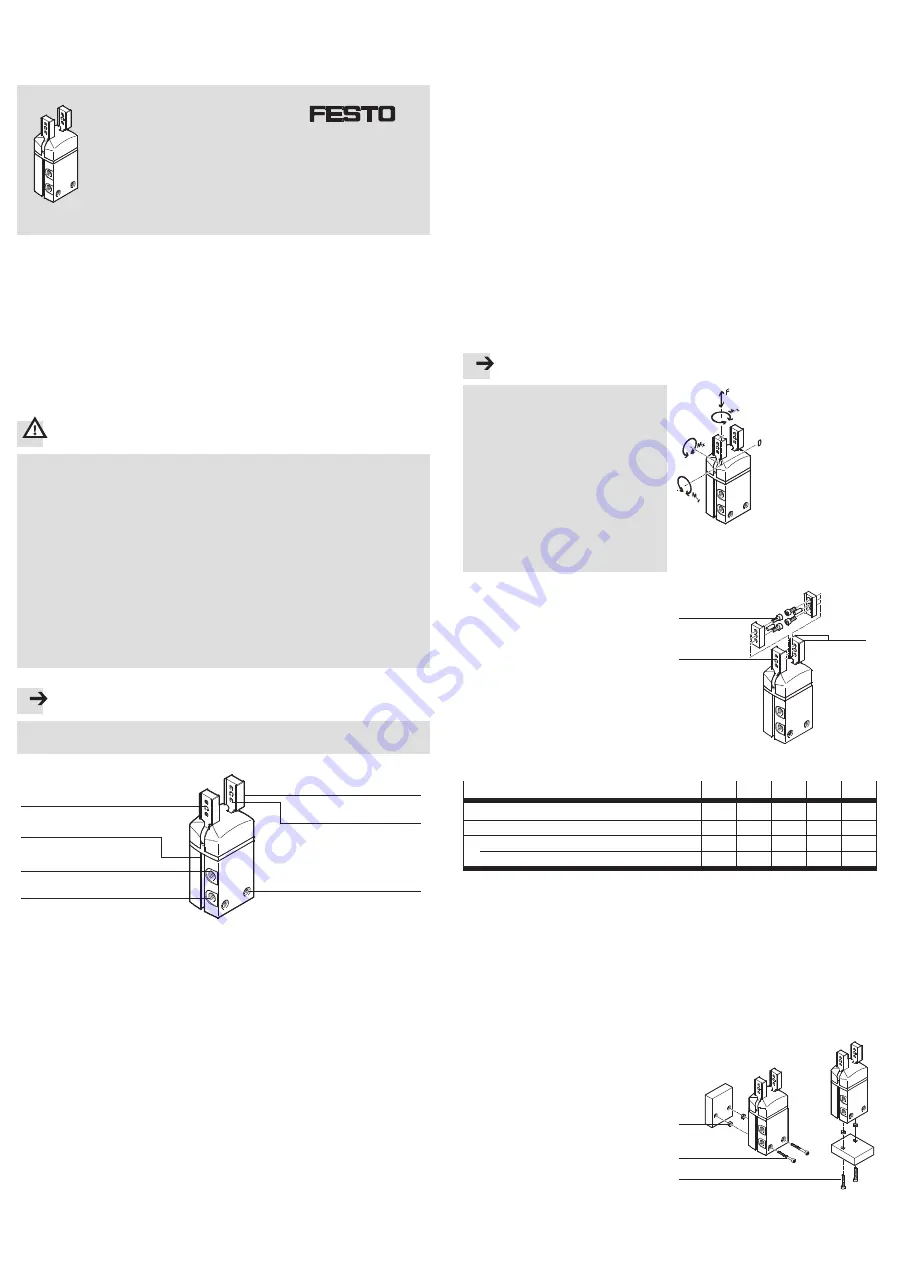
DHRS Radial Gripper
Festo AG & Co. KG
Postfach
D-73726 Esslingen
++49/711/347-0
www.festo.com
Operating instructions
757758
1103NH
Original: de
DHRS Radial Gripper
English
. . . . . . . . . . . . . . . . . . . . . . . . . . . . . . . . . . . . . . . . . . .
Warning
During commissioning and operation:
Moving masses can cause injury to people (crushing) or damage to property.
• Make sure that, in the gripping area,
– no one places their hands between the gripper fingers,
– there are no foreign objects in the gripping area (e. g. by means of a protective
screen)
When exhausting (without locking the gripping force):
• Make sure that the gripper is not holding an effective load.
In this way you can prevent a mass from falling down suddenly.
When dismantling the gripper:
High spring forces fling the components outwards with the DHRS-…-NC (risk of
injury).
• Ensure that the piston is preloaded to 210 N.
Note
Installation and commissioning are to be carried out only by qualified personnel
in accordance with the operating instructions.
1
2
3
4
7
5
6
Fig. 1: Control sections and connections
1
Function and application
When the compressed air connections
4
and
5
are pressurised alternately, an
internal piston is moved backwards and forwards. A mechanism transfers the
movement of the piston to the gripper jaws
1
, to which gripper fingers are
fastened.
The opening and closing action of the gripper fingers enables them to grasp work-
ing loads by their outer or inner contour (double-acting). In conjunction with the
integrated reset spring, the DHRS-…-NC can also be operated in single-acting
mode and for locking the gripping force. If the gripper is exhausted, this spring
returns the gripper jaws and pistons to their initial positions (gripper fingers closed
with DHRS-…-NC).
The DHRS radial gripper is intended for gripping and holding effective loads.
2
Requirements for product use
• Compare the maximum values specified in these operating instructions with
your actual application (e.g. pressures, forces, torques, temperatures, masses,
speeds). Only compliance with the load limits allows operation of the product in
compliance with the relevant safety regulations.
• Take into consideration the ambient conditions at the location of use.
Corrosive elements in the environment (e.g. ozone) will reduce the service life of
the product.
• Ensure that the compressed air is properly prepared (
11 Technical data).
• Maintain the selected medium for the complete service life of the product.
Example: Always use unlubricated compressed air.
• Pressurize the total system slowly. This will prevent uncontrolled movements
from occurring. For slow start-up pressurisation, use on-off valve HEL.
• Comply with the regulations of the trade association, the German Technical
Control Board or relevant national regulations.
• Remove all transport packaging such as foils, caps and cartons (except for any
plugs in the pneumatic connections).
The packing is intended for recycling on a material-sensitive basis (except for:
oiled paper = other waste).
• Use the product in its original condition without any unauthorised modifica-
tions.
• Note the warnings and instructions on the product and in the relevant operating
instructions.
• Take the tolerance of the tightening torques into account.
Unless otherwise specified, the tolerance is ±20 %.
3
Mechanical installation
Note
Excessive tightening torques during
mounting will damage the gripper
mechanism.
• Make sure that the maximum
permissible tightening torques are
not exceeded.
• Observe the maximum permissible
values for the following
characteristics
(
11 Technical data):
– Force F
– Torques Mx, My and Mz.
Fig. 2
Fitting the gripper fingers:
1. Position the gripper fingers with the
centring pins on the fitting hole
7
of
the gripper jaw
1
.
2. Fasten the gripper fingers with two
mounting screws each
8
to the
threaded holes.
Refer to the following table for the
characteristics.
7
8
1
Fig. 3
Size
10
16
25
32
40
Fitting
∅
centring pin [H8]
7
[mm]
2
2
3
4
5
Land width on gripper jaws [–0,03]
1
[mm]
6.5
10
13
14
20
Screw
8
M2.5
M3
M4
M5
M6
Tightening torque
[Nm]
0.7
1.2
2.9
5.9
10
Fig. 4
If proximity sensors are used:
• Observe the following points:
– Interference caused by ferritic mounting parts (e. g. by mounting screws made
of ferritic steel)
– Possibly protruding proximity sensors.
When sensing both piston end positions:
• Push the proximity switches into separate grooves
6
.
• Make sure there is sufficient room for the connection elements.
Fitting the gripper:
• Fasten the DHRS as follows:
1. Press two centring sleeves
9
into the
fitting holes.
2. Place the gripper on the connection
surface.
3. Turn the screws
aJ
/
aA
for fastening.
Refer to the following table for the
characteristics:
9
aA
aJ
Fig. 5