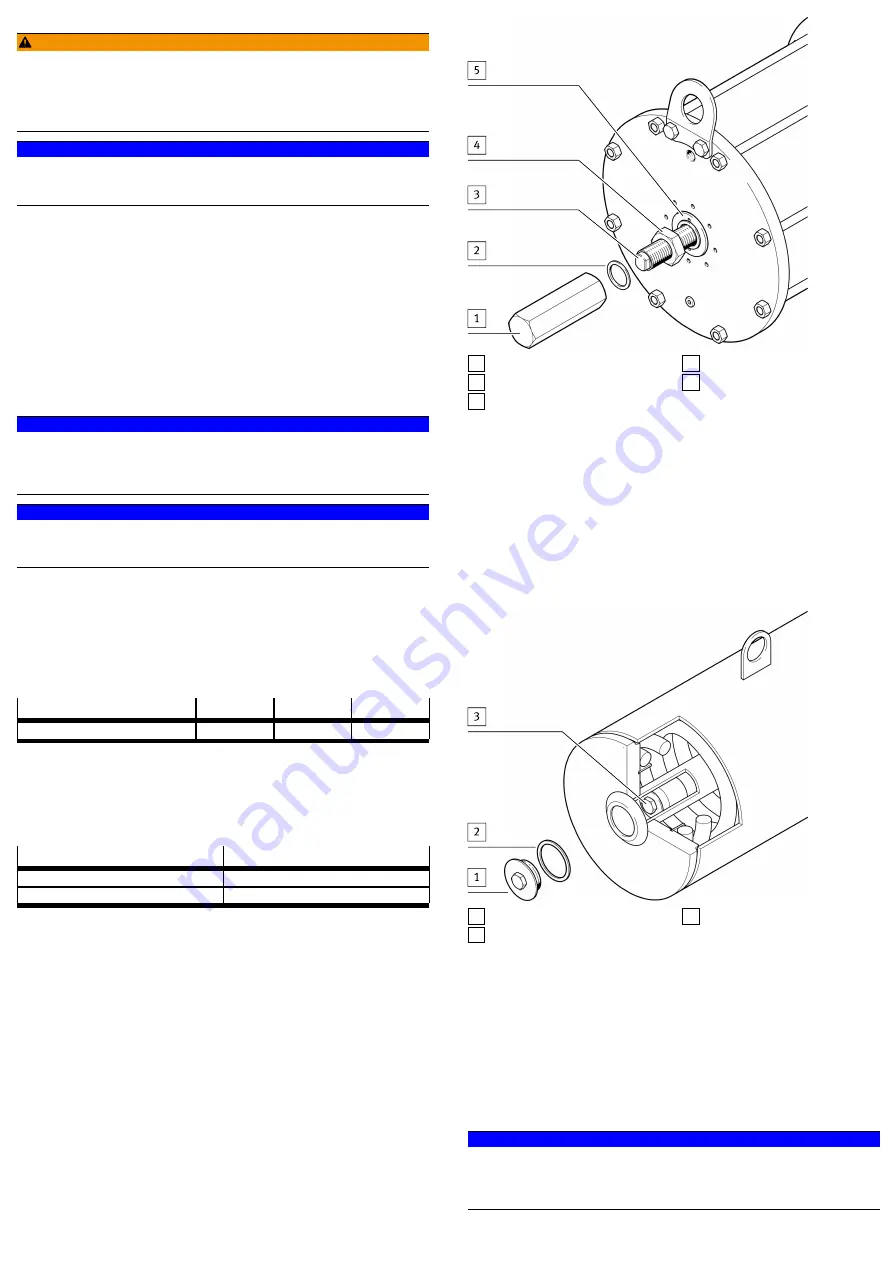
6
Transport and storage
WARNING!
Danger of crushing.
Body parts can be crushed if the product falls.
•
Use appropriate load handling equipment.
•
Lift the semi-rotary drive using the transport lugs.
•
Before transporting: detach the semi-rotary drive from the process valve.
NOTICE!
For variants with a hydraulic unit (DFPD-HD-...-HP): environmental damage due to
escaping oil.
•
Store the product horizontally and avoid inclines.
–
When dispatching used products: comply with all legal requirements for the
handling of hazardous substances and the transport of dangerous goods. For
return to Festo
è
2.1 General safety instructions.
–
Remove all attachments.
–
Store the product in a cool, dry, UV-protected and corrosion-protected envir-
onment. Ensure that storage times are kept to a minimum.
–
For long-term storage: test the function of the product regularly.
–
Observe environmental and storage conditions
è
–
Seal pneumatic connections.
–
Protect coupling parts with grease or protective oil.
–
To prevent damage to the coupling flange, store the product on a level
wooden pallet.
7
Mounting and installation
NOTICE!
Semi-rotary drives of the series DFPD-HD are intended for installation parallel to
the line axis.
•
If another installation position is necessary, consult your regional Festo con-
tact
è
NOTICE!
Semi-rotary drives with a hydraulic manual override are designed for a horizontal
installation position only. In this position, the pump and reservoir are mounted
towards the top of the hydraulic cylinder.
7.1
Assembly
1. Clean the coupling flange.
2. Adjust the valve position according to the semi-rotary drive settings.
3. Lubricate the valve spindle.
4. Place the semi-rotary drive on the control shaft of the process valve.
5. Mount the semi-rotary drive on the connecting flange of the process valve
with 8 threaded pins.
Tightening torque
è
Flange type
F25
F30
F35
Tightening torque
[Nm]
160
320
1100
Tab. 2
7.2
Pneumatic installation
•
Observe the operating instructions of the process valve.
•
Test the correct function of the pneumatic control.
•
Take precautions at the open port 4, which prevent the suction of harmful
substances, e.g. unfiltered outside air, humidity or water, into the product.
Connection
Effect
2
Air supply
4
Port remains open to the environment
Tab. 3
8
Commissioning
8.1
Requirements
–
The drive is fully mounted and connected.
8.2
Commissioning the semi-rotary drive
1. Check operating conditions and critical limits
è
2. Switch on the compressed air supply.
3. Check the semi-rotary drive for leakage.
4. First check the direction of rotation of the semi-rotary drive and reaction of
the process valve at a low travel speed.
8.3
Adjusting the end positions
8.3.1
"Valve closed" end position
The "Valve closed" end position is set at the pneumatic cylinder.
1 Stop bolt covering
2 Sealing washer
3 Stop adjusting screw
4 Stop nut
5 Sealing washer
Fig. 4 Adjust "valve closed" end position
1. Pressurise the connection (2) slightly to relieve the stop bolt.
2. Remove stop bolt
and sealing washer
3. Loosen the stop nut
together with the sealing washer
4. To reduce the rotation angle, screw in the stop adjusting screw
.
To increase the rotation angle, screw out the stop adjusting screw
. Make sure that the sealing washer
the stop nut and lies in the recess of the flange.
6. Run through a complete cycle to test the setting.
7. Replace stop bolt
8.3.2
"Valve open" end position
The "valve open" end position is set at the spring package.
1 Stop cap
2 Sealing washer
3 Stop adjusting screw
Fig. 5 Adjust "valve open" end position
1. Switch off the compressed air supply to relieve the spring.
2. Remove the stop cap
3. To reduce the rotation angle, screw in the stop adjusting screw
.
To increase the rotation angle, screw out the stop adjusting screw
4. Switch on the compressed air supply.
5. Run through a complete cycle to test the setting.
6. Replace the stop cap
.
9
Operation and use
•
Comply with operating conditions.
•
Comply with permissible critical limits.
NOTICE!
For continuous operation under extreme conditions: Use lubricated compressed
air. The oil must be chemically inert and must not carbonise. Once the product has
been used with lubricated compressed air, it must continue to be operated with
lubricated compressed air only.